Developing Effective Fall Risk Management and Prevention Programs for Industrial Safety
Industrial falls are a leading cause of workplace injuries and fatalities across industries-we-serve. Effective fall risk management is essential for maintaining a safe environment by identifying, assessing, and mitigating fall hazards, ensuring us fall protection for all workers. This guide outlines key steps for developing, implementing, and managing fall prevention programs in industrial settings, focusing on assessment procedures, design-installation of equipment, training, OSHA regulations, lifeline-systems for rescue planning, and continuous program improvement.
What Is Fall Risk Management and Why Is It Crucial for Industrial Safety?
Fall risk management, supported by us fall protection guidelines, is a systematic process designed to reduce workplace injuries by identifying fall hazards, analyzing risks, and implementing prevention strategies. In environments with elevated platforms, including ladder systems, unguarded edges where guardrail-systems are vital, slippery surfaces, or confined spaces, robust fall prevention programs not only lower injury rates and reduce costly litigation but also promote a culture of safety and compliance that enhances productivity and protects workers’ health.
How Does Fall Risk Management Reduce Workplace Injuries?
A comprehensive fall risk management strategy involves: – Hazard Identification: Regular surveys and audits across the facility, including evaluations of ladder systems and guardrail-systems to ensure optimal fall protection. – Risk Assessment: Evaluating each hazard’s severity and likelihood using standardized checklists and risk matrices, with attention to design-installation standards for lifeline-systems. – Mitigation Strategies: Prioritizing corrective actions in high-risk areas, incorporating annual-maintenance routines to sustain safety measures. – Inspections and Audits: Regular reviews to ensure safety measures remain current.
This proactive approach has led many organizations to report a significant reduction in slips, trips, and falls.
What Are the Key Components of a Fall Prevention Program?
A successful fall prevention program includes: 1. Hazard Identification: Surveys and safety audits to pinpoint fall risks. Our approach, rooted in us fall protection best practices, ensures that even the lesser-known hazards in industries-we-serve environments are detected. 2. Risk Assessment and Analysis: Evaluating the severity and probability of each hazard while considering site-specific factors to guarantee comprehensive safety. 3. Engineering Controls and Equipment: Installing guardrails, harnesses, lanyards, and implementing guardrail-systems and ladder systems to enhance structural safety. 4. Administrative Controls and Policies: Establishing clear safety protocols, recordkeeping, and emergency procedures to support a culture of continuous safety. 5. Training and Competency: Regular training for both competent and authorized personnel. Facilities are encouraged to get a free quote for tailored training sessions that meet specific requirements. 6. Continuous Monitoring: Ongoing evaluations and updates to the program, including scheduled annual-maintenance checks to ensure sustained effectiveness.
These components transform reactive responses into a proactive safety-first culture.
Which Industries Face the Highest Fall Risks?
Industries such as construction, manufacturing, warehousing, oil and gas, and maintenance (industries-we-serve) are at high risk due to: – Elevated work surfaces and scaffolding (ladder systems, guardrail-systems) – Confined or slippery environments (us fall protection) – Heavy machinery operations
Understanding these risks allows companies to tailor prevention strategies and allocate resources effectively for regulatory compliance and worker protection.
How Do You Conduct a Comprehensive Fall Risk Assessment in Industrial Settings?
