How to Implement OSHA-Compliant Fall Protection in Aircraft Hangars
Aircraft hangar fall protection integrates guardrails, lifeline systems, and safety net solutions to minimize height-related risks in maintenance bays and loading docks while meeting OSHA requirements.
Fall Hazards in Aircraft Hangars and Transportation Settings
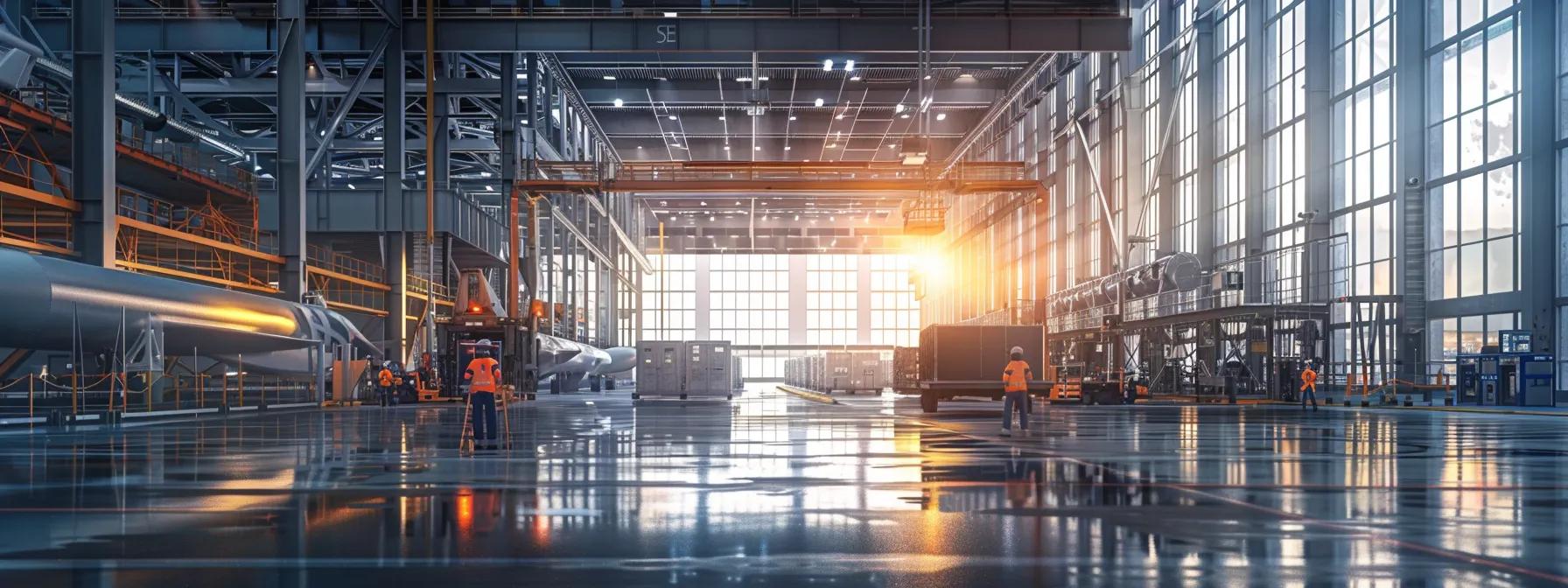
Aircraft hangars and adjacent transportation areas present multiple fall hazards due to elevated platforms, open edges, and moving equipment.
Hangar roof edges, mezzanine catwalks, loading docks, ladder-systems, and stair systems create potential drop zones from heights often exceeding 4 feet, which triggers OSHA compliance under 29 CFR 1910.23 and 1910.28. Implementing US fall protection and regular annual-maintenance ensures safety standards are met through our design-installation services.
Moving forklifts and railcars compound the hazard when personnel access elevated wings or fuselage surfaces, requiring reliable protection at every transition point.
What core systems are used for aircraft hangar fall protection?
