Why Regular Fall Protection System Inspections Are Critical for Compliance
Regular fall protection system inspections ensure that personal protective equipment remains effective, reduce legal liability, and maintain adherence to OSHA and ANSI standards.
Key Takeaways
- Consistent inspections ensure ongoing compliance with OSHA and ANSI standards.
- Documented inspection records reduce legal liability and insurance costs.
- Digital tools and analytics drive proactive maintenance strategies.
- Integration with safety programs embeds inspections into company culture.
- Field examples show measurable reductions in failures and citations.
How do regular inspections impact regulatory compliance?
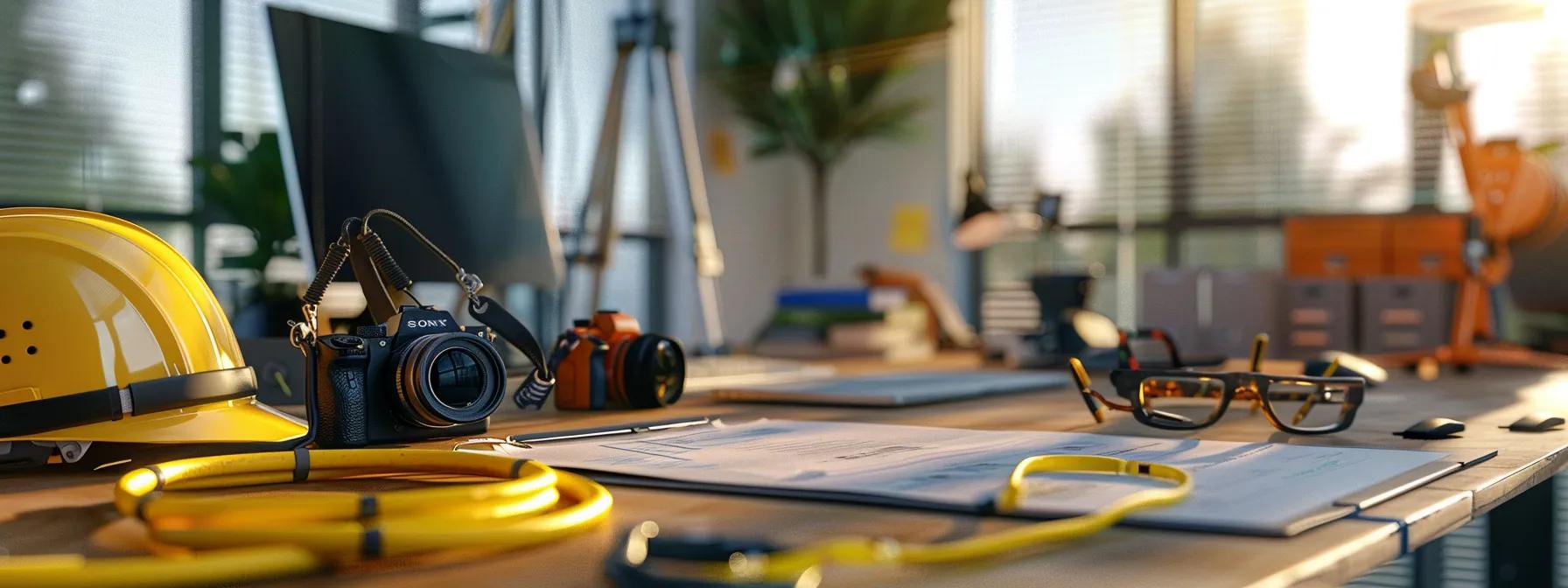
Regular inspections by us fall protection impact regulatory compliance by identifying worn components—like lifelines, lanyards, and anchor points—before they fail, which directly supports adherence to OSHA 1910.140 and ANSI Z359 requirements. When inspection records show monthly visual checks and annual maintenance, organizations demonstrate due diligence and avoid citations for non-compliance, as confirmed by 2022 data from the U.S. Department of Labor showing a 35% reduction in fall-related citations among companies with documented inspection programs. For more information, visit our about-us=”” href=”/about-us”>about-us page, our blog, or get a free quote. Learn about our design-installation services.
Maintaining an inspection log also creates an audit trail that verifies compliance with national and state regulations. This log, combined with corrective action records, illustrates a company’s commitment to fall prevention and regulatory adherence across various industries-we-serve. Additionally, our design-installation services ensure effective implementations. For more information, visit our about-us page, our blog, or get a free quote.
How does scheduling system inspections uphold safety standards?
