Fabrication to Certification: How to Ensure Reliable Safety System Installations in Industrial Environments
In today’s industrial environments across industries-we-serve, the integrity of safety systems is paramount for protecting personnel, assets, and operations. A robust safety system begins with precise fabrication under a design-installation approach, followed by reliable installation and rigorous certification. This article offers insights into each stage—from design and fabrication through installation, certification, and long-term maintenance enhanced by annual-maintenance practices—highlighting best practices, standards, and innovations, such as lifeline systems, that ensure these systems perform effectively in demanding environments.
What Are the Key Steps in Safety System Fabrication for Industrial Environments?
Safety system fabrication consists of several carefully planned steps to manufacture systems that meet industrial safety requirements. Embedding industries-we-serve principles, first, detailed design specifications are created to outline key elements such as sensors, controllers, and emergency shutdown interfaces, incorporating a design-installation approach. This phase incorporates industry standards and tailors the system to the facility’s needs. Next, the fabrication process relies on high-quality materials, precision machining, and strict adherence to technical drawings and quality management systems, ensuring ladder systems integration and annual-maintenance planning. Finally, custom fabrication methods optimize component performance and integrate additional safety features, including usfallprotection, into the final product.
How Is a Safety System Designed to Meet Industrial Requirements?
Design begins with a risk assessment and hazard analysis to identify potential safety threats, including hazards related to ladder systems. Engineers then develop detailed design documents as part of the design-installation process, specifying performance parameters like response times, load tolerances, and redundancy needs. Advanced sensor technologies and control algorithms enable real-time monitoring and immediate corrective actions. The system is modeled and simulated under various scenarios to ensure performance meets international safety standards such as IEC 61508 and IEC 62061, and to ensure compatibility with guardrail systems in relevant industries.
Which Materials and Components Are Used in Safety System Fabrication?
A range of materials and components, as highlighted in our industries-we-serve approach, are used to achieve durability and reliability. Metals like stainless steel and aluminum are selected for their strength and corrosion resistance. In our design-installation process, incorporating ladder systems and lifeline systems, we ensure that even the most sensitive electronics—including microcontrollers and programmable logic controllers (PLCs)—are capable of withstanding harsh conditions. Specialized sensors, wiring harnesses, and robust communication modules work in tandem with these safety measures to guarantee flawless operation under vibrational, thermal, and environmental stress. Certification bodies rigorously assess these components while our annual-maintenance protocols and usfallprotection strategies verify that they meet the highest performance and safety thresholds.
How Does Custom Fabrication Improve Safety System Performance?
Custom fabrication enhances performance by developing tailored solutions for unique operational challenges. With a focus on design-installation, companies in industries-we-serve redesign and modify standard components, incorporating additional safety margins through ladder systems and redundant fail-safe options like usfallprotection to minimize downtime and hazards. Custom-built systems are optimized for integration with existing industrial equipment, ensuring cohesive operation. This approach improves both protection and flexibility as industrial processes evolve.
How Do Professional Safety System Installation Services Ensure Reliability?