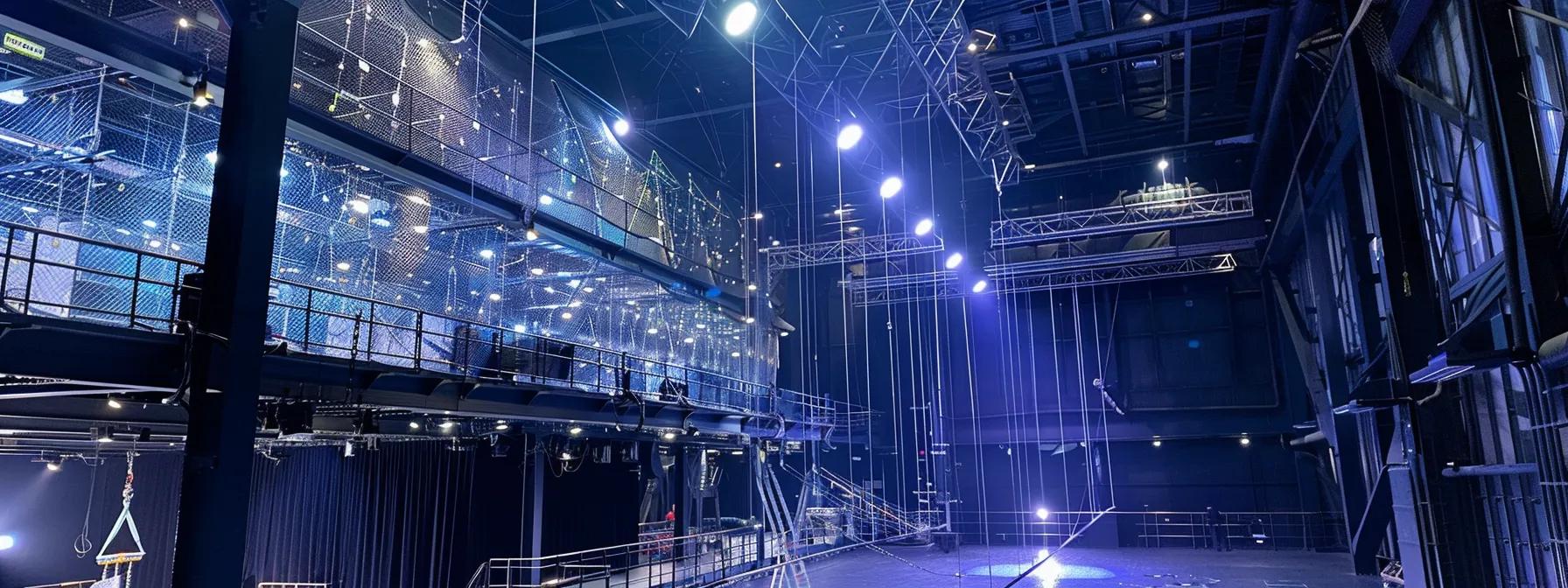
Core fall protection systems in aircraft hangars include guardrail systems, ladder-systems, safety net installations, personal fall arrest equipment, warning lines, and safety-monitor methods. We also provide design-installation and annual-maintenance services to ensure optimal safety and performance. Learn more about us and the industries we serve by visiting our blog or get a free quote today.
Guardrails with a top rail at 42 inches above walking surfaces and midrails at 21 inches satisfy OSHA 1910.28(d)(1) and protect roof edges and mezzanines.
Safety nets, installed not more than 30 feet below the work surface, comply with OSHA 1910.28(a)(1)(ii) and catch tools, debris, or personnel when overhead crane bays are open.
Which fall protection strategies apply in transportation facilities?
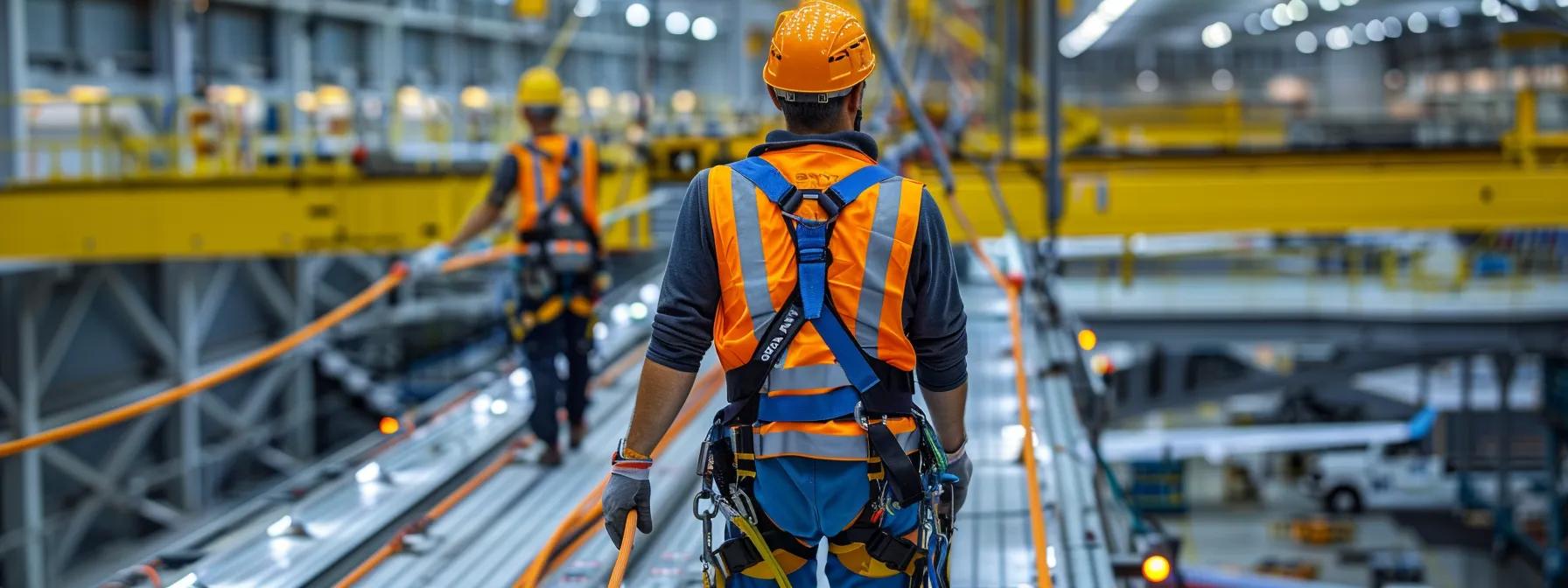
Transportation facilities leverage anchorage connectors, horizontal lifeline systems, ladder-systems, and specialized harnesses during annual-maintenance and fuel-truck loading. For more information, visit our about-us page or read our blog.