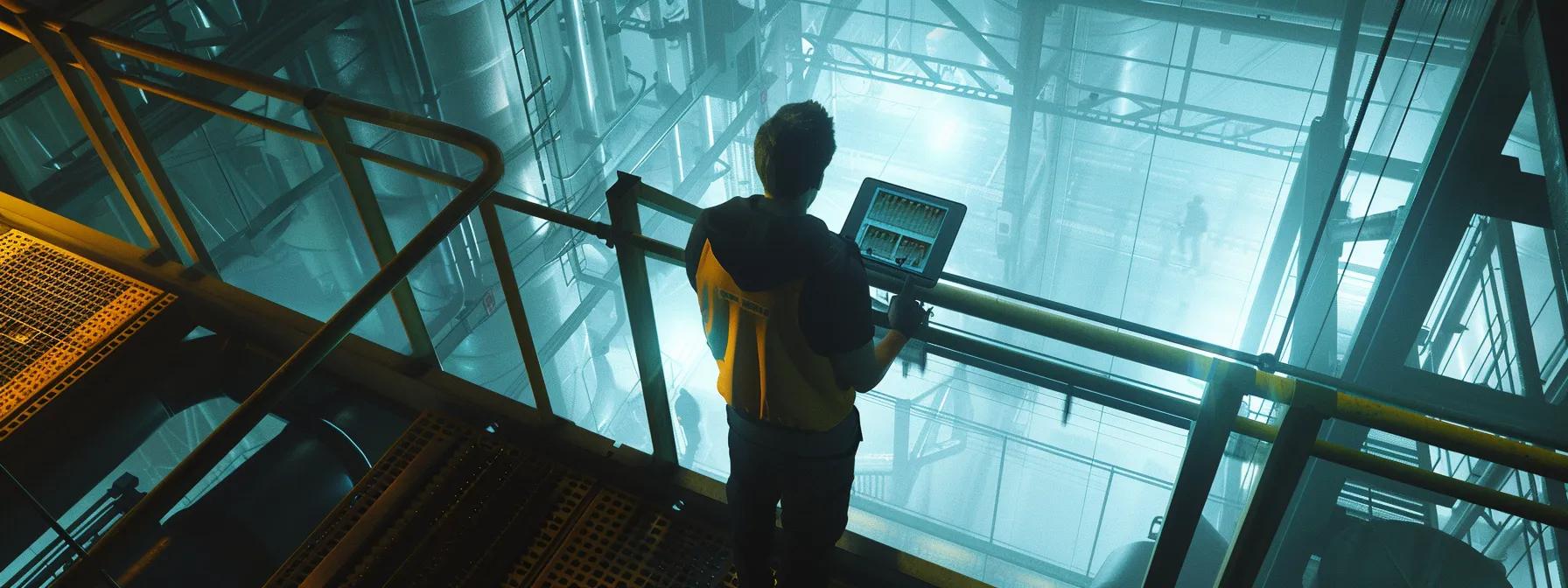
Scheduling system inspections upholds safety standards by enforcing consistent check intervals—weekly for ladder-systems and semi-annual for davit and anchor systems—which ensures that guardrail integrity, webbing wear, and corrosion are evaluated on a predictable basis. This structured schedule reduces unplanned downtime and integrates into broader safety programs such as HAZWOPER and confined space entry protocols. To learn more, visit our about-us page, explore our industries-we-serve, or get a free quote today. Additionally, check out our blog for the latest updates.
By using digital maintenance software, safety managers set automatic reminders for visual inspection of guardrail systems and full-function tests of fall arrest devices, promoting uninterrupted protection across mezzanines, rooftops, and industrial trusses through our design-installation services. For more information, check our blog, learn about us, or get a free quote.
What are the key considerations in fall protection system installation reviews?
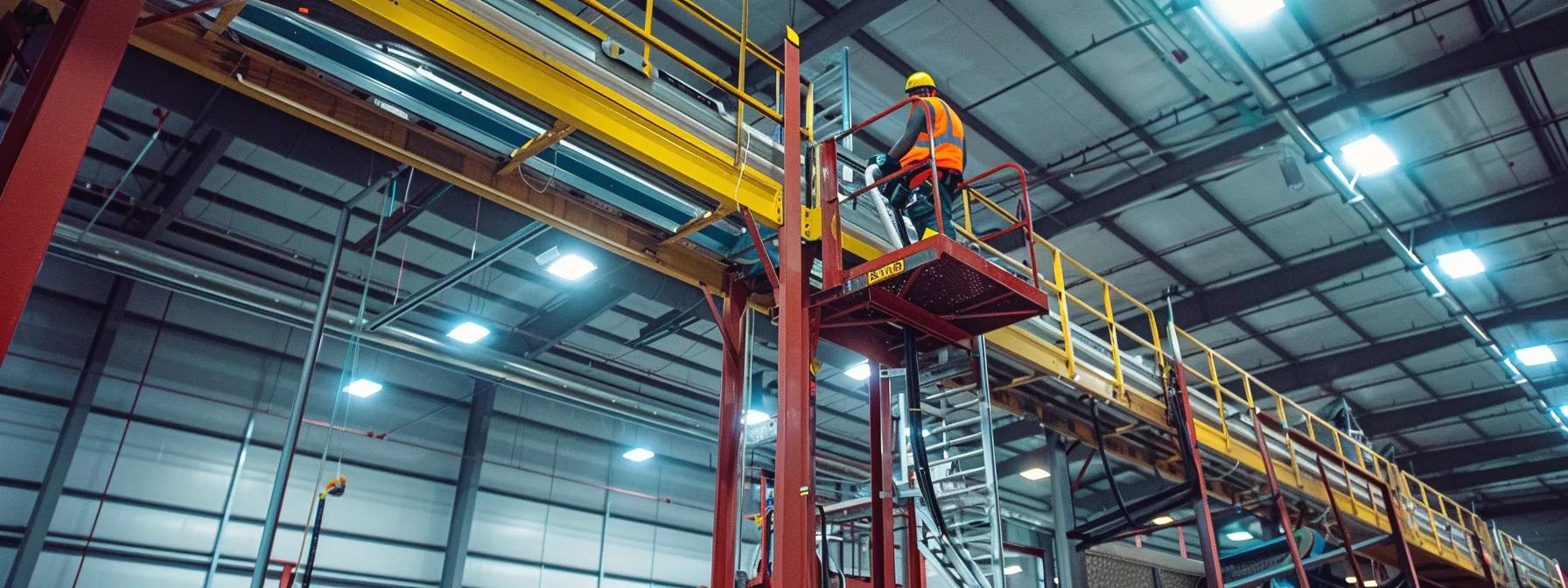
The key considerations in installation reviews include verifying correct anchor spacing (per ANSI Z359: 0.6 m to 2 m), checking beam load capacity against a 4:1 factor of safety, and confirming compatibility between harness buckles and lifelines from us fall protection. For more information, visit our about-us page. Reviewing design-installation plans also requires assessment of parapet and roof edge guardrails to meet a minimum 42 in height and withstand 200 lb of horizontal force per OSHA 1926.502(b). To get started, get a free quote or check out our blog.
