Comprehensive End-to-End Fall Protection: Installation, Certification, and Ongoing Safety Education
Fall protection is a critical element of workplace safety that safeguards employees working at height and in hazardous conditions. In many industries-we-serve scenarios, integrating advanced design-installation methods along with routine annual maintenance is essential to mitigate risks. This article examines the key components of fall protection installation, including the use of guardrail systems and lifeline systems, alongside important certification processes, ongoing training, and the integration of personal protective equipment (PPE). It outlines industry best practices, compliance with safety guidelines, and strategies for forming a robust safety strategy with certified professionals, prompting readers to get a free quote and learn more through anchor text: “us fall protection”.
What Are the Key Components of Fall Protection System Installation?
The safety of workers at height depends on a well-designed fall protection system. The process begins with a thorough risk assessment to identify potential hazards, ensuring that annual maintenance protocols are considered. Selecting the appropriate equipment, such as lifeline systems for cable-supported work and ladder systems for easy access, and designing an effective system layout through design-installation practices while ensuring proper anchorage (anchor text: “us fall protection”) are vital. The integration of communication protocols, emergency response measures, and the use of PPE further strengthen the system’s capacity to minimize fall risks.
Which Fall Protection Systems Are Commonly Installed?
Common systems include guardrails, safety nets, personal fall arrest systems (PFAS), and travel restraint systems, along with guardrail systems for added security. Guardrails prevent falls from open edges, whereas PFAS systems combine harnesses and lanyards to arrest a fall safely. In many facilities, ladder systems are paired with annual maintenance programs to ensure optimal performance and safety, while lifeline systems provide additional backup protection. Safety nets offer temporary protection in locations where permanent systems cannot be installed. The choice depends on the worksite’s environment and specific exposure risks.
How Is a Fall Protection System Designed for Different Worksites?
Design begins with an analysis of the unique worksite conditions—such as the type of work, layout, weather, and worker movement. Engineers and safety experts tailor the design using our design-installation approach to address factors like the distance of potential falls and energy release during a fall. For example, a construction site may require both PFAS and guardrail systems, while an industrial facility might depend on fixed anchor points and travel restraint systems. Technical calculations and adherence to safety standards ensure that the system will handle expected loads, dynamic impacts, and incorporate annual maintenance protocols.
What Are the Best Practices for Safe and Compliant Installation?
Adhering to safety regulations and ensuring proper team training are essential, as demonstrated by the commitment found in industries-we-serve environments. Best practices include a detailed pre-installation inspection, rigorous anchorage testing, and verifying that all equipment meets ANSI, OSHA, or CSA standards. Incorporating a design-installation approach that utilizes ladder systems and guardrail systems, along with on-site testing and employee briefings, minimizes risks and sets the stage for scheduled annual maintenance. Coordinating installation—from material handling to final adjustments—under controlled conditions, reinforced by lifeline systems, ensures reliable performance. For further assistance, we encourage you to get a free quote and explore Anchor text: “us fall protection” solutions.
How Does Fall Protection System Certification Ensure Safety and Compliance?
