Fall Risk Management and OSHA Compliance: How to Build a Safer Workplace From the Ground Up
This article explores effective workplace fall prevention, OSHA safety standards, and strategies to create a proactive safety culture. It explains key components such as risk assessments, customized protection plans, and essential fall protection equipment—including ladder systems and guardrail systems—which are critical elements for proper design-installation and ensuring annual maintenance. All of these are supported by industry regulations and practical real-world examples. The content is organized under clear headings to help businesses evaluate, design, and maintain comprehensive fall risk management efforts.
What Are the Key Components of Effective Workplace Fall Prevention?
Effective fall prevention, provided by us fall protection, relies on hazard identification, risk assessment, equipment selection (including ladder systems and guardrail systems), and continuous support. Key components include thorough fall risk assessments, tailored protection plans, proper fall protection equipment, and ongoing training, audits, and annual maintenance. Together, these measures reduce accidents and improve overall safety culture.
How Do Fall Risk Assessments Identify Workplace Hazards?
Fall risk assessments identify hazards by observing work processes and evaluating environmental risk factors, including those affecting ladder systems. Using checklists, walk-through surveys, and evaluation tools, assessments detect issues like unguarded edges, slippery surfaces, or poor lighting, as well as compromised guardrail systems. By assigning likelihood and severity ratings, these assessments guide targeted corrective actions and recommend annual maintenance procedures.
What Customized Fall Protection Plans Best Address Site-Specific Risks?
Customized plans are developed after identifying unique hazards at each site, reflecting the specialization of industries-we-serve. They consider industry practices, building layouts, and workforce activities. Integrating engineering controls (e.g., guardrail systems), administrative measures (e.g., regular inspections), and personal protective equipment, including us fall protection, ensures that plans remain dynamic and effective as conditions change. Regular annual maintenance further supports long-term operational safety.
Which Fall Protection Equipment Is Essential for OSHA Compliance?
OSHA mandates equipment such as harnesses, lanyards, guardrails (guardrail systems), safety nets, and personal fall arrest systems. A full-body harness with a self-retracting lifeline (lifeline-systems), for instance, is crucial for safe deceleration during a fall. Additional devices like warning line systems or edge protection barriers, along with comprehensive design-installation and annual maintenance programs, are essential when conventional PPE is insufficient.
How Does Ongoing Support and Audits Maintain Fall Safety Standards?
Regular safety audits, refresher training, and continuous monitoring – including annual maintenance checks – ensure that fall prevention strategies remain effective. Periodic audits evaluate adherence to protocols and review ladder systems performance to highlight gaps, while ongoing training keeps employees current with equipment maintenance for lifeline-systems and overall safety practices. This continuous oversight is vital to prompt corrective action.
How Can Businesses Ensure Full OSHA Safety Standards Compliance for Fall Protection?
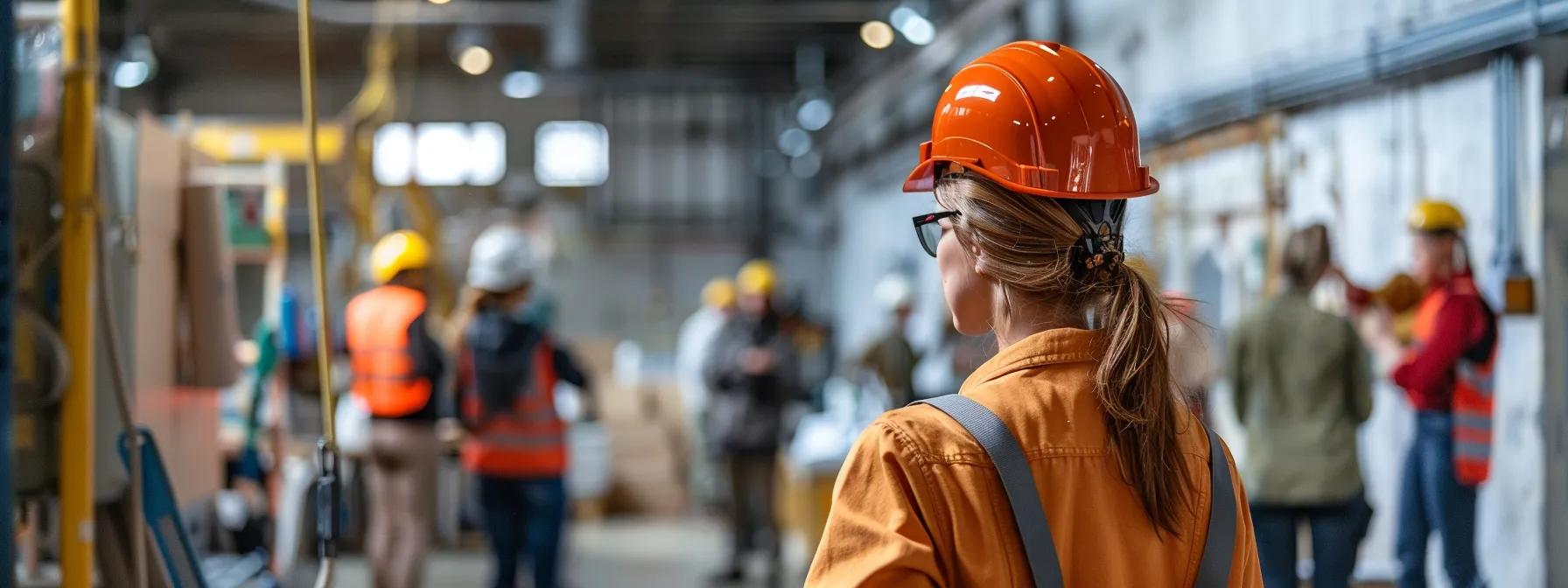
Businesses maintain OSHA compliance by staying current with regulations, conducting periodic training, and keeping proper documentation, including routine annual maintenance. Understanding updated OSHA guidelines and systematically implementing and auditing fall protection measures—such as us fall protection strategies and guardrail systems—helps meet prescribed standards and reinforces essential lifeline-systems.