Additionally, installers must ensure that all personal protective equipment components—lanyards, connectors, shock absorbers—are compatible and properly labeled with manufacturer specifications and expiration dates. For more information, visit our us fall protection page or get a free quote.
What techniques and tools are used for system inspection?
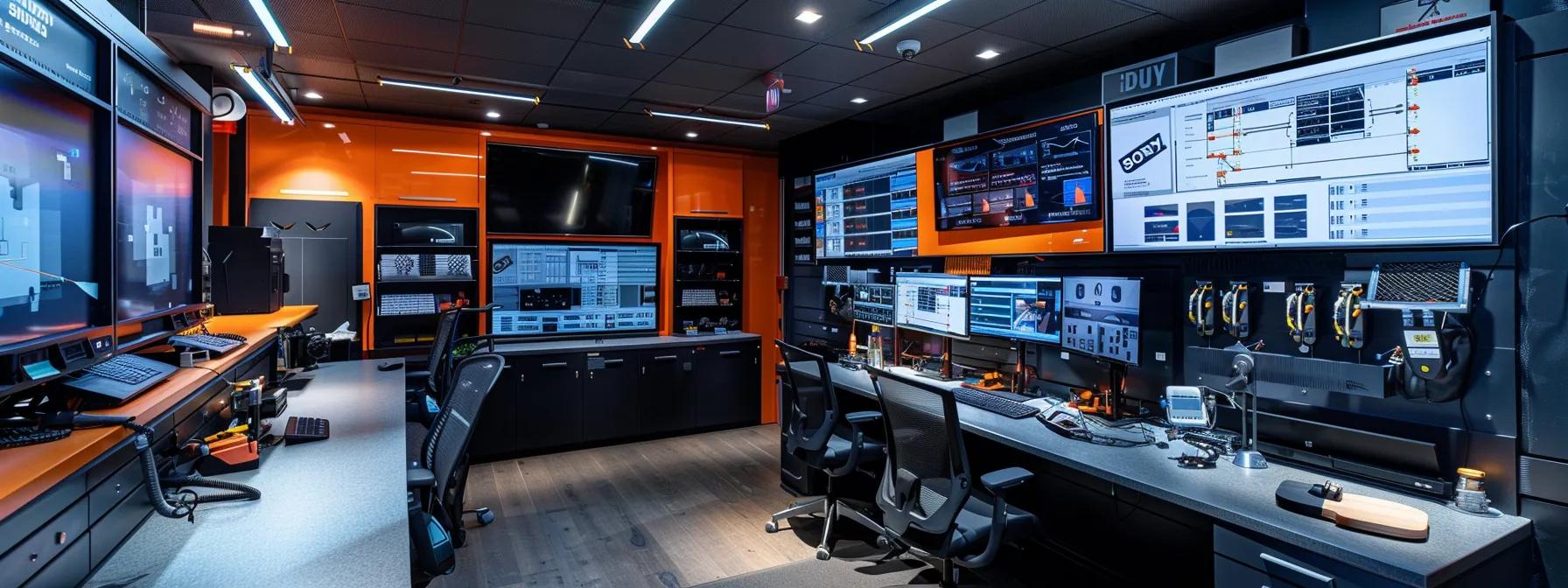
Techniques and tools for system inspection include visual inspection with a 10× magnification lens, tensile testing rigs for webbing strength, and digital torque wrenches to verify clamp tightness on wire rope systems. Inspectors also use borescopes to examine internal corrosion in davit bases and on‐site ultrasound thickness gauges for steel beam evaluation. For more insights, visit our blog or get a free quote to learn how we can assist you.
Advanced methods such as RFID tagging on harnesses allow real-time tracking of inspection dates, while mobile apps record photo-based evidence to support corrective actions and certification renewal. For more information, visit our blog or get a free quote.