Horizontal lifeline systems allow workers to traverse wing edges or engine nacelles while remaining tied off to a continuous fall arrest line rated at 5,000 lbf minimum.
Shock-absorbing lanyards and self-retracting lifelines reduce arresting force to under 1,800 lbf, meeting OSHA 1926.502(d)(16) criteria during high-movement tasks.
How can OSHA-compliant measures be implemented in aviation workspaces?
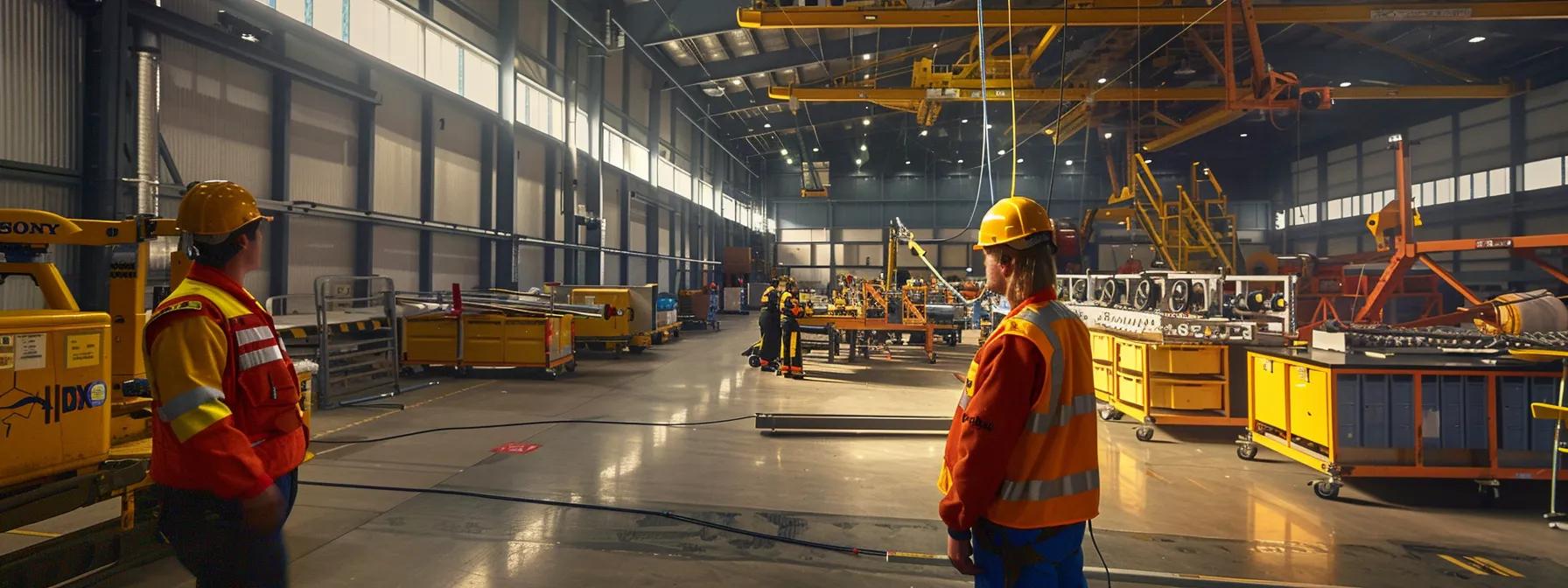
Implementing OSHA-compliant fall protection in aviation workspaces begins with a site-specific risk assessment per 29 CFR 1910.132 and 1910.140.
Facility managers must document hazard locations, select appropriate systems, train workers in fall protection procedures, and perform annual equipment inspections.
Training covers proper harness donning, anchor selection, rescue planning, and rescue equipment readiness to fulfill OSHA’s requirement for fall protection training under 1910.30(b).
What practical applications and case studies illustrate effective fall protection?
