Transforming Fall Protection: From Risk Management to Safety Culture
Building a long-term safety program is essential for organizations (industries-we-serve) committed to protecting employees using lifeline-systems and guardrail systems to ensure operational efficiency. Leveraging expert design-installation practices and annual maintenance services, this article examines the shift from traditional risk management to a holistic safety culture, offering data-supported insights, real-world examples, and expert recommendations to support sustainable workplace safety. For further details, visit usfallprotection.com or explore our blog to get a free quote.
What Is the Difference Between Risk Management and Safety Culture?
Risk management focuses on identifying, evaluating, and controlling hazards using quantitative and qualitative assessments. It relies on specific measures such as inspections, control protocols, annual maintenance, and periodic reviews to reduce incidents. In contrast, safety culture is about fostering shared values, attitudes, and practices among employees and leadership, with insights available on the about us page that highlights our industries-we-serve. For example, while a manufacturing plant may reduce incidents by following risk management measures, a true safety culture—where every employee participates in training, discussions, and incorporates strategies like guardrail systems and lifeline-systems—can result in up to 30% fewer accidents.
How Does Risk Management Identify and Control Workplace Hazards?
Risk management uses systematic risk assessments, audits, and tools such as root cause analysis and quantitative metrics. Once hazards are identified, organizations control them with administrative controls, engineering solutions and design-installation strategies, proper personal protective equipment (including Anchor text: ladder systems), and redesigning processes. Companies have observed incident reductions of around 25% when integrating automated alarms, regular audits and annual maintenance into their frameworks.
Why Is Safety Culture More Than Just Compliance?
Safety culture goes beyond compliance by transforming safety into a shared personal value rather than a box-ticking exercise. It encourages continuous communication, employee empowerment, and proactive hazard identification. This approach can boost overall safety by 40%, as employees engage in peer-to-peer feedback and brainstorming sessions that reduce near-misses and accidents.
What Are the Benefits of Moving From Risk Management to Culture Shift?
Transitioning to a safety culture can lead to higher employee engagement, improved productivity, and fewer incidents. Companies with robust safety cultures often experience up to a 50% drop in lost workdays and improved staff retention. Moreover, this shift enhances reputation, regulatory compliance, and overall resilience, ensuring safety is maintained even during organizational changes.
How Do You Develop an Effective Safety Program?
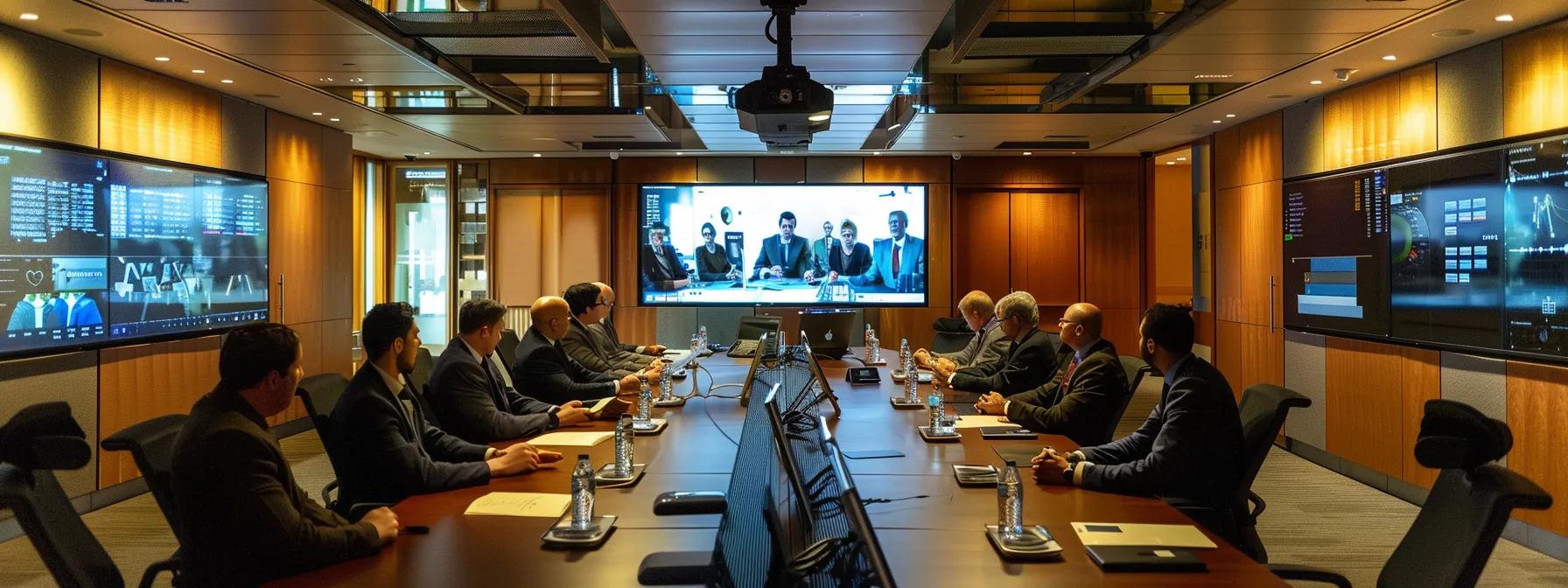
An effective safety program begins with clear safety goals and a design process that integrates risk assessments, tailored policies, and active engagement at all levels of an organization. Success relies on leadership, continuous improvement, and data-driven feedback.