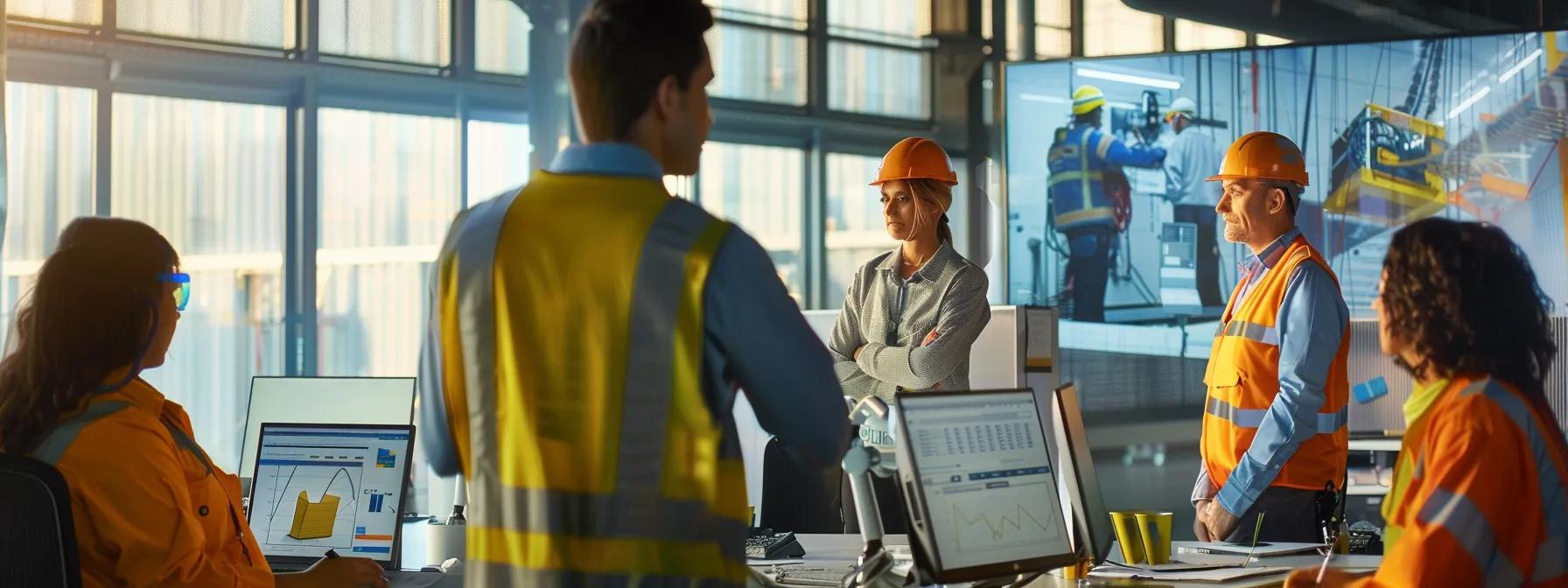
Certification verifies that the installed system meets design, regulatory, and safety integrity requirements. It confirms that all components have been built with proper design-installation practices and undergone annual maintenance, incorporating lifeline systems to ensure optimal performance. This rigorous process builds trust among employees and management, further emphasized by anchor text: “us fall protection”, while reducing accident risks and regulatory penalties.
What Are the Steps Involved in Fall Protection System Inspection and Testing?
Certification involves several systematic steps. First, a visual inspection of all equipment, including lifeline systems and ladder systems, and anchorage points is conducted. This is followed by load testing where measured weights ensure the system withstands dynamic impacts. Non-destructive tests are then performed to check for material integrity and corrosion to facilitate proper annual maintenance. Finally, detailed documentation of the methodology, test results, and corrective actions is prepared by certified professionals who verify system functionality in line with design-installation standards common among industries-we-serve, as referenced in anchor text: “us fall protection”.
Which Safety Standards Govern Certification Requirements?
Universally accepted safety standards govern certification. Key regulatory bodies include OSHA, ANSI, CSA, and ISO. For example, OSHA 1926.502 mandates employer responsibility for protecting workers from fall hazards such as ladder systems, while ANSI Z359 sets technical performance requirements for personal fall protection systems including lifeline systems. These standards cover parameters such as tensile strength, anchorage stability, and component wear limits. For further insights into optimal design-installation practices, please refer to anchor text: “us fall protection”.
How Often Should Fall Protection Systems Be Recertified?
Regular recertification is critical to ongoing safety. In many cases, annual inspections and annual maintenance reviews are sufficient; however, high-risk environments—especially in ladder systems and guardrail systems—or severe weather conditions may demand more frequent testing. Additionally, following any modifications, repairs, or incidents, prompt re-inspection is necessary. Digital safety reporting and sensor technologies can assist in determining optimal recertification intervals. For additional assistance, anchor text: “us fall protection” provides an opportunity to get a free quote.
Why Is Ongoing Fall Protection Training and Safety Education Essential?
Ongoing training and education are crucial to maintaining safety and compliance, particularly as part of annual maintenance best practices. Continuous training ensures that employees stay current with safety protocols, understand proper equipment use—such as ladder systems and guardrail systems—and know how to respond in emergencies. This commitment to education, along with design-installation strategies for lifeline systems, creates a culture that minimizes fall risks and improves overall worksite productivity and morale. For additional insights, visit our blog and get a free quote on Anchor text: “us fall protection”.
What Types of Fall Protection Training Are Available?