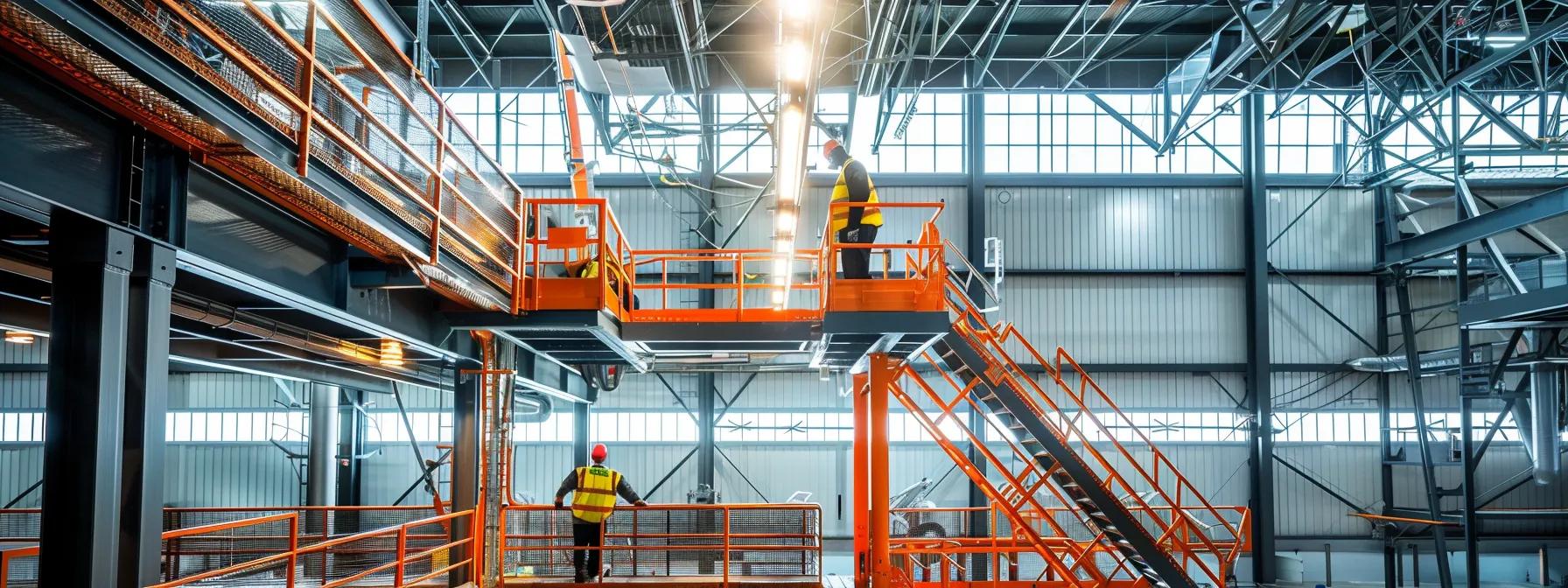
Practical case studies in major airline maintenance bases show a 45 percent reduction in lost-time injuries after installing combined guardrail and horizontal lifeline systems.
At a Midwestern hub, integration of warning line systems on low-slope hangar roofs reduced unprotected edge exposure by 60 percent within six months.
Another study published in the Journal of Safety Research (2021) reported elimination of fatalities over a two-year period following full implementation of personal fall arrest and safety net systems, including design-installation and annual-maintenance by US fall protection across the industries we serve.
What expert insights guide the selection of fall protection solutions?
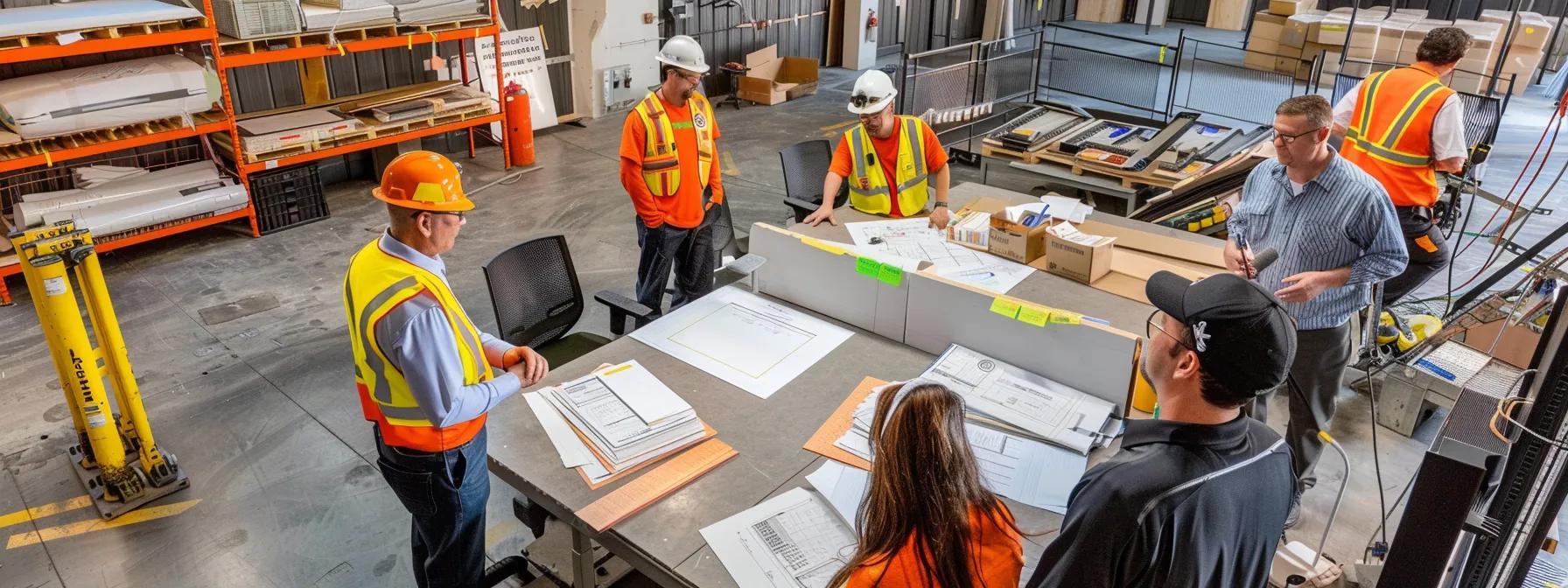
Experts recommend choosing passive systems like guardrails as first-line defense, supplemented by active systems where access is limited.