What is the certification process linked to regular system inspections?
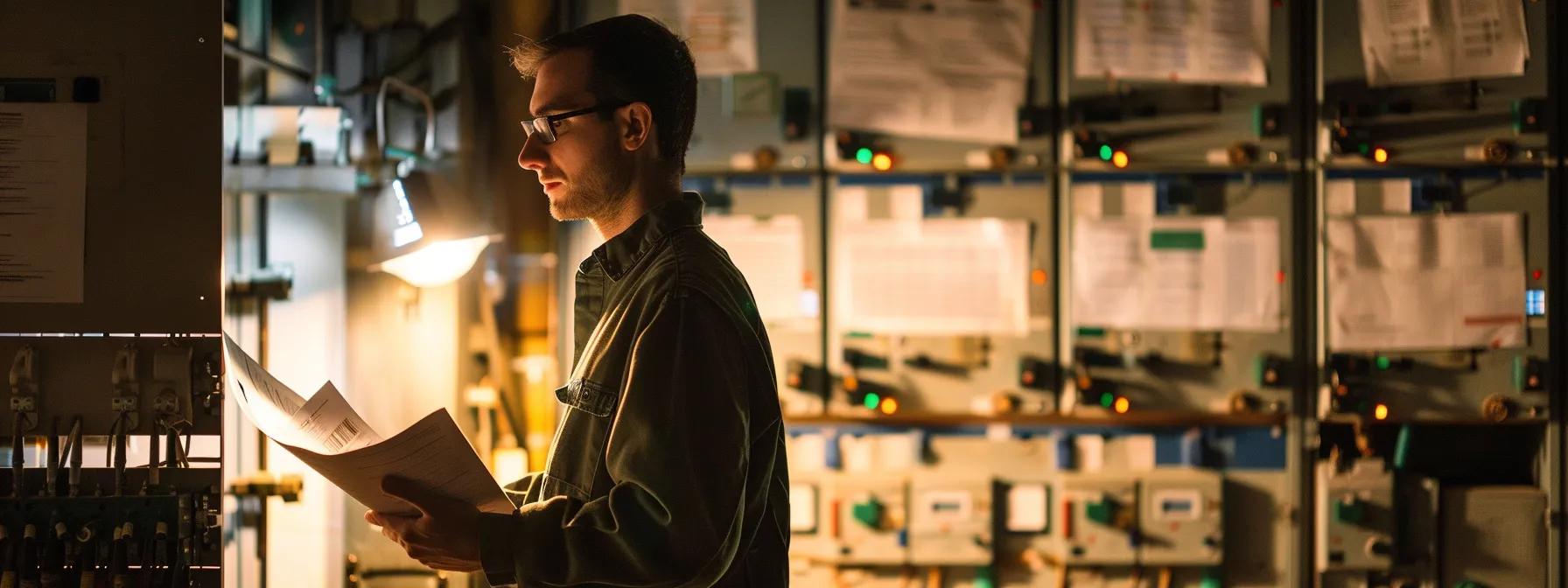
The certification process linked to regular system inspections requires documented proof of annual maintenance by a qualified engineer from our design-installation team, followed by third-party certification under ANSI Z359.2 for us fall protection. Once visual inspection and functional testing are completed, the engineer issues a certificate valid for one year, after which re-inspection is mandatory. For more information, visit our blog or get a free quote.
This annual certification aligns with OSHA’s recommended practice, ensuring that lifeline systems, horizontal and vertical lifelines, and personal fall arrest systems continue to meet design‐installation specifications and performance criteria. For more details, visit our about-us page or explore the industries-we-serve section.
What field examples illustrate the practical benefits of inspection?