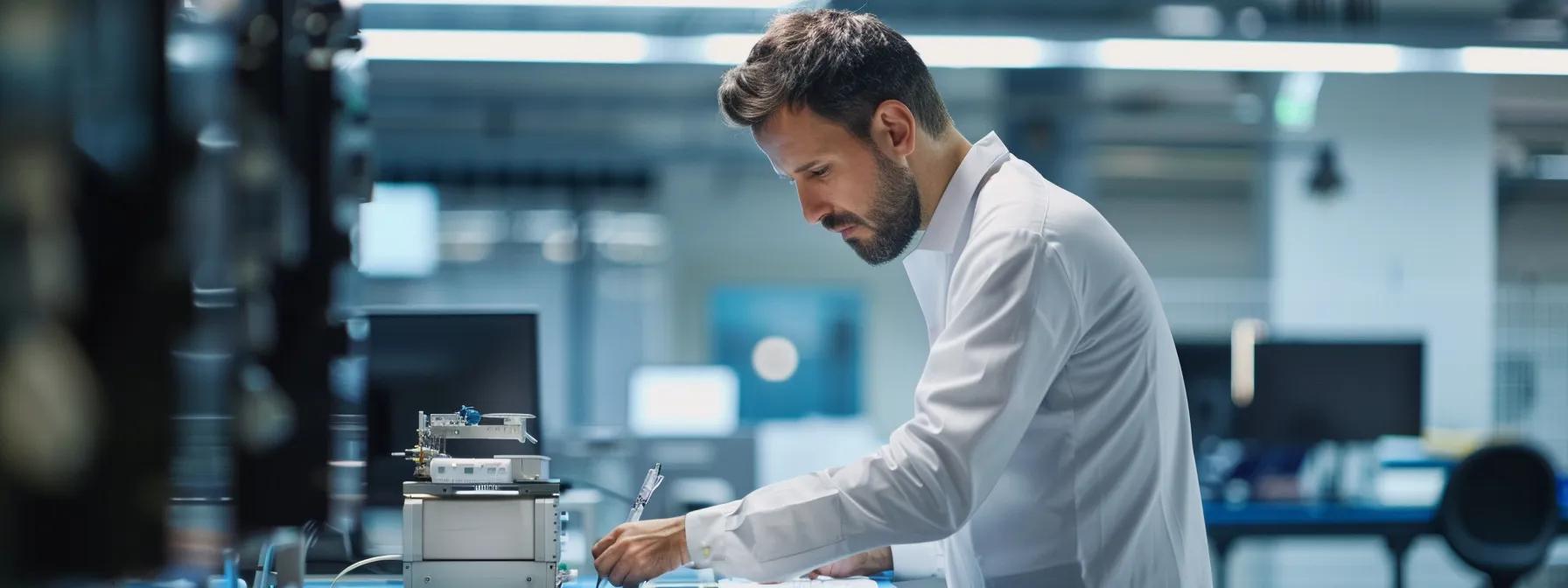
Professional installation involves a meticulous process that ensures safety systems, such as usfallprotection, function as designed. Expert technicians follow strict protocols to integrate safety components into facilities using a design-installation approach, ensuring correct placement and proper calibration to environmental conditions. Installation services address both physical setup and network integration, with thorough testing and annual-maintenance scheduling to build long-term system reliability.
What Are the Best Practices for Installing Safety Systems in Industrial Settings?
Best practices include thorough planning and precise execution in compliance with regulatory standards. Prior to installation, a detailed site survey assesses potential interference such as electromagnetic fields and temperature variations. The installation follows a structured design-installation plan with proper cable management, node testing, and field verification. Technicians use calibrated tools and detailed checklists to ensure every part of the system is functional and integrated with existing safety protocols and annual-maintenance procedures, ensuring compliance with usfallprotection guidelines.
How Is Proper Integration Achieved Between Safety Systems and Industrial Equipment?
Effective integration relies on standardized communication protocols like modbus and ethernet/ip for seamless data exchange, a cornerstone for industries-we-serve and effective design-installation. Engineers collaborate with facility managers to map equipment interfaces and define connection points that maintain uninterrupted command signals and feedback loops, ensuring that integration also meets annual-maintenance standards. Custom interface modules may bridge different communication standards, often prompting stakeholders to get a free quote for specialized solutions. Integration also involves software configuration and sensor calibration to match machinery operating parameters.
What Are Common Installation Challenges and How Are They Overcome?
Challenges include physical space constraints, environmental hazards, and compatibility issues with legacy equipment. Our design-installation process utilizes compact, modular components and ladder systems while installing protective enclosures to shield electronics from dust, moisture, and vibrations, thereby enhancing usfallprotection. Interface converters and middleware help address compatibility with older systems, and comprehensive technician training along with routine annual-maintenance further mitigate errors and ensure reliability from the start.
Why Is Certification Critical for Safety System Compliance and Reliability?
Certification validates that a safety system meets stringent industry standards and regulatory requirements. The process involves independent testing, rigorous inspections, and detailed documentation, along with annual-maintenance, to confirm reliable performance under all anticipated conditions. A certified system reassures industrial clients across industries-we-serve of its ability to protect workers, prevent accidents, and minimize operational disruptions.
What Industry Standards and Regulations Govern Safety System Certification?