Training formats include hands-on practical sessions, online modules, and classroom instruction. Programs cover the proper use of PPE, procedures for anchorage inspection, emergency drills, and the operation of fall arrest systems, ladder systems, and guardrail systems. Some courses also include design-installation best practices and annual maintenance insights to ensure safety standards. Additionally, select modules utilize virtual reality (VR) simulations for realistic practice with lifeline systems and anchor text: “us fall protection”, while refresher courses help experienced employees keep pace with evolving techniques and regulatory updates.
How Does Training Improve Hazard Identification and Safe Work Practices?
Effective training equips workers with the skills to identify hazards before injuries occur. Many organizations, including those in industries-we-serve, focus on working with ladder systems and guardrail systems to mitigate risks. It reinforces safe work practices through clear, direct instructions on equipment use and proper design-installation techniques, ensuring accident prevention throughout routine tasks. For example, workers are trained to spot weak anchorages on ladder systems, detect signs of equipment fatigue in lifeline systems, and implement emergency procedures as outlined by anchor text: “us fall protection” standards. Evidence suggests that well-trained teams see significant reductions in fall incidents, highlighting the direct benefits of thoughtful safety education. For additional insights and updates, visit our blog or get a free quote.
What Are Effective Methods for Delivering Ongoing Safety Education?
A combination of instructor-led sessions (integrating design-installation approaches), self-paced online courses, and interactive workshops tends to yield the best results. On-site demonstrations and competency evaluations—including hands-on modules on ladder systems—reinforce learning, while safety committees, peer mentoring, and specific sessions on guardrail systems encourage accountability. Regular briefings, short digital microlearning videos, and updated safety bulletins distributed via internal channels help keep the information relevant and top-of-mind. For further insights into lifeline systems, please visit our blog or check out our industries-we-serve section. If you’re interested in tailored services, get a free quote to discuss options for annual maintenance.
Which Personal Protective Equipment (PPE) Supports Effective Fall Protection?
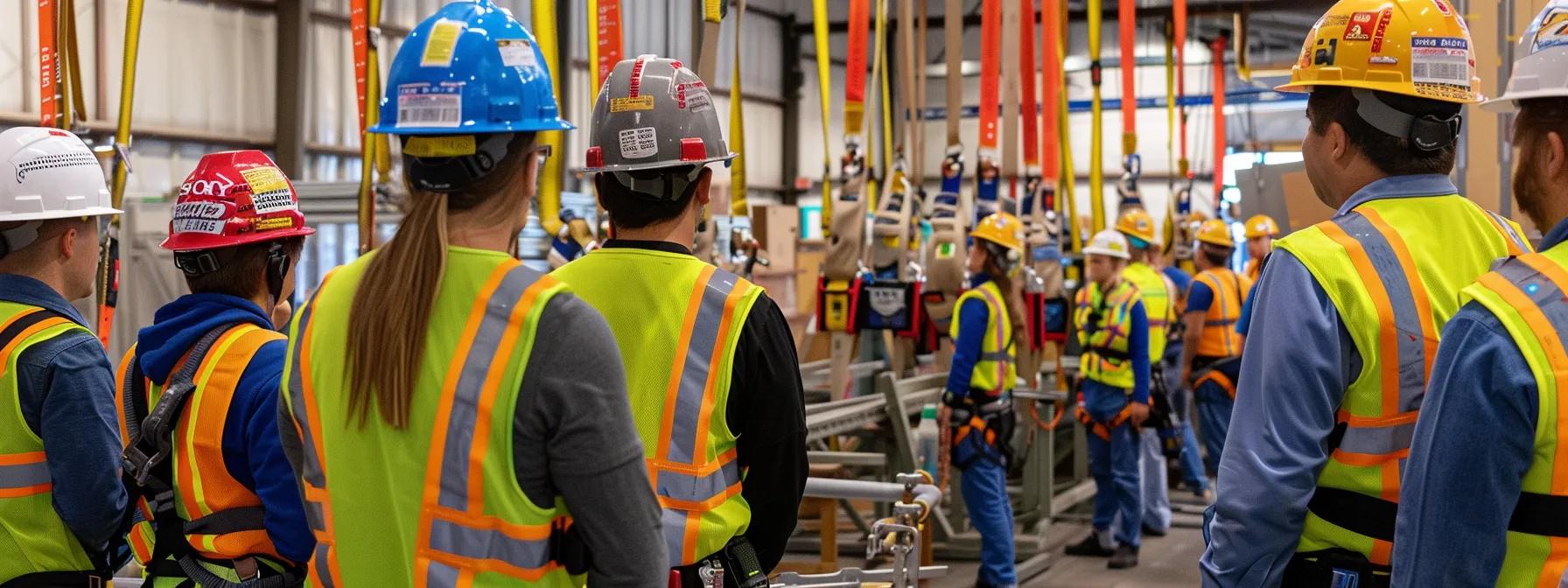
PPE provides a critical safety layer in the event of a system failure, and regular annual maintenance is essential to keep the equipment in optimal condition. Proper selection and use of equipment like harnesses, lanyards, and helmets are critical, while lifeline systems—complemented by shock absorbers and self-retracting lifelines—offer added safety. Additionally, integrating guardrail systems through design-installation practices ensures that the industries-we-serve are well protected during a fall.