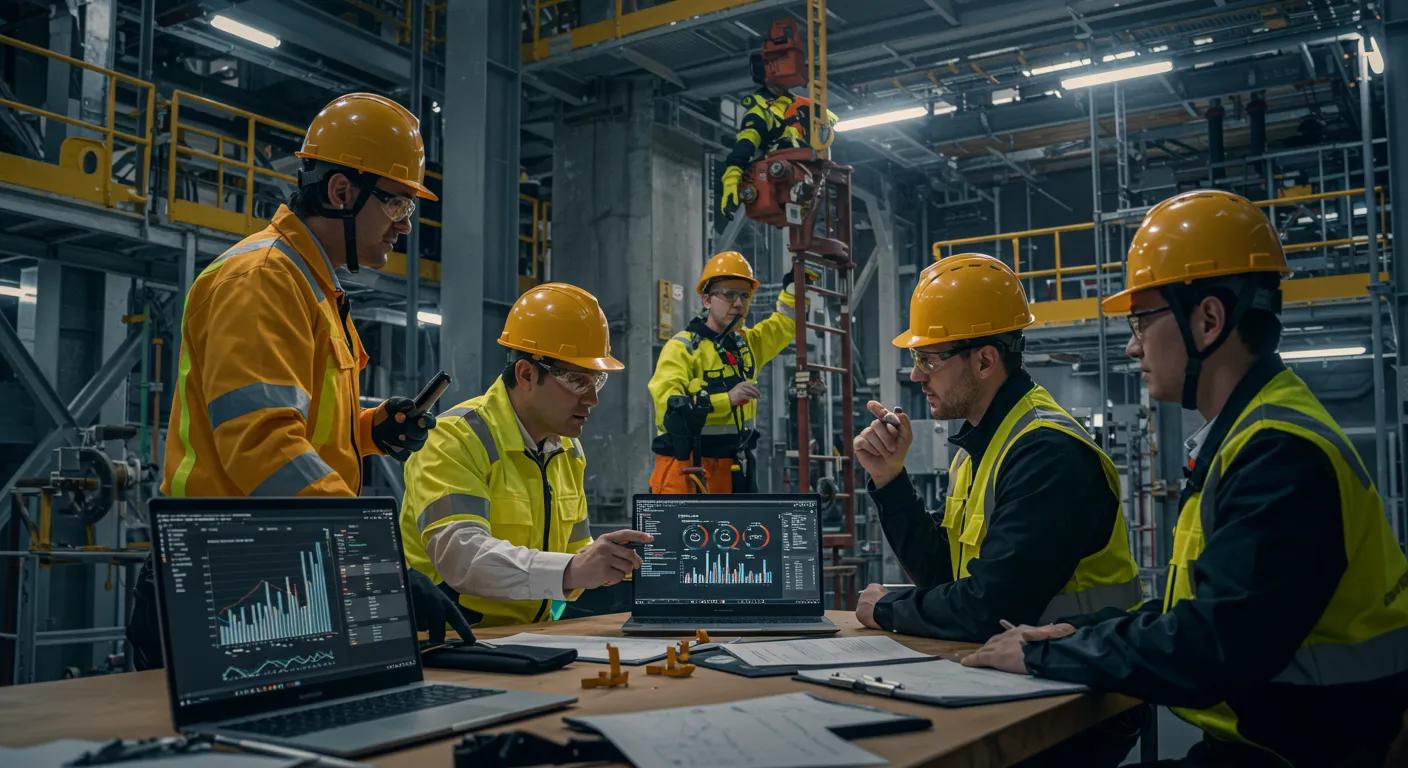
A detailed fall risk assessment under us fall protection evaluates the work environment and current safety measures through: – Work Area Reviews: Inspecting equipment, such as ladder systems and guardrail-systems (including periodic annual-maintenance), alongside established employee procedures. – Data-Driven Strategies: Using systematic observations to prioritize corrective actions and better serve industries-we-serve by guiding design-installation improvements.
What Steps Are Involved in Identifying Fall Hazards?
Begin by identifying all potential hazards: – Unprotected edges and openings (ensure implementation of guardrail-systems and us fall protection) – Slippery or uneven surfaces – Inadequate lighting (consider lifeline-systems for added safety) – Poorly maintained equipment (ladders, scaffolds) – inspect ladder systems and schedule annual-maintenance checks – Obstructed pathways For additional resources, visit industries-we-serve for further design-installation guidance.
Involving workers via safety meetings and checklists helps ensure comprehensive hazard identification.
How Is Risk Analysis and Evaluation Performed?
Risk analysis categorizes hazards based on: – Impact: From minor injuries to fatalities. – Frequency: Exposure rates and potential recurrence. – Prioritization: Immediate engineering controls for high-risk areas, such as an uncovered platform near busy production areas, where ladder systems and guardrail-systems are implemented as part of the design-installation process. Regular annual-maintenance ensures that lifeline-systems remain effective, contributing to enhanced us fall protection during operations.
Regular re-evaluation ensures that changes in the work environment are addressed promptly.
What Tools and Checklists Support Effective Site Surveys?
Effective assessments use: – Digital Checklists and Mobile Apps: For streamlined data collection; if you’re interested in learning more, get a free quote is available to guide your process. – Risk Assessment Software: Cloud-based platforms to record and report hazards with design-installation integration ensuring versatile functionality. – Inspection Guides: Structured methods for thorough surveys that support annual-maintenance checks. – Measurement Devices: To evaluate factors like temperature, friction, and lighting, providing key data for us fall protection protocols.
These tools, combined with periodic inspections, ensure that safety performance is continuously monitored.
What Types of Fall Protection Equipment Are Essential for Industrial Safety?