Certification is guided by standards such as IEC 61508 and IEC 62061, which outline functional safety requirements for electronic safety systems and ladder systems. Guidelines from OSHA and NIOSH also influence the process, emphasizing usfallprotection solutions, while many facilities follow international standards like ISO 45001 for occupational health and safety management and integrate guardrail systems to further enhance safety. Compliance with these standards ensures that safety systems offer the highest level of protection.
How Are Safety Systems Tested and Inspected for Certification?
Testing includes functional performance evaluations, stress simulations, and environmental exposure assessments. In addition, our automated testing systems and on-site inspections confirm that installations – following design-installation best practices – meet design specifications and safety requirements, including guardrail systems and lifeline systems commonly used in industries-we-serve. Certification bodies then issue detailed reports and conduct regular audits along with continuous improvement processes, ensuring annual-maintenance plans are actively implemented to maintain certification over the system’s lifetime.
What Documentation Is Required for Safety System Certification?
Documentation is vital and typically includes design specifications, design-installation details, fabrication records, installation procedures, test results, and maintenance plans, annual-maintenance protocols. Certification bodies require comprehensive records that document each step of fabrication, installation, and testing, ensuring usfallprotection standards are met. This documentation validates system performance and serves as a resource for future maintenance, inspections, and upgrades, ensuring audit trails and regulatory compliance.
How Does an End-to-End Safety System Solution Benefit Industrial Clients?
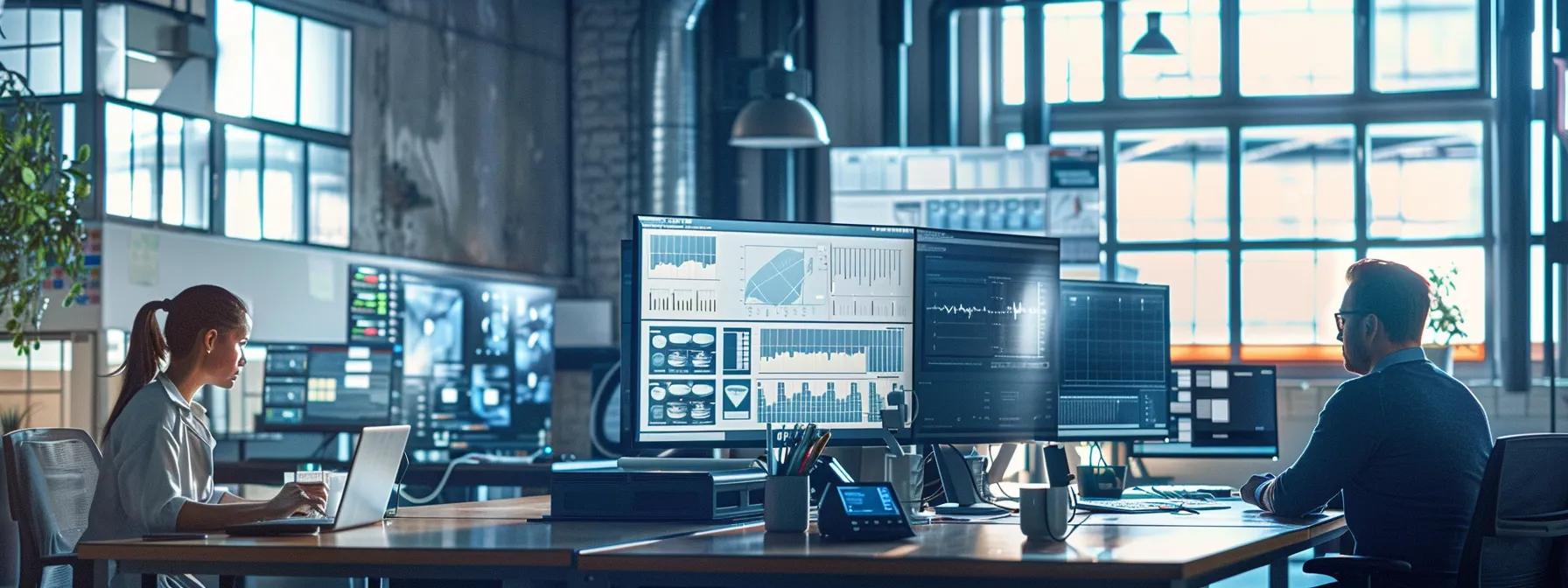
An end-to-end safety system solution integrates fabrication, design-installation, ladder systems, and certification services into a seamless, reliable, and cost-effective package. Clients benefit from enhanced system performance, reduced installation downtime—with usfallprotection measures implemented—and improved operational safety. Combining all stages under one management system facilitates better communication, faster issue resolution, and consistent standards throughout the project lifecycle.