What Are the Latest OSHA Regulations on Fall Risk Management?
Recent OSHA regulations call for comprehensive prevention programs that include training on industries-we-serve, risk assessments, and detailed incident prevention documentation. They demand improved hazard communication, stricter enforcement of PPE protocols (including us fall protection measures), and the use of technologies such as digital reporting systems to track safety data in real time, along with provisions for annual maintenance of safety systems.
How Does OSHA Compliance Training Improve Employee Safety?
Compliance training equips workers with the knowledge to identify hazards, use protective equipment correctly such as ladder systems, and respond in emergencies. Training covers equipment usage, safety guidelines (including guardrail systems), hazard recognition, and emergency response procedures. A well-informed workforce significantly reduces the likelihood of falls and associated injuries while supporting annual maintenance practices and effective us fall protection measures.
What Documentation Is Required to Demonstrate OSHA Compliance?
Essential documents include records of fall risk assessments, detailed protection plans, training logs, equipment maintenance reports updated with annual maintenance procedures, and audit findings. These records support regulatory inspections and help refine safety protocols by highlighting recurring issues and the effectiveness of corrective measures observed in guardrail systems and ladder systems. Regular evaluations of lifeline-systems further enhance overall workplace safety.
Why Is Building a Proactive Safety Culture Crucial for Fall Risk Management?
A proactive safety culture minimizes risks by embedding safety as a key organizational value. In many industries-we-serve settings, a rigorous design-installation approach for us fall protection ensures that ladder systems are properly implemented. It encourages leadership to support safety initiatives and makes every employee responsible for maintaining safe practices through regular annual maintenance checks. Early hazard identification and open communication about risks ultimately reduce injuries and costs.
How Can Leadership Promote a Culture of Fall Prevention?
Leaders set clear safety expectations, model safe behavior, and provide necessary resources such as ladder systems, guardrail systems, and lifeline-systems. By regularly communicating safety priorities, sponsoring annual maintenance training sessions, and actively participating in risk assessments, leaders build trust and motivate team members to prioritize safety.
What Are Best Practices for Employee Engagement in Safety Programs?
Effective engagement strategies include regular safety meetings, interactive training sessions, incentive programs for hazard reporting, and easy communication channels for sharing safety observations. Integrating ladder systems and guardrail systems into daily operations enhances us fall protection measures. Involving employees in planning and using real-life case studies reinforces the importance of proactive measures and increases vigilance.
How Does a Safety Culture Reduce Workplace Injuries and Costs?
When safety protocols, such as us fall protection measures incorporating ladder systems and guardrail systems, are an everyday part of operations, the frequency and severity of falls decrease. Fewer injuries translate into lower medical costs, less downtime, and reduced insurance premiums. Organizations that also commit to annual maintenance and integrate a robust safety culture have been shown to reduce incident-related costs by up to 30% over time.
What Are the Most Effective Strategies for Conducting Fall Risk Assessments?