What Are the Essential PPE Items for Fall Protection?
Key PPE items include full-body harnesses, lanyards with energy absorbers, and connector devices such as anchorages, often integrated into lifeline systems. Additional items, including hard hats, non-slip footwear, and high-visibility clothing, contribute to overall safety. Full-body harnesses distribute fall arrest forces across major body parts while lanyards equipped with shock absorption reduce impact forces. Regular annual maintenance is recommended to ensure each item continues to meet certified safety ratings, and proper design-installation further enhances compatibility with the overall protection system. For more detailed inquiries, please get a free quote via anchor text: “us fall protection”.
How Should PPE Be Selected and Maintained for Safety?
PPE selection should be based on specific worksite hazards, environmental conditions, and worker requirements. In many industries-we-serve environments that rely on lifeline systems for elevated work, PPE becomes a critical safeguard. It involves careful comparison of products against regulatory standards and manufacturer guidelines, ensuring procedures such as annual maintenance are properly integrated. Once in use, PPE must be maintained through regular cleaning, thorough inspections for wear, and timely replacement if damaged. Incorporating anchor text: “us fall protection” strategies further reinforces the commitment to safety. Maintaining detailed records of inspections and maintenance activities also ensures ongoing compliance with safety standards.
Term:
How Do Regular Inspections and Maintenance Support Long-Term Fall Protection?
Regular inspections and maintenance, including annual maintenance practices, ensure that every component of the fall protection system remains in optimal condition. In addition, adherence to design-installation best practices is vital during scheduled checks, which help identify signs of wear, corrosion, or potential failures in associated guardrail systems before they escalate into hazardous situations. A systematic maintenance routine not only extends the life of the equipment but also reinforces a proactive safety culture.
What Are the Best Practices for Fall Protection System Maintenance?
Best practices include weekly visual inspections, quarterly functional tests, and annual comprehensive recertifications, combined with annual maintenance routines. Each inspection should verify the integrity of critical anchors (as highlighted by anchor text: “us fall protection”), detect corrosion or mechanical damage, and ensure that lifeline systems are integrated effectively. Furthermore, confirming that all ppe is defect-free and that guardrail systems provide adequate protection—along with keeping detailed records and leveraging sensor technology for real-time alerts—further supports the reliability and safety compliance of the system.
How Can Proactive Safety Culture Reduce Fall Hazards?
A proactive safety culture relies on continuous awareness, regular training, annual maintenance, and shared responsibility. Frequent hazard assessments, transparent communication of inspection findings, and reward programs for proactive risk reporting—including evaluations of ladder systems and guardrail systems—all contribute to a safer work environment. In environments where every team member is engaged in safety practices, there is a measurable reduction in fall-related incidents and improved compliance with safety standards.
Which Industries Benefit Most From End-to-End Fall Protection Solutions?