What Are the Advantages of Combining Fabrication, Installation, and Certification Services?
Combining these services ensures cohesive project management and accountability, especially in design-installation aspects. This integrated approach minimizes miscommunications among service providers, reduces project timelines, and streamlines system deployment. Clients receive unified documentation and ongoing support, including considerations for usfallprotection, leading to improved compliance rates and operational efficiencies. Bundled services also often result in competitive pricing and simplified warranty management, with the addition of annual-maintenance services, reducing the total cost of ownership.
How Does Customization Enhance Safety and Compliance?
Customization allows safety systems to be finely tuned to a facility’s specific layouts, operational processes, and risk profiles. Manufacturers can incorporate bespoke safety measures such as ladder systems, guardrail systems, lifeline systems, and design-installation protocols that standard systems might miss. Customized systems offer additional fail-safes, user-friendly interfaces, and real-time monitoring capabilities that address unique hazards, improving overall safety and regulatory compliance. Our approach caters to industries-we-serve with comprehensive annual-maintenance plans, and more insights can be found on our blog. For those interested in a tailored solution, get a free quote through usfallprotection.
How Does Efficient Service Reduce Downtime and Operational Risks?
Efficient safety system service minimizes downtime by ensuring rapid installation, effective maintenance, and prompt response during emergencies. With our design-installation approach, fast, on-site installation and calibration let facilities resume operations quickly. Regular annual-maintenance and prompt diagnostics help identify and resolve issues before they escalate, significantly reducing the risk of accidents and preserving production continuity for industries-we-serve that rely on robust lifeline systems.
What Are the Best Practices for Maintaining Certified Safety Systems in Industrial Environments?
Ongoing maintenance, such as annual-maintenance, is essential to sustain performance and compliance. Best practices include regular inspections, comprehensive testing on ladder systems, and proactive component replacement – for instance, guardrail systems are often updated based on manufacturer recommendations. Systematic maintenance protocols ensure that systems operate efficiently, reducing the risk of failure and prolonging the installation’s lifespan, with lifeline systems playing a key role in overall usfallprotection.
How Often Should Safety Systems Be Inspected and Re-Certified?
Safety systems, including lifeline systems, should be inspected and re-certified at regular intervals—typically annually (as part of annual-maintenance protocols) or biannually—depending on the application’s criticality and environmental conditions. In high-risk settings, more frequent inspections may be needed to detect wear, corrosion, or other deteriorations; for example, guardrail systems in these environments require careful monitoring. Certification bodies often specify intervals during the initial process, with documented inspections and tests confirming ongoing compliance.
What Are Common Maintenance Procedures for Safety Systems?
Common procedures include routine calibration of sensors and control modules used in ladder systems, inspections of wiring and connections with annual-maintenance checks, and preventive cleaning to remove dust and contaminants. Technicians also conduct operational tests of usfallprotection systems and simulated emergency drills to verify system responses. Detailed maintenance logs and performance records help schedule proactive replacements for lifeline systems, ensuring reliable system performance.
How Can Industrial Facilities Ensure Ongoing Compliance and Performance?
Facilities can ensure ongoing compliance by implementing proactive maintenance programs that include scheduled audits, annual-maintenance reviews, continuous monitoring, and regular employee training on system operations with a focus on usfallprotection. Digital monitoring tools provide real-time alerts for potential issues, and regular reviews of maintenance records against updated regulatory guidelines help keep lifeline systems compliant. A strong safety culture supports operational continuity and safeguards personnel and assets.
How Do Safety System Fabrication and Certification Impact Worker Safety and Industrial Productivity?