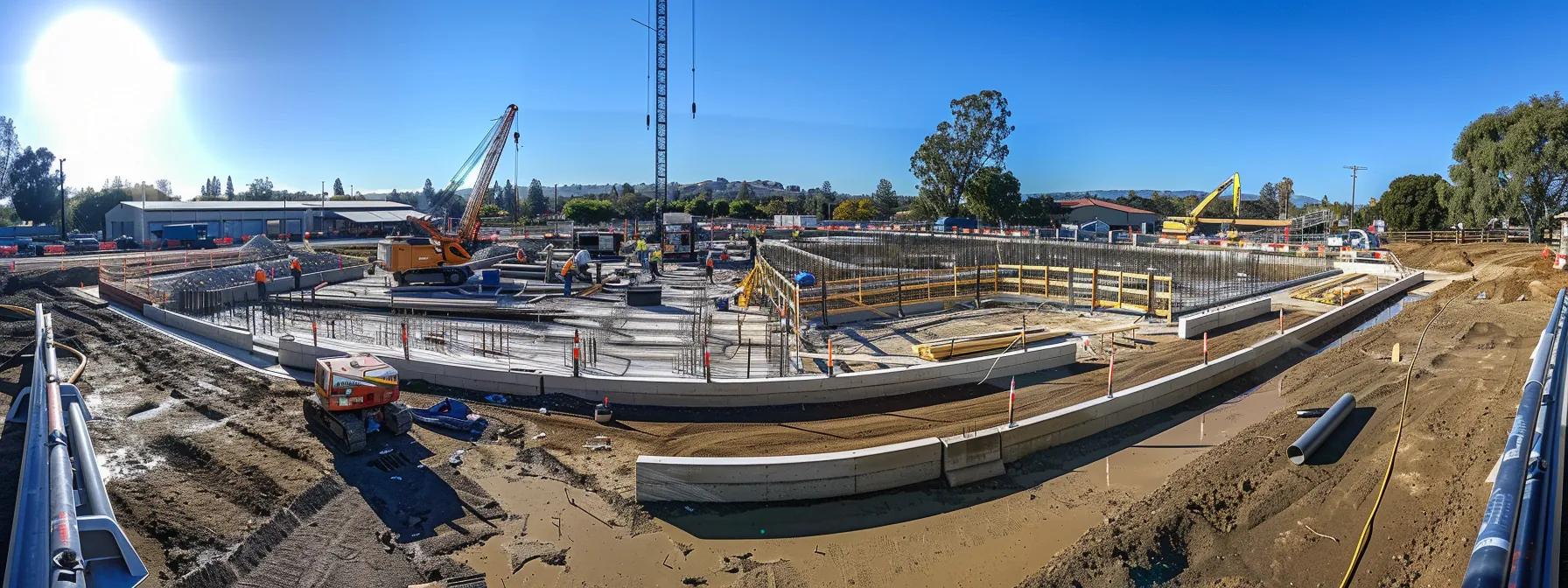
Field examples illustrate practical benefits of inspection: a warehouse in Texas reported a 50% drop in ladder‐system failures after implementing monthly visual inspections and annual certification, while a Canadian railcar maintenance facility reduced injury rates by 40% through quarterly anchorage testing and corrective maintenance.
In another case, a construction contractor in California avoided a $25,000 OSHA fine by presenting a complete inspection log for scaffold guardrails and mobile aerial lifts, demonstrating how proactive inspections can translate into cost savings and enhanced worker safety.
What are the main steps in a fall protection inspection program?
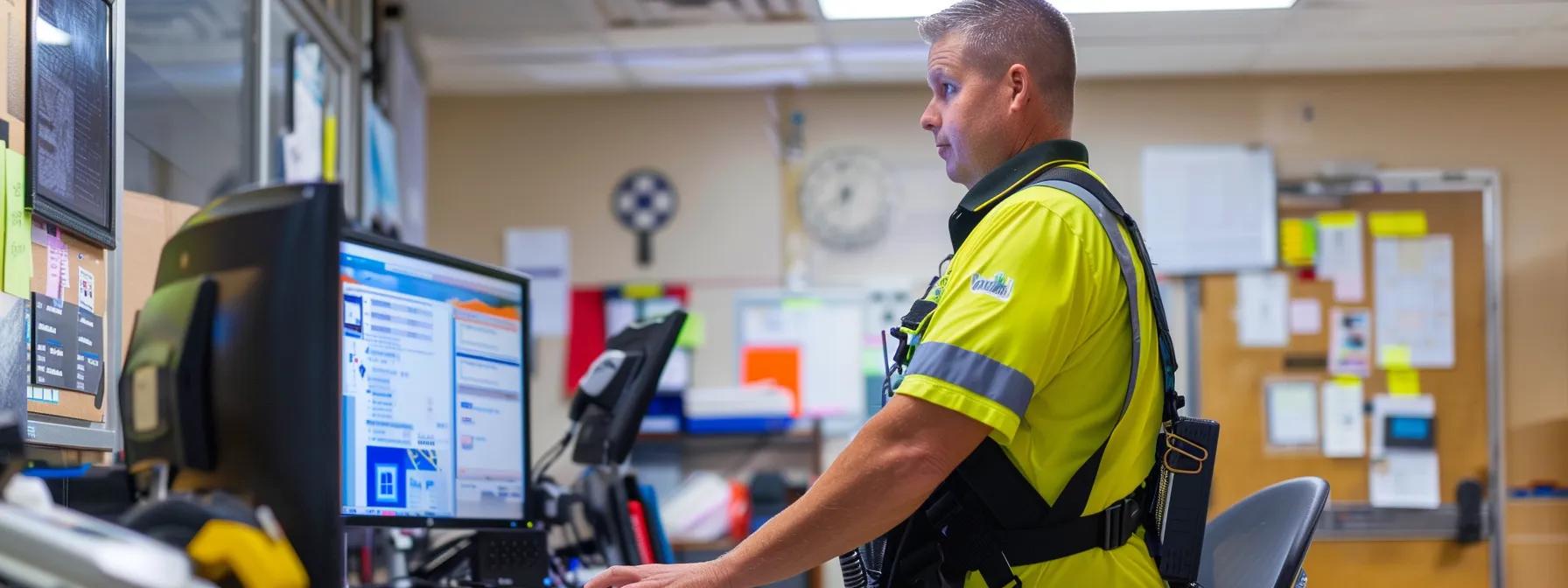
Organizations follow five main steps in a fall protection inspection program:
- Define inspection frequency based on system type (e.g., weekly, monthly, annual).