What Steps Are Involved in Safety Program Design?
A typical design process involves: 1. Hazard Identification and Risk Assessment: Systematically identifying hazards through audits, interviews, and accident data. 2. Policy and Procedure Development: Creating clear guidelines that define safety protocols and responsibilities. 3. Resource Allocation: Ensuring budgets, tools, and training resources are in place. 4. Implementation: Rolling out safety measures with defined timelines, roles, and performance metrics. 5. Monitoring and Evaluation: Using quantitative metrics and feedback loops to measure effectiveness and make adjustments.
For example, one construction firm reduced injuries by 35% after integrating real-time incident reporting and monthly safety reviews into its program.
How Can Customized Safety Programs Meet Industry Needs?
Customized programs address specific hazards and regulatory demands unique to each industry. In healthcare, for instance, the focus is on infection control and ergonomics, while manufacturing may emphasize machinery safeguards and hazardous material handling. Utilizing industry-specific data and guidelines (e.g., from the National Safety Council) can reduce incident risks by over 30%. Tailored training modules, drills, and emergency plans ensure relevance for situations such as fall risks or chemical exposures.
What Role Does Training and Education Play in Safety Programs?
Ongoing training and education are the backbone of safety programs. Regular workshops and e-learning modules keep employees current on best practices, technological advancements, and regulatory updates. Data indicates that regular safety education can lower incident rates by as much as 40% by fostering accountability and continuous improvement.
How Can Organizations Enhance Safety Culture for Long-Term Success?
Enhancing safety culture requires creating an environment that values open communication, continuous learning, and proactive safety engagement. Embedding safety into daily operations strengthens long-term success.
What Strategies Foster Employee Engagement in Safety?
Key strategies include: – Regular Safety Meetings and Workshops: Open discussions help review hazards, near-misses, and improvement suggestions. – Reward and Recognition Programs: Acknowledging safe behavior boosts morale and accountability. – Interactive Training Programs: Hands-on sessions, simulations, and virtual drills create memorable learning experiences.
For example, monthly “safety champions” awards have been linked to a 20% increase in compliance and a stronger collective sense of responsibility.
How Does Leadership Commitment Influence Safety Culture?
Leadership is critical for establishing a robust safety culture. When senior leaders participate actively in safety rounds and provide regular feedback, it motivates employees to adopt similar practices. Organizations with visible leadership engagement typically see safety performance improvements of about 30% or more.
What Communication Practices Support a Positive Safety Culture?
Effective communication is achieved through: – Safety Bulletins and Newsletters: These share tips, incident summaries, and success stories. – Digital Platforms: Mobile apps and intranet systems enable real-time hazard reporting and feedback. – Feedback Loops: Anonymous surveys and reporting systems ensure employees have a voice. One company reported a 50% increase in hazard reports after introducing a smartphone safety reporting app, which helped prevent potential accidents.
How Is Fall Risk Management Integrated Into Safety Programs?