Selecting the right fall protection equipment is crucial. At us fall protection, our design-installation services ensure that the equipment matches the specific risks of your work environment while our annual-maintenance plans keep your systems compliant with regulatory standards. For more details, get a free quote or explore our blog and industries-we-serve to learn about our comprehensive safety solutions. Two main categories include: – Fall Arrest Systems: Designed to stop a fall (e.g., harnesses, lanyards, energy absorbers, lifeline-systems). – Fall Restraint Systems: Prevent a fall (e.g., fixed tethers, guardrails, guardrail-systems, ladder systems).
What Are the Differences Between Fall Arrest and Fall Restraint Systems?
- Fall Arrest Systems stop a falling worker, reducing descent distance and deceleration forces.
- Fall Restraint Systems prevent workers from reaching hazardous areas altogether.
For example, a fall arrest system may involve a full-body harness with an overhead lifeline, while a fall restraint system uses a fixed tether near an unprotected edge.
How Do You Choose the Right Harnesses, Lanyards, and Lifelines?
Consider: – Weight and Load Capacity: Each component must handle expected forces, as demonstrated in the performance of ladder systems and guardrail-systems. – Comfort and Fit: Properly fitted gear, following design-installation best practices, ensures both safety and usability. – Durability and Maintenance: Equipment should withstand industrial conditions; regular annual-maintenance is recommended to ensure longevity. – Certification: Compliance with OSHA and ANSI standards is mandatory and aligns with us fall protection requirements.
Manufacturers’ performance data and specification tables assist in making the best choice.
What Are Best Practices for Equipment Use and Maintenance?
Ensure equipment effectiveness through: – Routine Inspections: Daily or pre-use checks for damage as part of regular annual-maintenance procedures. – Proper Storage: Keeping equipment like ladder systems clean and dry. – Recordkeeping: Detailed logs of inspections and repairs help align with guidelines provided on our industries-we-serve page. – Training Programs: Regular instruction on equipment usage and maintenance – for more insights, visit our blog. – Following Manufacturer Guidelines: Adhering to lifecycle and replacement recommendations, as detailed in about us information.
These best practices maintain reliable safety support in hazardous work environments.
Why Is Fall Protection Training Vital and What Does It Include?
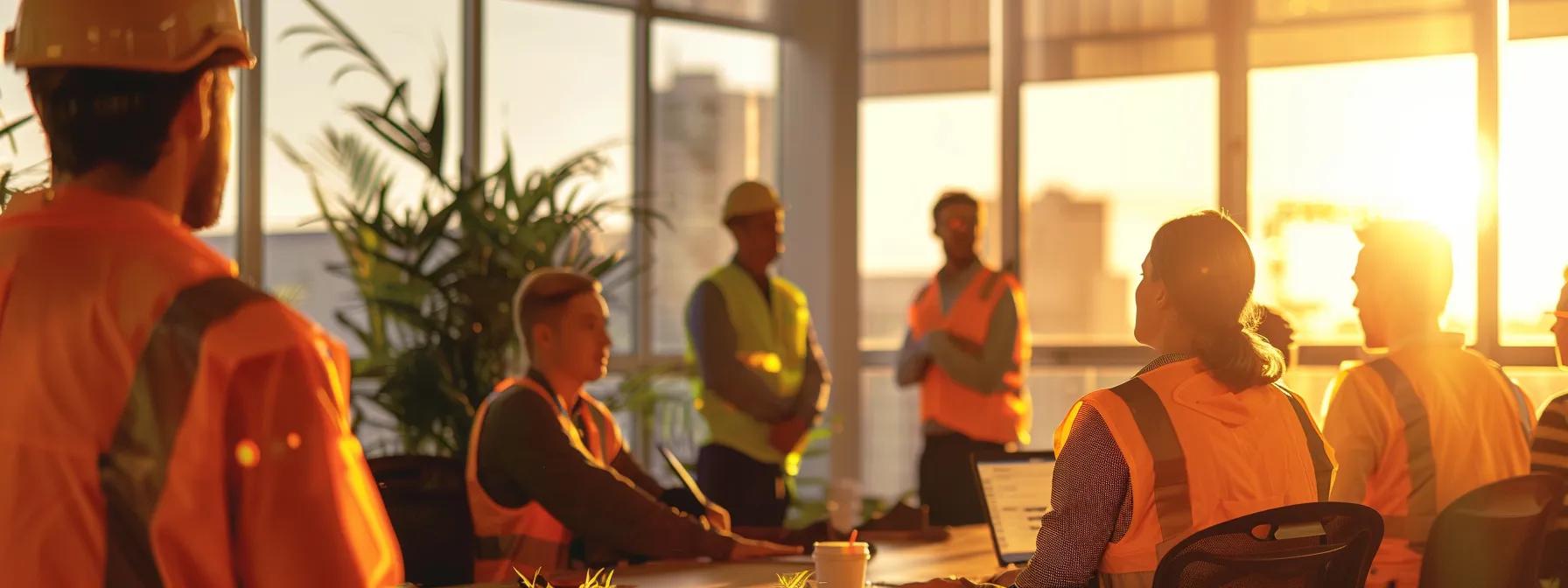
Training is indispensable for ensuring workers know how to properly use fall protection equipment, recognize hazards, and respond in emergencies. Comprehensive training fosters a safety culture and minimizes accident risks.