- Assign qualified inspectors and document training credentials.
- Perform visual and functional tests using calibrated tools.
- Log findings and corrective actions in a digital maintenance system.
- Obtain third-party certification and store certificates in compliance records.
By following these steps, companies align with both OSHA standards and ANSI Z359 guidelines while ensuring uninterrupted protection for workers at height.
How do inspection records support legal and insurance requirements?
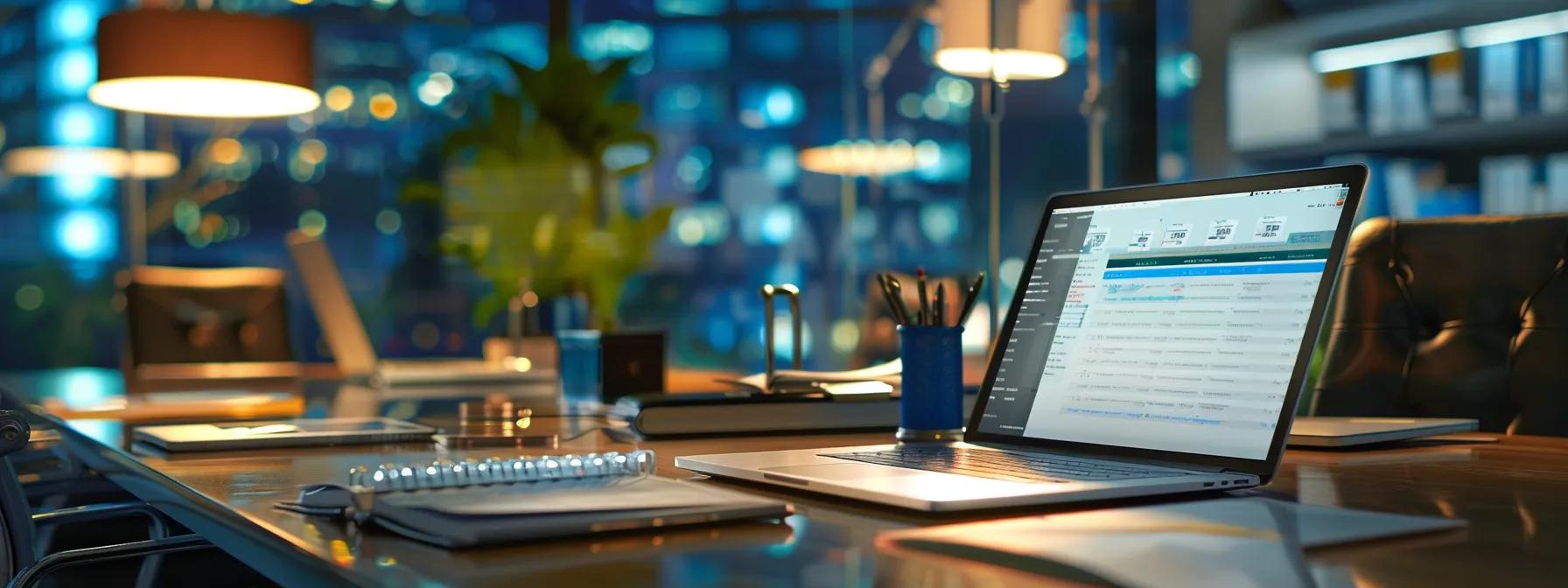
Inspection records support legal and insurance requirements by providing evidence of due diligence, which insurers often require to validate coverage for workplace injury claims. Detailed logs showing element-level inspections of personal protective equipment and system integrity tests enable legal teams to demonstrate compliance in the event of an accident.
Records tied to manufacturer factory specifications and ANSI certification certificates strengthen a company’s position in liability disputes and can reduce insurance premiums by up to 20%, according to a 2021 risk assessment report by the National Safety Council.
How do digital tools and analytics improve inspection effectiveness?