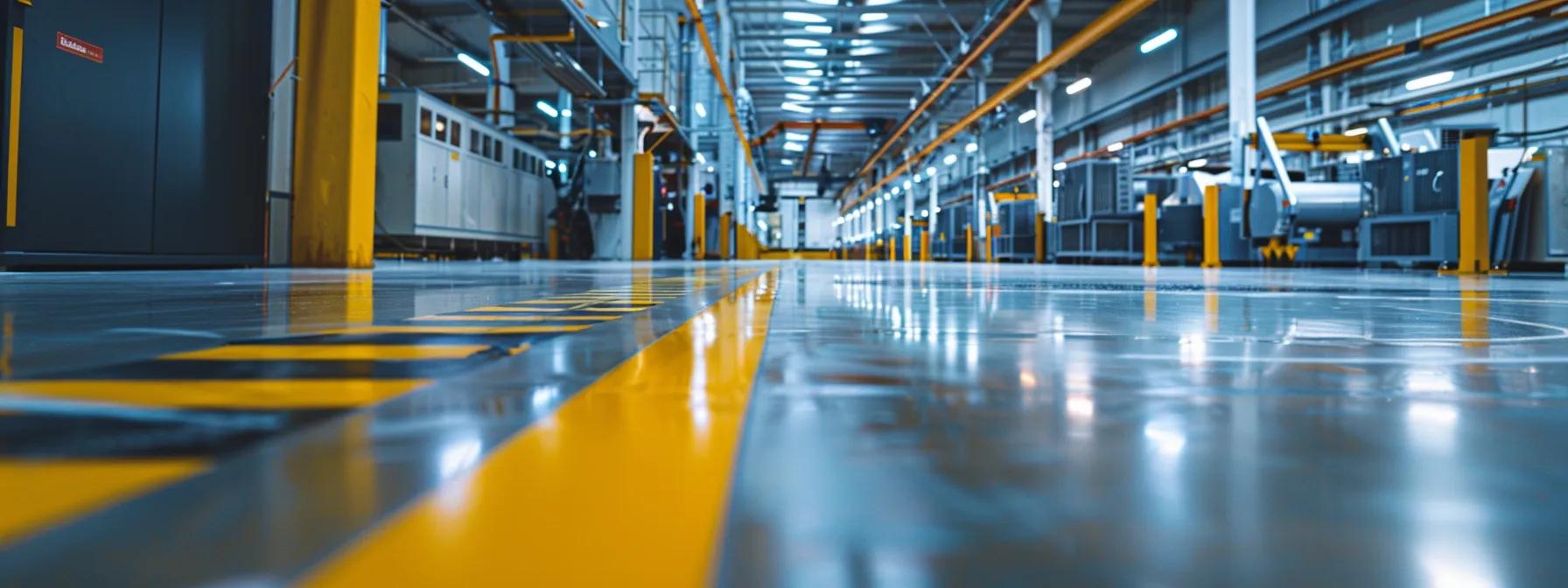
Certified safety systems such as ladder systems and lifeline systems are critical for worker safety and industrial productivity by mitigating risks and ensuring a secure work environment. Accurate fabrication, meticulous design-installation, and robust certification protect employees from hazards while reducing unplanned downtime and costly accidents. Improved worker confidence and operational continuity directly contribute to more efficient, productive industrial processes. To maintain these high standards, companies are encouraged to get a free quote for annual-maintenance services.
What Role Do Certified Safety Systems Play in Accident Prevention?
Certified safety systems, including usfallprotection measures, are designed to detect, alert, and mitigate hazardous conditions before accidents occur. By meeting strict regulatory standards and undergoing thorough testing, these systems not only ensure public safety but also lead the design-installation process in various industries-we-serve applications. Automated shutdown features, real-time monitoring, and redundant safety protocols, combined with periodic annual-maintenance checks, work together to correct any deviation from safe operating conditions, thereby reducing accident rates and protecting lives.
How Does Reliable Safety System Installation Minimize Downtime?