What Is Competent Person Training and Who Needs It?
Competent person training is provided to employees responsible for: – Identifying fall hazards – Conducting risk assessments – Implementing safety measures
Typically, safety managers, supervisors, or maintenance personnel receive this training, which covers hazard recognition, equipment application, and recordkeeping protocols.
How Does Authorized Person Training Differ?
Authorized person training is for individuals designated to: – Supervise and conduct rescue operations – Use rescue equipment effectively – Coordinate emergency responses
This specialized training ensures rapid and effective response when a fall occurs.
What Are the Key Elements of Fall Rescue Training?
Fall rescue training includes: – Rescue Plans: Step-by-step procedures for different scenarios. – Equipment Operation: Training on lifelines, winches, and rescue devices. – Emergency Communication: Clear protocols for alerting rescue teams. – Drills and Simulations: Practical exercises to reinforce learning. – Hazard-Specific Procedures: Tailoring approaches to specific industrial settings.
These elements help ensure that injured workers are rescued safely with minimal delay.
How Can Training Programs Be Developed and Evaluated?
Effective training programs should: – Assess the specific needs of the workforce. – Set clear learning objectives. – Combine theoretical and practical modules. – Use feedback surveys, performance metrics, and drills for continuous evaluation. – Include periodic certification and recertification to ensure ongoing competency.
How Do OSHA Regulations Impact Fall Risk Management Programs?
OSHA regulations significantly influence fall risk management programs by establishing mandatory safety standards. Compliance not only avoids penalties but also reinforces a company’s commitment to safety and operational excellence.
What Are the Main OSHA Fall Protection Standards (Subpart M)?
Key elements of OSHA’s standards include: – Guardrails, Safety Nets, and Fall Arrest Systems: Requirements for when and how these must be installed. – Training and Certification: Mandatory courses for workers and supervisors. – Equipment Specifications: Detailed standards for harnesses, lanyards, and lifelines. – Maintenance and Inspection: Regular checks and proper documentation.
These guidelines provide a legal framework to prevent fall-related injuries.
How Should Recordkeeping and Inspections Be Managed?
Effective practices include: – Detailed Documentation: Keeping records of safety inspections, equipment maintenance, and training. – Scheduled Audits: Periodic internal reviews to identify risks. – Digital Data Management: Systems to track inspection dates and remedial actions. – Employee Involvement: Encouraging workers to report hazards.
Proper management of records and inspections supports proactive risk management and ensures compliance with OSHA.
What Are Common OSHA Citations Related to Fall Protection?
Common citations involve: – Inadequate fall protection systems (e.g., missing guardrails). – Insufficient or undocumented training. – Poor recordkeeping of inspections. – Failure to repair or replace faulty equipment.
Awareness of these issues helps managers focus on critical areas to prevent violations.
How Can Fall Rescue Planning Enhance Industrial Safety Programs?