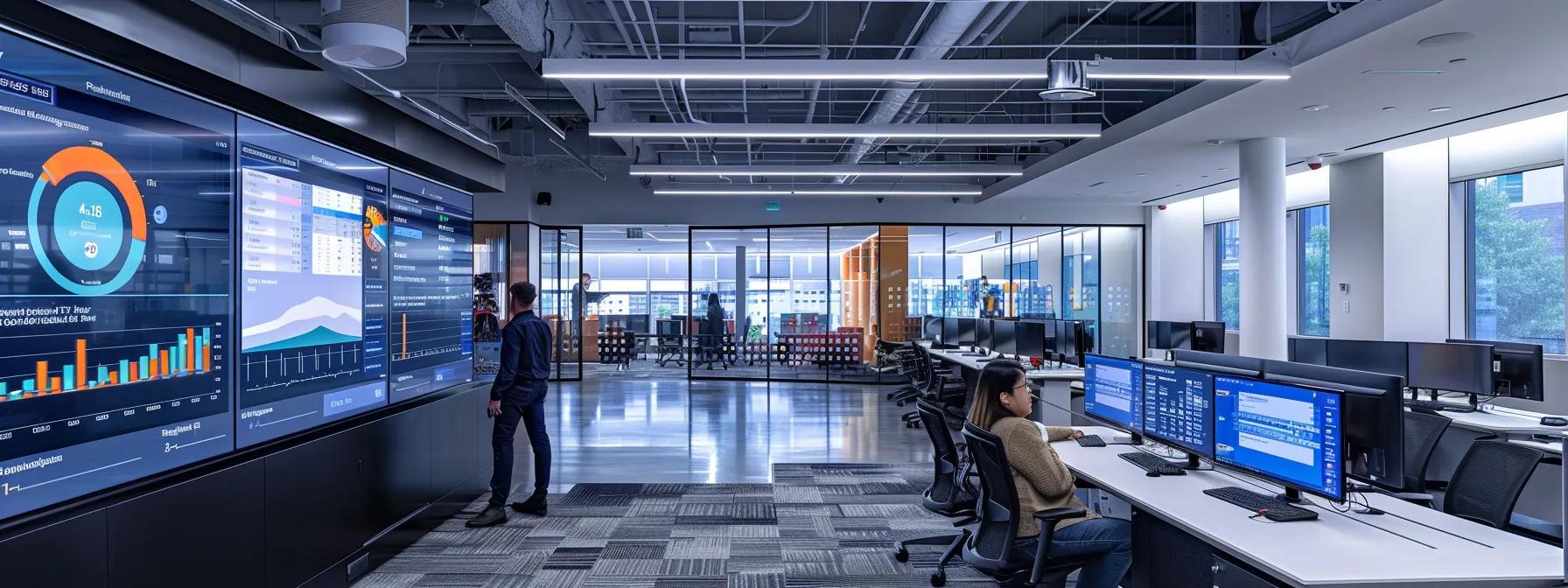
Digital tools and analytics improve inspection effectiveness by analyzing historical inspection data to predict component failure and optimize maintenance schedules. Analytics platforms highlight recurring issues—such as corrosion hotspots on steel rooftops or wear on lifeline connectors—allowing safety managers to prioritize high‐risk areas.
Automated dashboards also track key performance indicators like mean time between failures (MTBF) for fall arrest equipment, helping organizations move from reactive repairs to proactive risk management.
How can companies integrate inspection programs into broader safety initiatives?
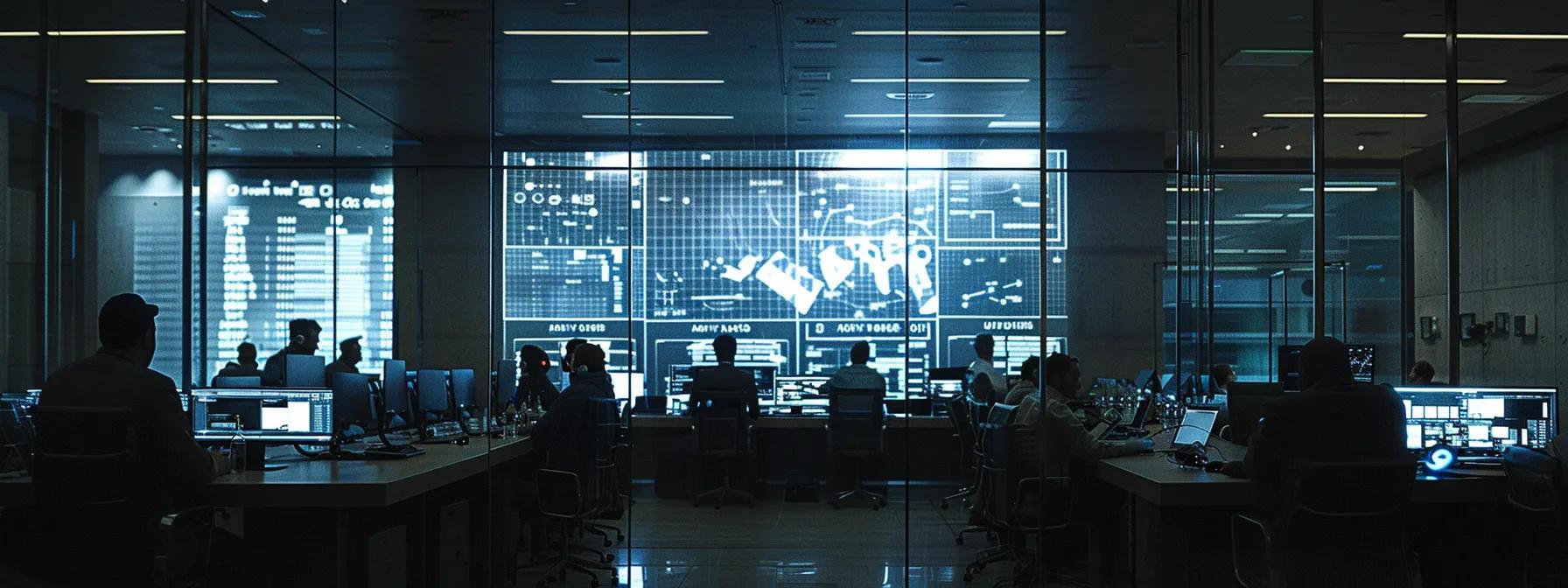
Companies integrate inspection programs into broader safety initiatives by linking fall protection audits with OSHA 10/30 training programs, HAZWOPER certification, and confined space entry protocols. By including inspection outcomes in monthly safety meetings, organizations reinforce a culture of continuous improvement.