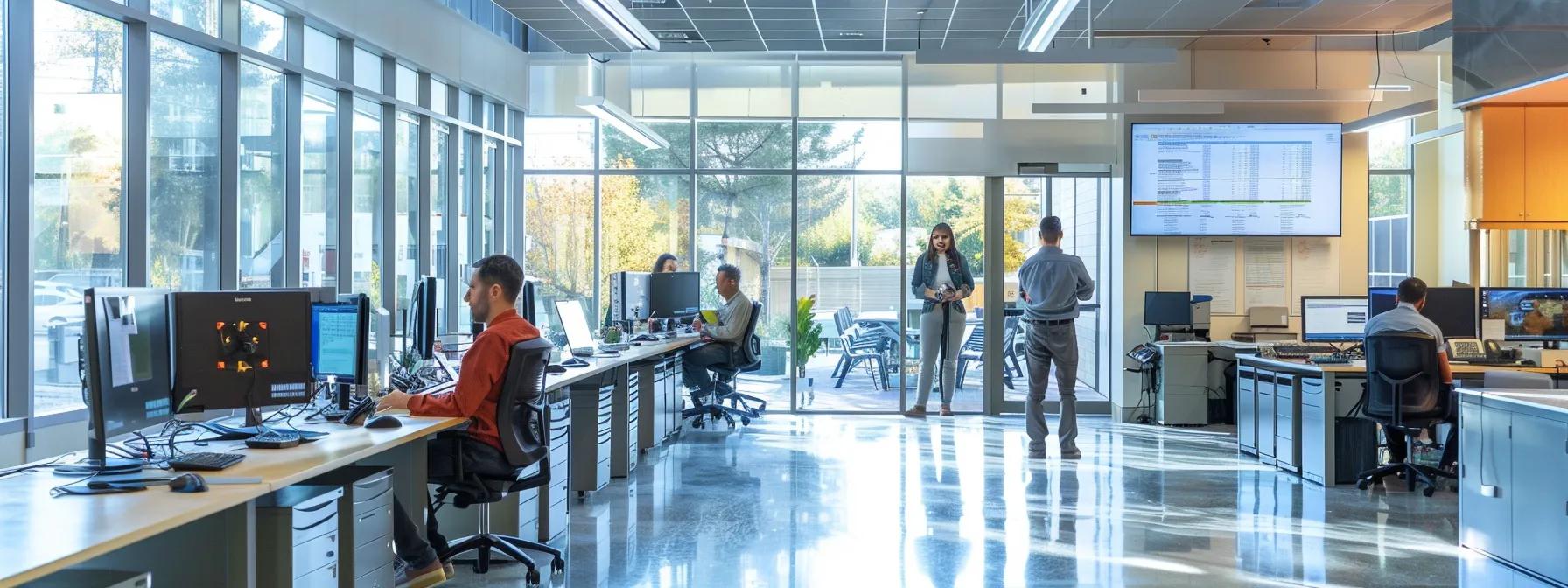
Fall risk management is critical, particularly in environments involving heights or uneven surfaces. Its integration requires continuous monitoring, proper training, and advanced safety tools.
What Are Common Fall Hazards in the Workplace?
Frequent fall hazards include: – Unprotected Edges and Openings: Gaps without guardrails or barriers. – Slippery Surfaces: Wet or uneven floors that lead to slips. – Improper Use of Ladders and Scaffolding: Unsafe setups increase risk. Regular inspections and risk assessments have demonstrated that addressing these issues can reduce falls by up to 45%.
How Can Fall Prevention Be Embedded in Safety Training?
Effective fall prevention training combines theory with practice: – Proper Ladder and Scaffold Use: Hands-on sessions simulate real scenarios. – Personal Protective Equipment (PPE): Training on the correct use of harnesses, non-slip footwear, and guardrails. – Emergency Response Procedures: Drills ensure employees know first aid and rescue protocols. Studies suggest that well-trained employees are 35% less likely to experience falls, especially when training is refreshed regularly.
What Tools and Technologies Support Fall Risk Monitoring?
Advanced tools include: – Wearable Safety Devices: These detect falls with accelerometers and gyroscopes and send immediate alerts. – Real-Time Monitoring Systems: Video analytics and sensor networks identify hazards in high-risk areas. – Mobile Reporting Apps: Enable on-the-spot reporting of potential risks. Implementing these tools has resulted in fall incident reductions of around 30% in industries like construction and warehousing.
How Do You Measure and Improve Safety Program Performance?
Continuous measurement and improvement are vital for safety programs. Organizations rely on various metrics, analytics, and feedback tools to refine and adapt their safety strategies.
What Metrics Track Safety Program Effectiveness?