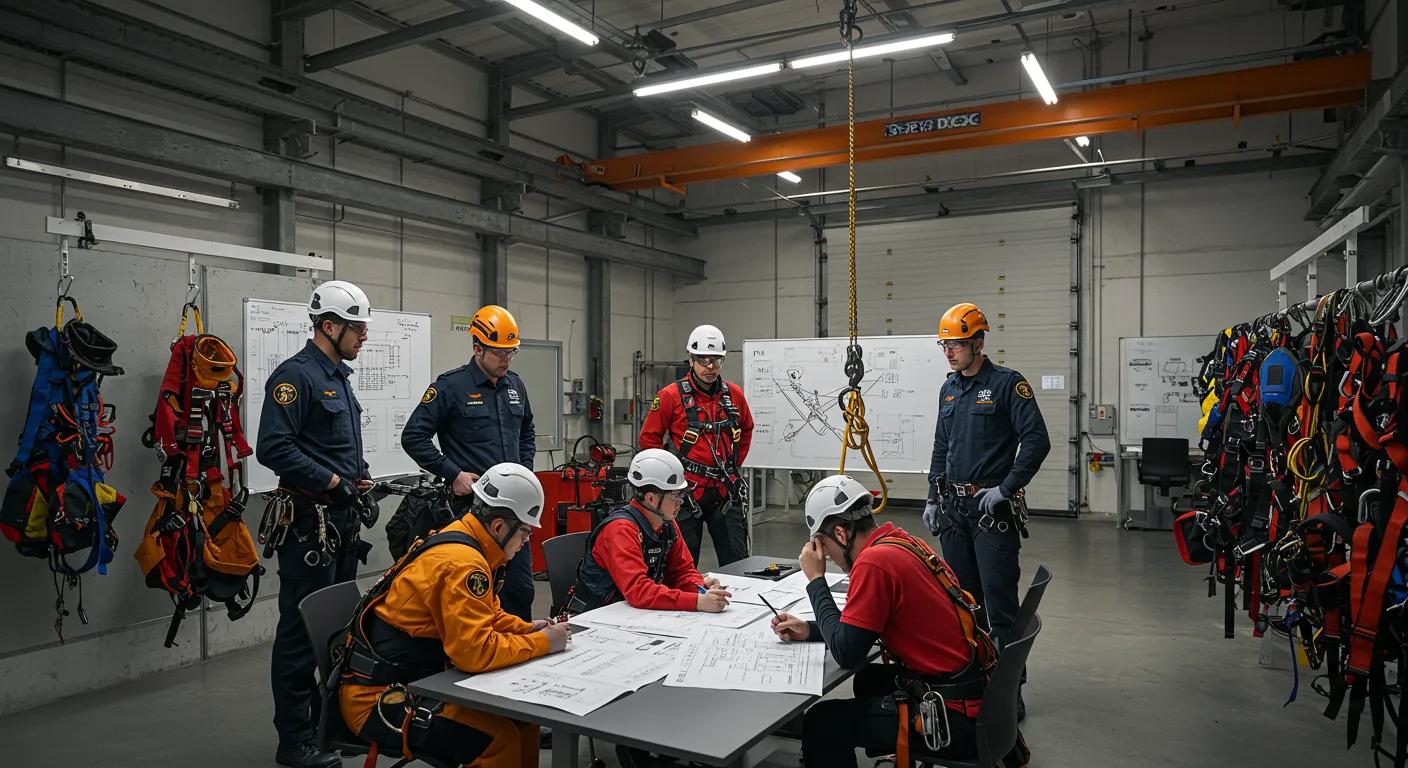
Fall rescue planning is crucial for ensuring prompt and effective aid during fall incidents. A comprehensive rescue plan includes proper equipment, training, and clear emergency procedures to facilitate safe extraction of injured workers.
Why Is Fall Rescue Planning Important?
Timely rescue operations: – Reduce injury severity. – Prevent fatalities. – Ensure that rescue teams are well-prepared and roles are clearly defined.
Regular drills and scenario simulations help identify and address gaps in rescue strategies.
What Equipment Is Required for Effective Fall Rescue?
Essential equipment includes: – Rescue Harnesses and Lanyards: For secure and quick connection. – Lifelines and Anchor Systems: To support rapid extraction. – Rescue Kits: Containing necessary tools like rope and carabiners. – Communication Devices: To maintain contact with rescue teams. – Powered Rescue Equipment: Such as winches in high-risk settings.
Routine inspection and maintenance are critical to ensure this equipment functions reliably.
What Are Standard Fall Rescue Procedures and Emergency Responses?
A typical fall rescue procedure involves: 1. Initial Assessment: Confirm the status and location of the fallen worker. 2. Communication: Alert rescue teams using clear protocols. 3. Stabilization: Secure the area to prevent additional hazards. 4. Rescue Operation: Use specialized equipment to safely retrieve the worker. 5. Post-Rescue Assessment: Provide immediate medical attention and evaluate the operation.
How Do You Develop and Implement a Fall Rescue Plan?
Developing a rescue plan involves: – Risk Identification: Determining high-risk areas and potential rescue scenarios. – Resource Allocation: Assigning necessary equipment and roles. – Plan Development: Documenting procedures, communication protocols, and responsibilities. – Training and Drills: Regularly practicing rescue operations. – Plan Evaluation: Revising the plan based on drill feedback and actual incidents.