Consultants emphasize selecting anchor points with documented load tests, ensuring harnesses fit a range of body sizes, and specifying quick-attach connectors for efficiency.
Multi-disciplinary teams including safety engineers, aircraft mechanics, and compliance officers ensure that selected solutions align with both operational workflows and regulatory mandates.
Which components form a comprehensive fall protection system?
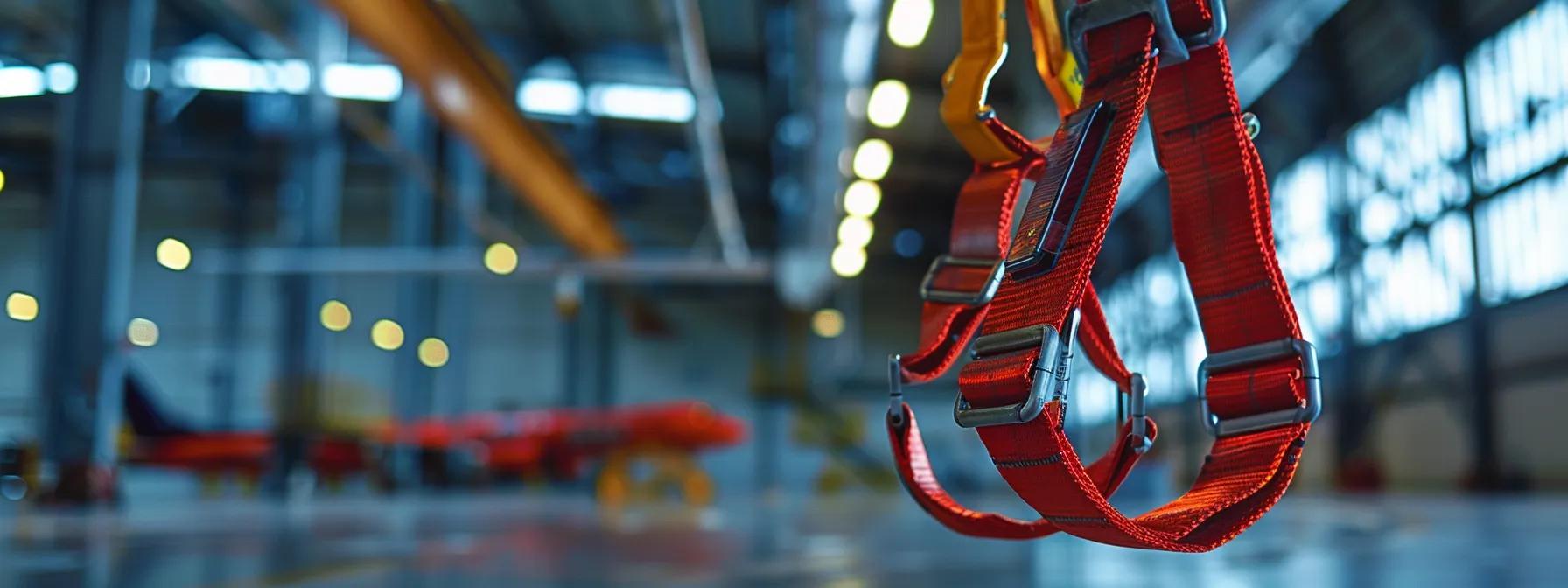
A comprehensive fall protection system comprises anchorage, body-worn gear, connectors, lifelines, and control measures such as guardrails and warning lines.
Each component must meet minimum performance criteria: anchorage points rated 5,000 lbf, harnesses rated 3,600 lbf, and shock-absorbing lanyards limiting deceleration to 1,800 lbf.
Site-specific system integration reduces overlap gaps and ensures seamless coverage across hangar floors, loading areas, and aircraft surfaces.