Effective safety metrics include: – Incident Frequency Rate (IFR): The number of incidents per 100 employees. – Lost Time Injury Rate (LTIR): Injuries causing lost workdays, indicating both frequency and severity. – Near-Miss Reporting Rate: Higher reporting often signals proactive hazard identification. – Training Completion and Audit Scores: These indicate the effectiveness of safety communication and compliance. Some organizations have achieved a 40% reduction in injuries over three years by consistently tracking these metrics.
How Can Data Analytics Drive Safety Improvements?
Data analytics transforms incident reports, audit data, and feedback into actionable insights. Predictive modeling can forecast high-risk periods, enabling timely interventions that reduce incident rates by about 25%. Dashboards and KPIs support agile safety program management.
What Are Best Practices for Ongoing Safety Program Evaluation?
Best practices include: – Regular Safety Audits: Scheduled and surprise audits verify ongoing compliance. – Employee Surveys: Anonymous feedback helps pinpoint areas for improvement. – Benchmarking: Comparing against industry standards highlights strengths and weaknesses. – Continuous Improvement Cycles: Using Plan-Do-Check-Act (PDCA) cycles to refine safety measures. These practices ensure that safety programs evolve with emerging risks and technological advancements.
Key Challenges When Shifting from Risk Management to Safety Culture
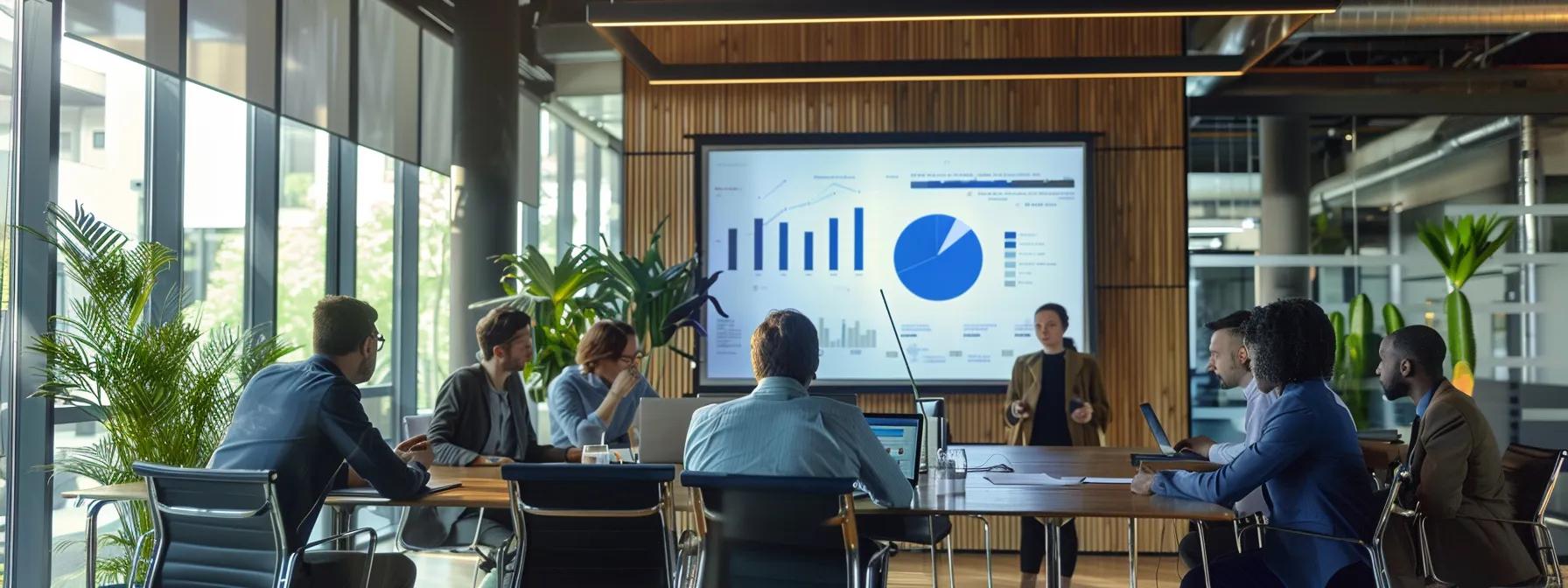
Shifting from risk management to a comprehensive safety culture involves challenges such as resistance to change, communication breakdowns, limited resources, and maintaining momentum. Employees accustomed to compliance-focused methods may be skeptical about new approaches.