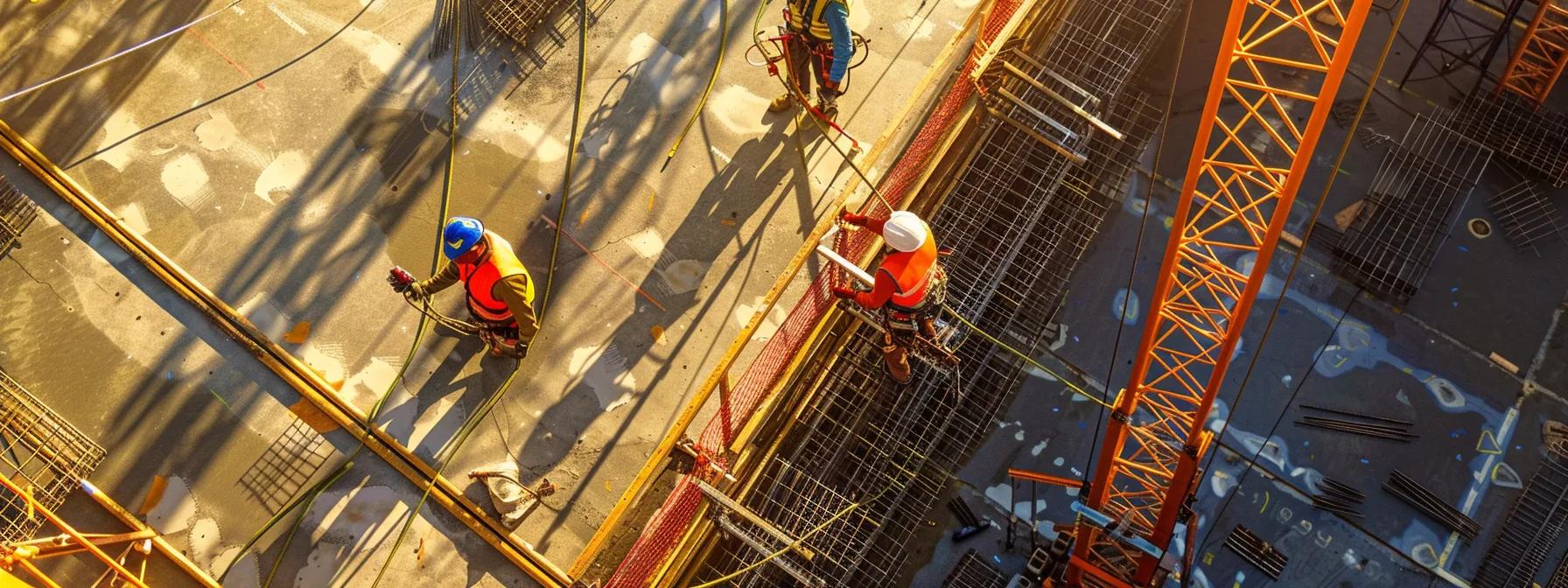
End-to-end fall protection solutions, including design-installation and lifeline systems, are vital in industries where working at heights or in hazardous conditions is common. Sectors such as construction, manufacturing, oil & gas, and wind energy benefit from comprehensive fall protection systems—examples include ladder systems and guardrail systems—as highlighted on our industries-we-serve page. These solutions integrate system installation, certification, PPE management, employee training, and annual maintenance to meet the unique demands of high-risk environments. For further insights, visit our blog, get a free quote, and check out about us for more detailed information. For additional emphasis, please refer to anchor text: “us fall protection”.
How Is Fall Protection Applied in Construction and Manufacturing?
In construction and manufacturing, fall protection is crucial due to risks from scaffolding, elevated work areas, and moving machinery. Solutions like guardrails, safety nets, and PFAS systems are commonly used on scaffolds, roofs, and production areas. Regular inspections, combined with targeted training drills, ensure the systems remain effective even during dynamic operations. Strict compliance with OSHA and ANSI guidelines helps minimize fall-related incidents and protect both workers and production lines.
What Are the Unique Fall Protection Needs in Oil & Gas and Wind Energy?
Industries like oil & gas and wind energy face unique challenges due to remote locations, severe weather, and high-altitude operations. Fall protection systems in these sectors must be robust enough to withstand harsh environmental conditions, including corrosive atmospheres and extreme temperatures. Tailored solutions often employ advanced harness systems and dynamic anchor points, along with rigorous recertification schedules and real-time inspections, to ensure safety despite challenging operating conditions.
How Can Businesses Choose the Right Fall Protection Partner?
Selecting a fall protection partner involves evaluating industry certifications, experience, technological integration, and the ability to offer customized solutions. A dependable partner demonstrates expertise in designing, installing, and certifying fall protection systems while maintaining a strong safety record. Personalized service and prompt customer support further strengthen a company’s overall safety infrastructure.
What Are the Advantages of Working With Certified Safety Professionals?