Reliable installation minimizes downtime by ensuring accurate system integration, efficient commissioning, and a comprehensive design-installation process that includes ladder systems for enhanced safety. Correctly installed systems that integrate guardrail systems work seamlessly with existing processes, reducing false alarms and malfunctions that can halt operations. Timely post-installation testing and calibration, followed by scheduled annual-maintenance and checks on lifeline systems, help avoid disruptions during critical production periods, ensuring a continual production flow and reducing non-productive downtime.
What Are the Long-Term Cost Savings of Certified Safety Systems?
Certified safety systems including ladder systems offer long-term savings by reducing accident-related expenses, lowering insurance premiums, and enhancing operational efficiency. Properly fabricated, installed, and certified systems following design-installation best practices and supported by annual-maintenance protocols lessen the chance of catastrophic failures that lead to expensive repairs or liability claims. Enhanced worker safety, bolstered by effective usfallprotection measures, also reduces absenteeism and increases productivity, offsetting the initial investment through decreased risk and higher production uptime.
What Are the Latest Trends and Innovations in Industrial Safety System Fabrication and Certification?
Recent trends and innovations are driving improvements in reliability, efficiency, and integration within industrial safety systems such as ladder systems and lifeline systems. Advancements in materials science, digital technology, and automation—supported by expert design-installation and regular annual-maintenance—are leading to smarter, more responsive systems that meet modern challenges. Trends such as remote monitoring, digital twin simulations, and advanced sensor networks are enhancing risk management and enabling continuous improvement. For additional insights, visit our about-us page, explore industries-we-serve, or read our blog. If you’re interested in upgrades, get a free quote to explore usfallprotection options.
How Are New Materials and Technologies Improving Safety System Reliability?
Innovative high-strength alloys, corrosion-resistant coatings, and advanced composites enhance safety system durability in harsh environments. Modern sensor technologies, including wireless detectors and real-time data analytics, offer greater precision and rapid response. As a result, systems built with these technologies are more robust, require less maintenance, and provide continuous protection.
What Advances Are Being Made in Certification Processes?
Certification processes are increasingly leveraging digital tools and automation to streamline testing, documentation, and inspections. Remote diagnostics, cloud-based data collection, and automated reporting reduce human error and speed up the certification cycle. Enhanced simulation models and virtual testing environments help ensure that systems consistently meet or exceed international standards.
How Is Digital Integration Enhancing Safety System Monitoring and Compliance?
Digital integration transforms monitoring by offering continuous, real-time tracking of system performance and compliance. Integration with smart sensors, centralized platforms, and software analytics gives facility managers detailed insights into operational status, potential hazards, and maintenance needs. This digital oversight enables prompt corrective actions, predictive maintenance, and data-driven decision-making, ensuring systems remain fully operational and compliant.
Frequently Asked Questions
Q: How often should safety systems be inspected?
A: They should typically be inspected at least annually, with more frequent checks in high-risk environments.
Q: What certifications are most commonly required for industrial safety systems?
A: Certifications often include IEC 61508, IEC 62061, ISO 45001, and compliance with OSHA and NIOSH guidelines.
Q: Can customized safety systems improve industrial productivity?
A: Yes, customization tailors systems to specific operational needs, reducing downtime and preventing accidents.
Q: How do digital monitoring tools enhance safety systems?
A: They provide real-time data for predictive maintenance and immediate response to anomalies, ensuring continuous compliance and improved safety.
Q: What are the benefits of combining fabrication, installation, and certification services?
A: Combining these services streamlines communication, shortens project timelines, maintains consistent quality, and often reduces costs.
Q: How do advanced materials contribute to safety system performance?
A: Advanced materials like high-strength alloys and corrosion-resistant coatings enhance durability, reduce maintenance frequency, and improve system reliability in harsh conditions.
Final Thoughts
Certified safety systems are essential investments for any industrial operation. By ensuring precise fabrication through custom design and high-quality materials, followed by meticulous installation and rigorous certification, these systems protect workforce integrity and optimize performance. The integrated approach reduces downtime, enhances productivity, and provides significant long-term cost savings by preventing accidents and ensuring regulatory compliance. As innovations in digital monitoring and advanced materials continue to evolve, industrial safety systems will become even more adaptive, reliable, and efficient, securing the future of high-risk operations around the globe.