How Can Resistance to Change Be Overcome?
Overcoming resistance requires: – Transparent Communication: Clearly explain the benefits of a safety culture. – Pilot Programs: Small-scale projects can demonstrate quick wins. – Employee Involvement: Engage staff in decision-making and safety committees. – Incentive Programs: Reward early adopters and safety champions. Targeted interventions have reduced resistance by over 35% in some cases.
What Are Typical Barriers to Employee Engagement?
Common barriers include: – Lack of Awareness: Employees may not grasp the full impact of proactive safety measures. – Perceived Time Constraints: Additional protocols can be seen as burdensome. – Insufficient Training: Employees may feel unprepared without proper instruction. – Inadequate Rewards: Failing to recognize contributions can lead to disengagement. Organizations that address these barriers through comprehensive programs have seen a 20–30% increase in participation.
How Do You Maintain Momentum for Long-Term Safety Culture?
Maintaining momentum requires: – Regular Updates and Training Refreshers: Ensure all employees stay current. – Leadership Visibility: Continued involvement from senior management is key. – Periodic Reviews and Reassessments: Use data analytics to adapt to emerging trends. – Celebration of Milestones: Recognize achievements to reinforce positive behavior. Such ongoing efforts are essential to making safety a core, enduring value.
How Can Organizations Sustain Safety Programs That Last?
Long-term sustainability in safety programs is achieved by embedding safety in daily operations and maintaining continuous training. This requires integrating safety into every organizational function and fostering a proactive approach through leadership and employee engagement.
What Role Does Continuous Training Play in Sustainability?
Continuous training keeps employees updated on new risks, technologies, and best practices. Regular sessions, refresher courses, and e-learning help maintain high awareness and competency, contributing to a 20–25% improvement in compliance. Ongoing education equips staff with the skills to identify and mitigate hazards effectively.
How Can Safety Culture Be Embedded Into Daily Operations?
Embedding safety culture involves: – Incorporating Safety Metrics in Performance Reviews: Linking safety outcomes to individual performance fosters accountability. – Daily Safety Briefings: Toolbox talks and briefings keep safety top of mind. – Safety Reminders and Visual Cues: Posters and digital displays reinforce key messages. – Employee-Driven Committees: Regular safety team meetings promote peer mentoring. These practices help integrate safety so deeply that it becomes a natural part of everyday work.
What Are Examples of Successful Long-Term Safety Programs?
Industries such as manufacturing, healthcare, and construction offer examples of successful programs. One electronics manufacturer reduced workplace injuries by 45% over five years through continuous training, rigorous audits, and regular recognition of milestones. Similarly, a major healthcare provider improved both patient and staff safety by integrating safety indicators into employee evaluations. These examples demonstrate the benefits of consistently prioritizing and integrating safety.
How Do You Measure and Improve Safety Program Performance?
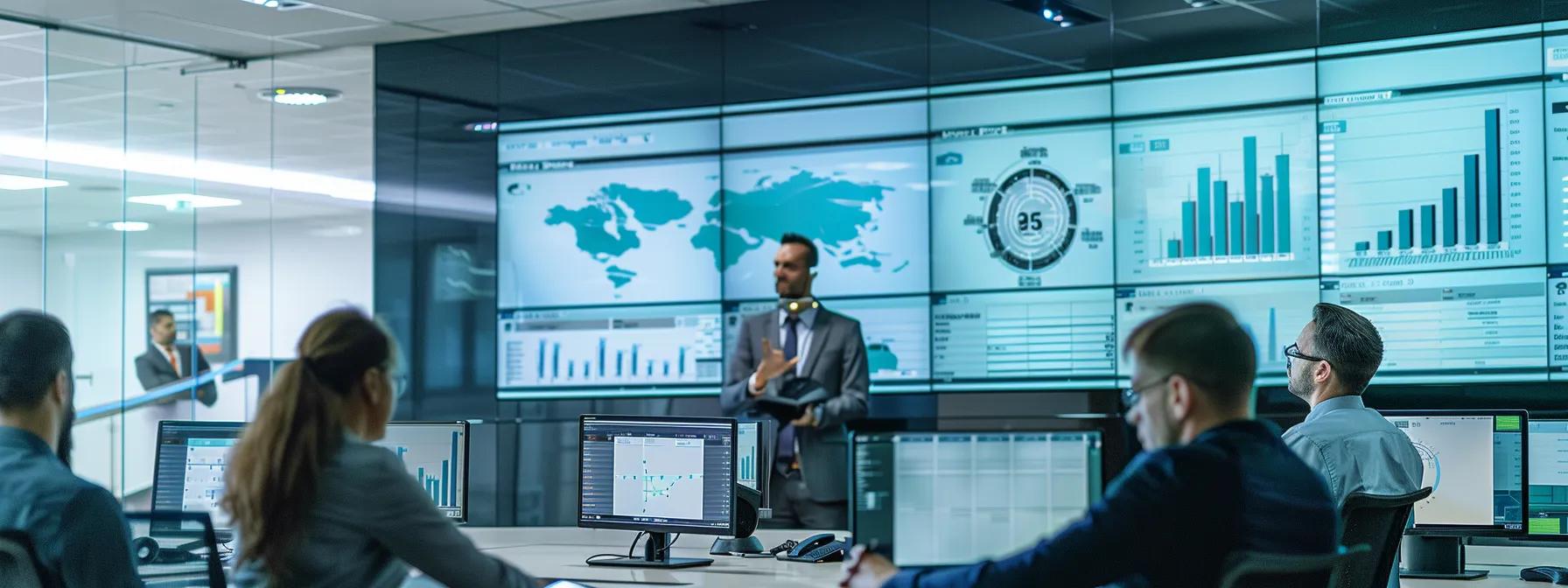
Ongoing measurement drives the continuous improvement of safety programs. Organizations use specific metrics and review processes to assess and adjust their approaches.