How do guardrail, safety net, and personal fall arrest systems compare?
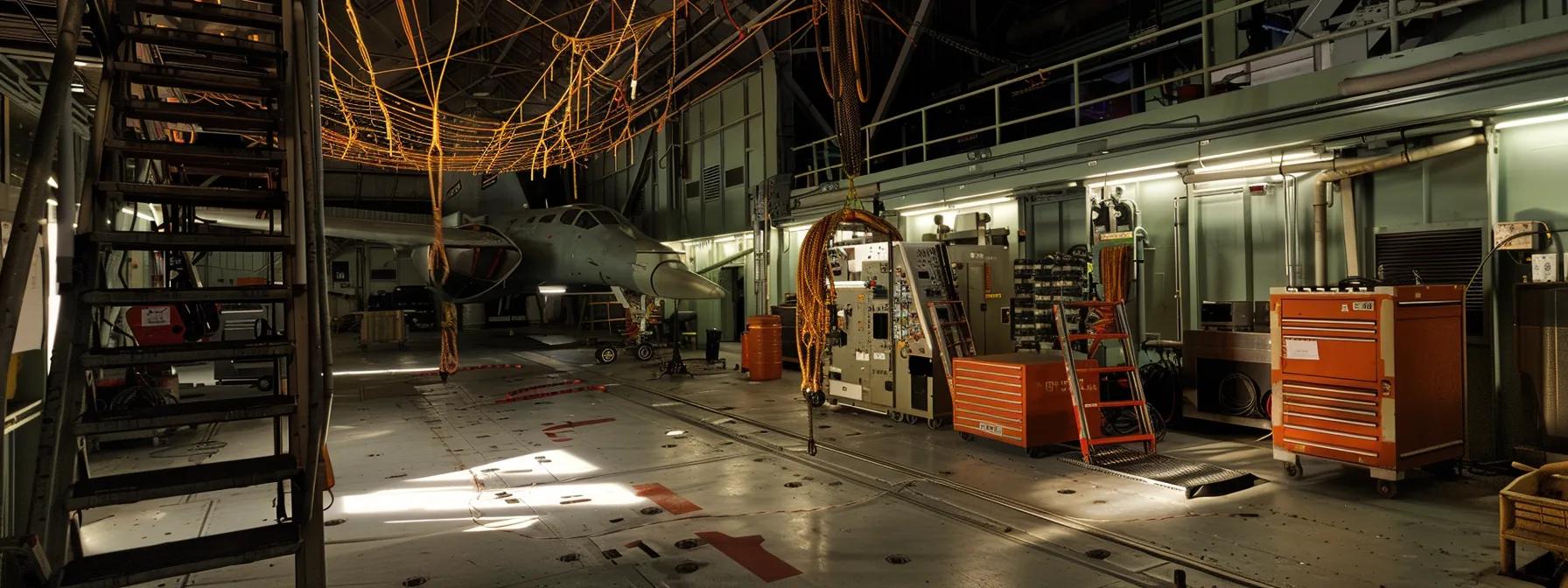
Guardrail, safety net, and personal fall arrest systems differ by installation cost, compliance code, and ideal application scenarios.
Guardrails provide continuous edge protection at a fixed cost of $10 per linear foot, while nets cost $15 per square foot and require specialized rigging.
Personal fall arrest systems cost $250 per worker set and are highly mobile, making them ideal for frequent access points on wings and tail assemblies.
Below is a comparison table summarizing attributes and use cases for each primary system.
System | Key Attribute | OSHA Standard | Best Use Case |
---|---|---|---|
Guardrail System | 42″ top rail, 21″ midrail, toeboard | 1910.28(d)(1) | Hangar perimeter, mezzanines |
Safety Net System | Mesh nets no more than 30′ below | 1910.28(a)(1)(ii) | Open crane bays, maintenance pits |
Personal Fall Arrest | Harness, lanyard, anchor connector | 1926.502 | Aircraft surfaces, confined spaces |
Warning Line System | Flagged rope/chain 6′ from edge | 1910.28(b)(3)(ii) | Low-slope roofs, dock edges |
Safety Monitor | Dedicated observer for unprotected areas | 1910.28(b)(3)(vi) | Short-term roof tasks |
This comparison illustrates how each system aligns with specific aviation maintenance tasks and regulatory codes.
What are the five essential components of a fall protection plan?