Integration ensures that deficiencies uncovered during system inspections feed directly into corrective training—such as proper use of personal protective equipment—closing the loop between hazard identification and hazard control.
Table: Regulatory Comparison for Fall Protection Inspections
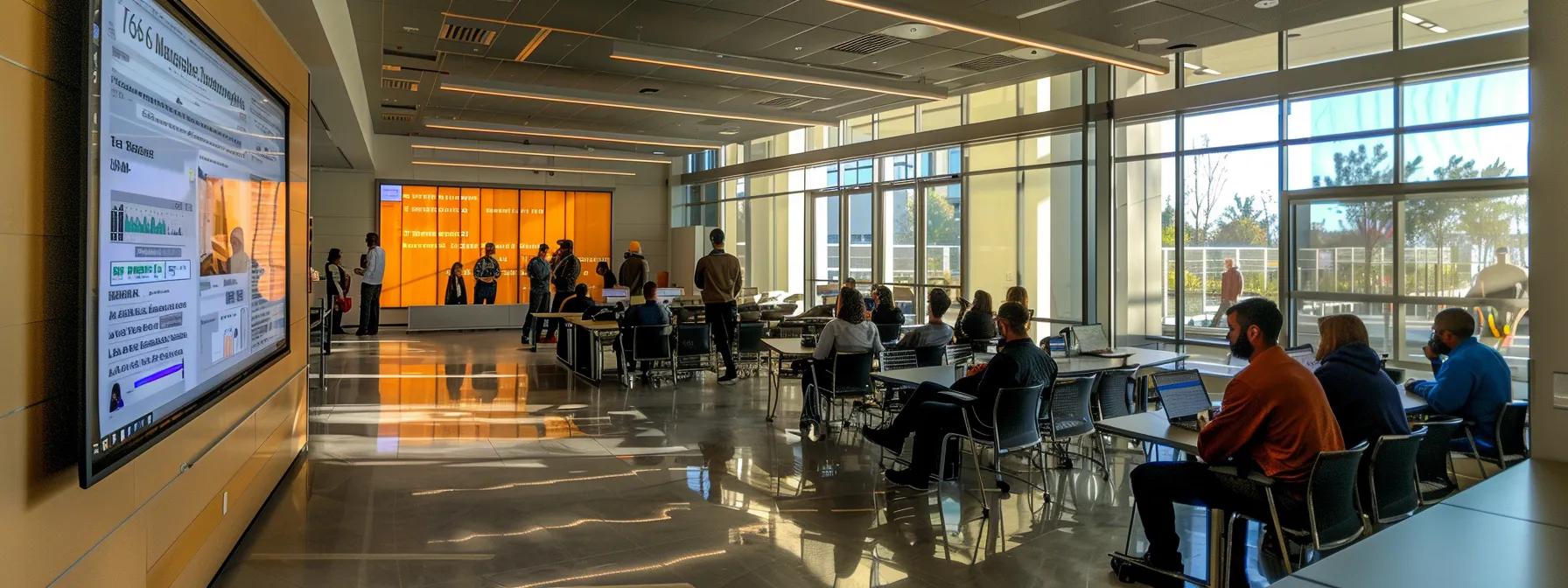
The table below compares key inspection requirements under OSHA and ANSI standards, illustrating frequency, documentation, and responsible parties.
Standard | Inspection Frequency | Documentation Required | Qualified Inspector |
---|---|---|---|
OSHA 1910.140 | Before each use (visual), annual (detailed) | Log of visual checks, annual certification | Competent person per §1910.140(c) |
ANSI Z359.2 | Monthly (visual), annual (functional) | Monthly checklist, test reports, engineer’s certificate | Qualified fall protection inspector |
CSA Z259 | Monthly (visual), annual (certified) | Inspection tag, digital record | Certified inspector per CSA guidelines |
This comparison highlights how harmonizing inspection schedules with multiple standards delivers comprehensive compliance and safety assurance.
How often should fall protection systems be inspected?
Fall protection systems require visual inspection before each use and detailed annual inspection by a qualified person.
Who qualifies to perform system inspections?
Inspectors must be competent persons trained per OSHA 1910.140(c) or certified under ANSI Z359.2 criteria.
What documentation is needed after an inspection?
Inspectors must record visual inspection logs, test reports, and obtain engineer-issued annual certificates.
How do inspection findings feed into corrective actions?
Findings populate digital dashboards, trigger work orders, and schedule retests to close hazard control loops.
Can digital tools replace hands-on inspections?
No; digital analytics enhance scheduling, but hands-on visual and functional tests remain mandatory for compliance.
Regular fall protection system inspections form the backbone of regulatory compliance and worker safety. By combining visual checks, functional tests, and annual certifications, organizations meet legal obligations and reduce accident risk. Digital inspection management enhances scheduling precision and data‐driven maintenance. Ultimately, rigorous inspections protect employees, lower costs, and support a proactive safety culture.