What Metrics Track Safety Program Effectiveness?
Key metrics include: – Incident Frequency Rate (IFR): Measures overall safety climate. – Lost Time Injury Rate (LTIR): Tracks the severity of injuries. – Near-Miss Reporting Rate: Indicates proactive hazard identification. – Training Completion and Audit Scores: Reflect effective communication and compliance. Consistent tracking has helped some organizations achieve a 40% reduction in workplace injuries over several years.
How Can Data Analytics Drive Safety Improvements?
By converting raw data into actionable insights, predictive analytics can identify high-risk periods and trends, enabling targeted interventions that have reduced incident rates by approximately 25%. Real-time dashboards and KPIs ensure programs remain agile and responsive.
What Are Best Practices for Ongoing Safety Program Evaluation?
Best practices include: – Regular Internal Audits and Benchmarking: Ensure continuous adherence to protocols. – Employee Surveys and Management Reviews: Collect feedback to refine programs. – Continuous Improvement Cycles (PDCA): Foster ongoing safety enhancements. These methods help keep safety programs relevant and effective.
Frequently Asked Questions
Q: What is the key difference between risk management and safety culture?
A: Risk management involves identifying and controlling hazards through specific measures, while safety culture embeds safety as a core organizational value, improving overall behavior and engagement.
Q: How can continuous training improve workplace safety?
A: It equips employees with up-to-date practices and emergency protocols, significantly reducing incident rates and ensuring ongoing effectiveness.
Q: What metrics are most useful in tracking a safety program’s effectiveness?
A: Key metrics include Incident Frequency Rate, Lost Time Injury Rate, near-miss reporting rates, and training completion and audit scores.
Q: How does leadership impact the success of a safety program?
A: Active leadership sets the tone for safety by driving accountability and engaging directly in safety activities, which encourages employees to follow best practices.
Q: Can technological tools really reduce fall incidents?
A: Yes, tools such as wearable devices, real-time monitoring systems, and mobile reporting apps have been shown to reduce fall incidents by up to 30% by addressing hazards promptly.
Q: What challenges should organizations expect when shifting to a safety culture?
A: Challenges include overcoming resistance to change, ensuring consistent engagement, and maintaining momentum via regular training and robust feedback systems.
Q: How can data analytics contribute to the ongoing improvement of safety programs?
A: Data analytics transforms incident reports and audit data into actionable insights, enabling the use of predictive modeling to preemptively identify risks and drive targeted improvements.
Final Thoughts
This article underscores the transition from traditional risk management to an all-encompassing safety culture as a pathway to improved workplace safety. By embedding safety into daily operations through continuous training, open communication, and dedicated leadership, organizations can reduce incident rates, boost employee engagement, and build sustainable safety programs. Data-driven strategies and advanced technologies further enhance the effectiveness of these programs, making proactive safety a cornerstone of long-term operational success.