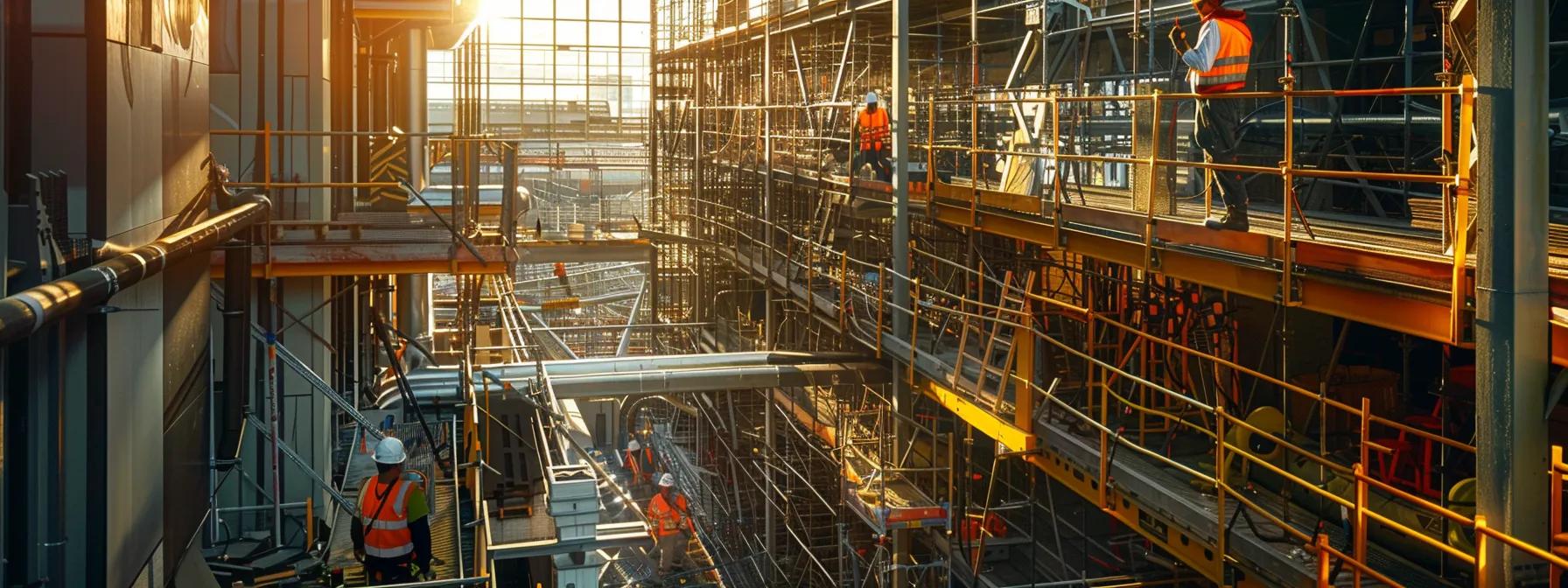
A robust fall protection plan integrates site assessment, system selection, worker training, equipment inspection, and rescue procedures.
Site assessments identify hazard zones and determine where passive or active systems are needed while maintaining guardrail continuity.
Training ensures workers understand harness inspection, anchor point selection, and emergency rescue requirements per OSHA 1910.146.
Key components include:
- Hazard assessment with documented site map and elevations
- Selection of systems (guardrails, nets, personal arrest)
- Comprehensive worker training and certification records
- Routine inspection schedules and maintenance logs
- Rescue planning with pre-designated equipment and protocols
These elements form an integrated approach that reduces injury risk and ensures regulatory compliance.
How is annual maintenance performed on fall protection equipment?
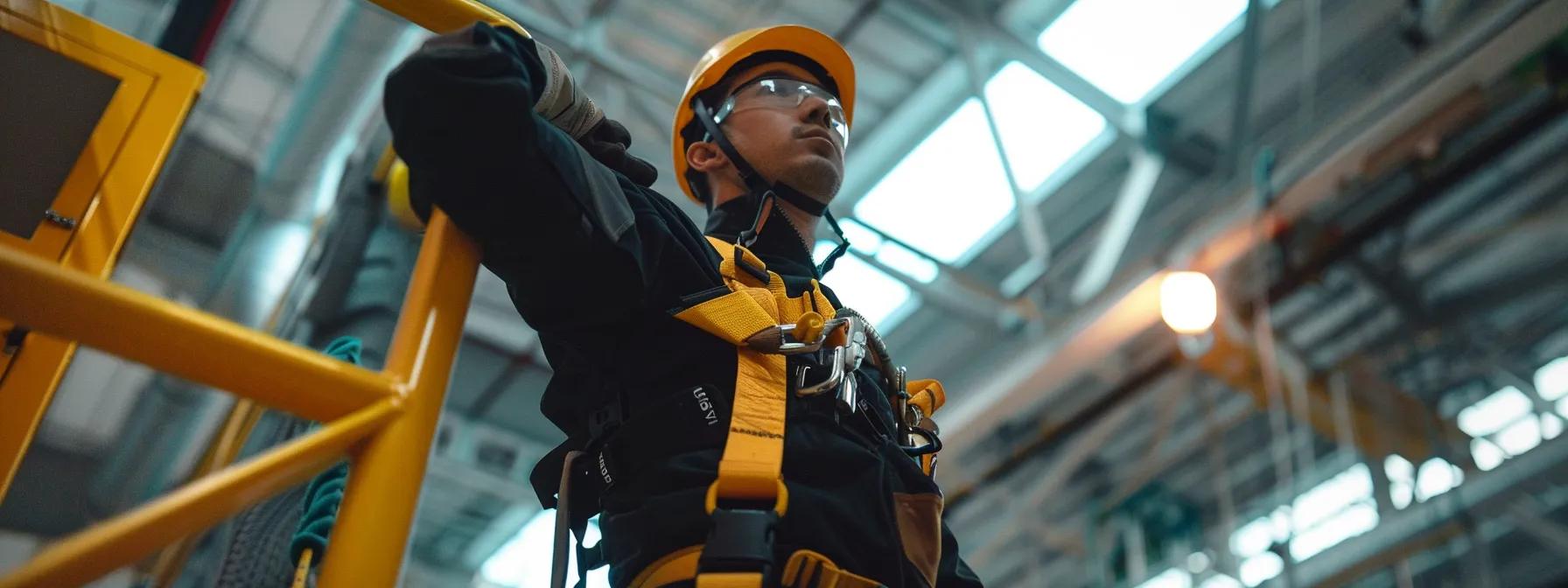
Annual maintenance on fall protection equipment involves inspection, testing, and recordkeeping per OSHA 1910.66 and ANSI Z359.2.