A dynamic rescue plan is continuously refined to address evolving risks.
How Do You Develop, Implement, and Manage a Successful Fall Prevention Program?
A successful fall prevention program requires meticulous planning, implementation, and ongoing management, balancing hazard recognition, worker training, and engineering controls with continuous improvements.
What Are the Steps to Develop a Fall Prevention Program?
Key steps include: – Initial Hazard Assessment: Conduct a comprehensive audit to identify risks. – Set Clear Objectives: Define specific safety goals and key performance indicators. – Policy Formulation: Develop safety protocols and operational guidelines. – Resource Allocation: Invest in fall protection systems and training initiatives. – Integration: Align the program with existing safety and quality management systems.
These steps create a framework for a sustainable safety culture.
How Is Program Implementation Best Executed?
Effective implementation involves: – Employee Engagement: Involve workers through training sessions and feedback loops. – Phased Rollout: Start in high-risk areas and gradually expand. – Provision of Equipment: Ensure proper installation and availability of safety gear. – Regular Training: Conduct refresher courses to stay updated with best practices. – Documentation: Maintain records of audits, training, and incidents for continuous monitoring.
A coordinated effort across departments is essential to foster a culture that supports the program.
What Are Effective Methods for Program Management and Continuous Improvement?
Continuous improvement is achieved by: – Data Collection and Analysis: Use digital tools to monitor safety data. – Performance Reviews: Evaluate the program against safety metrics and KPIs. – Employee Feedback: Use forums and suggestion boxes for insights. – Benchmarking: Compare performance with industry standards. – Corrective Actions: Address deviations quickly via established procedures.
These strategies ensure that the program remains dynamic and effective.
How Do You Evaluate Program Effectiveness and Outcomes?
Evaluation should involve: – Quantitative Metrics: Track incident rates, near-misses, and corrective action completions. – Qualitative Feedback: Gather worker satisfaction data through surveys. – Regular Audits: Conduct internal and external audits to gauge compliance. – Trend Analysis: Monitor declining trends in fall incidents. – Return on Investment: Assess reductions in downtime, litigation costs, and improved safety indicators.
A systematic evaluation identifies successes and areas for further improvement.
Table: Fall Protection Equipment Comparison
Before finalizing program development, consider this summary:
Equipment Type | Key Function | Primary Benefit | Regulatory Compliance |
---|---|---|---|
Full-Body Harness | Arrests a fall and distributes impact | Reduces injury risk by 80% | OSHA, ANSI compliant |
Lanyard with Energy Absorber | Minimizes force during a fall | Decreases deceleration forces | OSHA standards |
Guardrails | Prevents access to fall hazards | Eliminates exposure to unprotected edges | OSHA requirements |
Fall Restraint Lanyard | Restricts movement to prevent falls | Proactive hazard prevention | ANSI certified |
Lifelines and Anchors | Provides stable attachment for rescue | Ensures secure rescue operations | OSHA, NFPA compliant |
This comparison helps managers make informed equipment decisions, reinforcing a culture of safety.
Frequently Asked Questions
Q: How often should fall risk assessments be conducted in industrial settings?
A: They should be performed quarterly and after any significant changes to the environment.
Q: What role does employee feedback play in a fall prevention program?
A: It helps identify overlooked hazards and evaluate the effectiveness of safety measures, leading to continuous improvement.
Q: Can fall protection equipment be shared among workers?
A: Some equipment can be shared; however, personal protective items like harnesses should be individually assigned and regularly inspected.
Q: How are OSHA citations typically resolved in fall protection-related cases?
A: Through immediate corrective action, retraining employees, and maintaining comprehensive documentation.
Q: Is specialized training required for all employees regarding fall protection?
A: Yes, employees working at heights or in hazardous environments need role-specific training, and supervisory staff must receive advanced hazard and rescue training.
Q: What are the most significant benefits of implementing a fall prevention program?
A: Such programs significantly reduce injuries, lower insurance costs, boost productivity, and enhance overall worker morale.
Final Thoughts
Developing effective fall risk management and prevention programs is essential for keeping industrial workplaces safe and compliant with regulatory standards. By identifying hazards, selecting the appropriate equipment, and providing thorough training, organizations can protect workers and reduce fall-related incidents. Continuous monitoring, data-driven evaluations, and a proactive approach lead to steady improvements in safety. In today’s evolving industrial environment, dynamic fall protection programs are crucial for long-term success and worker wellbeing.