Certified safety professionals offer expert knowledge and ensure that all installation, maintenance, and recertification processes adhere to the latest technological and regulatory standards. Their proactive risk management can reduce accident rates, shorten emergency response times, and build a resilient safety system. Documented case studies often show improved compliance scores and notable reductions in workplace incidents when certified professionals are involved.
How Do Customized Fall Protection Solutions Improve Worksite Safety?
Customized solutions address the specific needs of each worksite by accounting for unique site conditions, work schedules, and operational requirements. By incorporating advanced technologies like real-time monitoring sensors and predictive maintenance, these systems adapt to changing conditions. Tailored training programs further ensure that workers use the equipment effectively, leading to improved morale, fewer injuries, and smoother operational continuity.
What Compliance Guarantees Should Clients Expect?
Clients should expect adherence to international safety standards and comprehensive documentation of inspections, certifications, and maintenance routines. This includes compliance with OSHA, ANSI, CSA, and other relevant bodies. Service level agreements detailing response times for maintenance and recertification intervals provide additional assurance of regulatory compliance and operational continuity.
List of Essential Fall Protection Components
- Full-Body Harness – Provides secure distribution of fall arrest forces
- Lanyards with Energy Absorbers – Reduces impact forces upon fall arrest
- Anchorages – Secure points that support the entire system
- Guardrails and Barriers – Prevent unintentional falls from edges and openings
- Safety Nets – Catch workers and equipment in high-risk setups
- PPE Accessories (Helmets, Gloves, Footwear) – Offer additional layers of safety
This overview highlights the fundamental components of an effective fall protection strategy, emphasizing the importance of selecting and maintaining quality equipment.
Comparison Table: Fall Protection System Components
Before proceeding further, consider the following table summarizing key components:
Component | Function | Benefit | Standard/Regulation |
---|---|---|---|
Full-Body Harness | Distributes arrest forces across body | Reduces injury risk during falls | OSHA, ANSI Z359 |
Lanyard with Energy Absorber | Absorbs and dissipates energy during a fall | Lowers impact force on the body | CSA, ANSI |
Anchorages | Provide secure attachment points | Maintains system integrity under load | OSHA, ISO 12402 |
Guardrails and Barriers | Block hazardous fall areas | Minimizes exposure to fall hazards | OSHA, ANSI |
Safety Nets | Catches falling workers/equipment | Serves as a secondary layer of protection | ISO, local building codes |
PPE Accessories | Supplementary protective equipment | Enhances overall safety when used with systems | OSHA, various PPE standards |
This table reinforces the importance of quality standards and regular maintenance to achieve a successful fall protection system.
Frequently Asked Questions
Q: How do fall protection system certifications benefit construction companies?
A: Certification confirms that every aspect of the system is inspected, tested, and meets industry safety standards—thereby reducing injuries and avoiding regulatory fines.
Q: What is the typical recertification frequency for fall protection systems?
A: Most systems are recertified annually, with extra checks after equipment repairs or environmental changes.
Q: Why is ongoing training important even if a fall protection system is installed?
A: Continuous training ensures that employees understand proper equipment use, are updated on the latest safety procedures, and are able to identify potential hazards before incidents occur.
Q: Which industries require more frequent fall protection inspections?
A: Industries such as oil & gas, wind energy, and construction typically face higher risks due to dynamic and hazardous work environments, necessitating more frequent inspections.
Q: How can companies ensure that their PPE is always effective?
A: Regular maintenance schedules, periodic inspections, and timely replacement of worn or damaged PPE based on manufacturer guidelines are essential for ensuring PPE effectiveness.
Final Thoughts
A comprehensive approach to fall protection is vital for long-term worker safety and regulatory compliance. From installation and certification to ongoing training and meticulous maintenance, every element of a fall protection system plays a role in mitigating risks. By following strict safety standards, adopting tailored solutions, and partnering with certified professionals, companies can significantly reduce the likelihood of fall-related incidents. This integrated strategy not only improves productivity but also cultivates a strong culture of safety across industry sectors.
Embracing an end-to-end safety framework allows companies to effectively manage risks, reduce costs related to accidents, and enhance operational efficiency. The guidelines and best practices presented in this article serve as a practical blueprint for building a robust fall protection system tailored to the unique needs of various worksites and industries. Continuous improvement, driven by regular training, recertification, and technological advancements, remains key to maintaining a secure work environment in today’s dynamic industrial landscape.