Qualified inspectors examine harness webbing for tears, metal connectors for corrosion, and lifeline tension to ensure proper shock-absorption.
Records must detail inspection date, inspector credentials, equipment ID, and any corrective actions taken, creating an audit trail for compliance reviews.
What visualization could illustrate cost versus protection coverage?
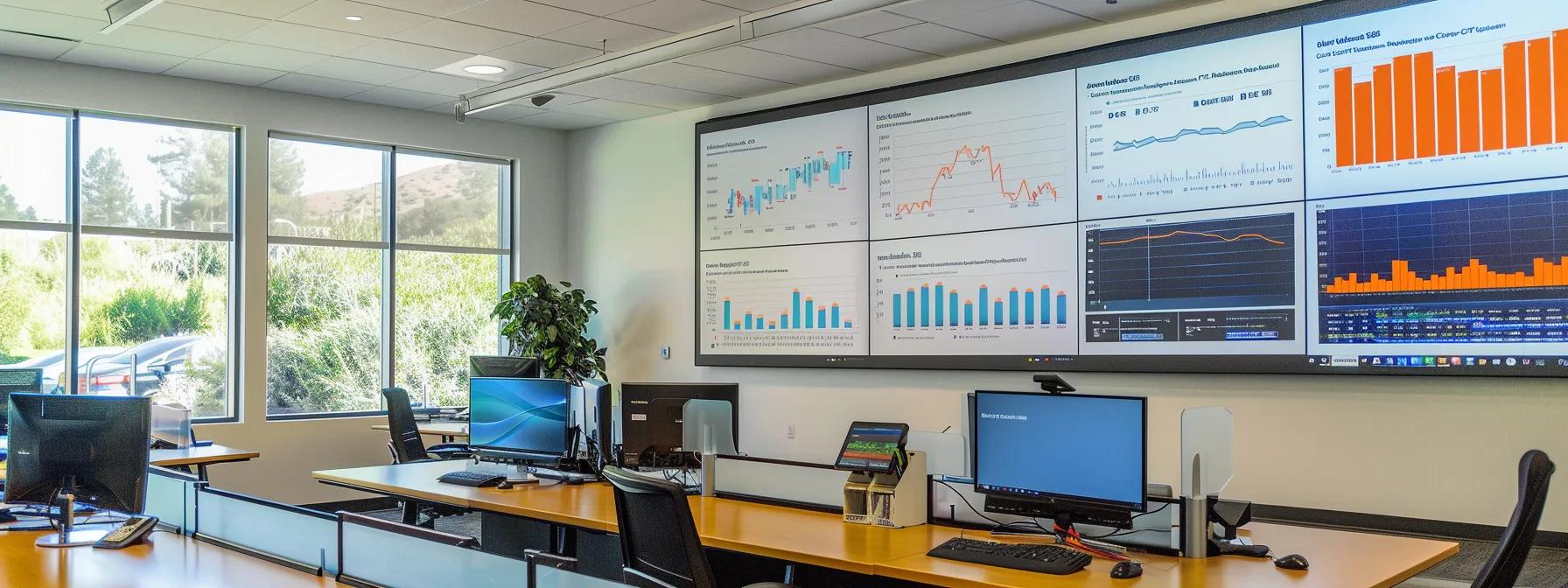
A bar chart comparing installation cost per square foot to coverage area efficiency for guardrails, nets, and lifeline systems could clarify budgeting decisions.
Such a visualization would highlight that guardrails cost $10 per foot but cover 100 sq ft per crew, while nets cost $15 per sq ft covering 50 sq ft per crew.
Including operational downtime metrics further enhances decision-making by showing protection uptime percentages over a year.
Visualization prompt: “Bar chart of cost per unit versus coverage area and downtime impact for primary fall protection systems.”