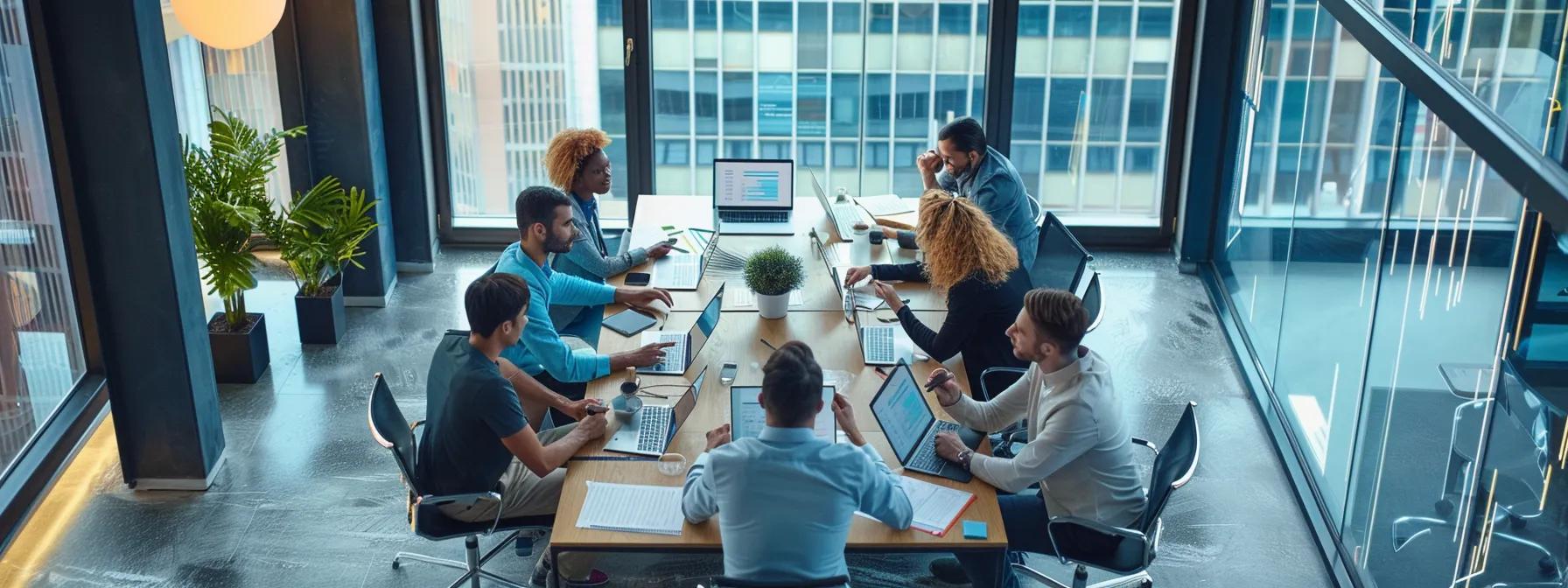
Effective assessments combine direct observation, quantitative measurements, and employee input to deliver a precise evaluation of hazards, including key considerations for us fall protection and ladder systems. A systematic approach ensures that risks, such as those associated with guardrail systems, are identified, prioritized, and managed based on their potential impact.
How to Identify Common Fall Hazards in Different Work Environments?
Typical hazards include unguarded edges, wet or uneven surfaces, poor lighting, and structural deficiencies, underscoring the importance of annual maintenance. In industrial settings, industries-we-serve have often observed that an elevated platform without proper guardrails—or guardrail systems—poses a major risk, while in office environments, cluttered pathways and slippery floors can be problematic. Tailored checklists help ensure every hazard is flagged and categorized appropriately, reinforcing effective us fall protection measures.
What Tools and Techniques Support Accurate Risk Evaluations?
Both traditional inspection methods and modern technologies support risk evaluations, particularly in annual maintenance scenarios. Techniques such as thermal imaging, laser scanning, and sensor-based monitoring, along with digital checklists and mobile audit applications, enhance accuracy and streamline documentation of risks. Incorporating guardrail systems evaluations and lifeline-systems inspections further ensures comprehensive safety and compliance.
How to Prioritize Risks for Targeted Fall Prevention Measures?
A risk matrix that scores hazards based on likelihood and potential severity is commonly used in design-installation projects. High-risk hazards, marked by both high occurrence probability and significant consequences, are addressed with immediate engineering controls such as guardrail systems, while lower-priority risks may be managed through administrative controls and enhanced monitoring. Additionally, annual maintenance of ladder systems and lifeline-systems is recommended to ensure long-term safety and reliability.
How Do Customized Fall Protection Plans Improve Workplace Safety?
Tailored fall protection plans enhance safety by addressing unique site conditions and integrating input from risk assessments. At us fall protection, these plans are supported by a comprehensive design-installation approach and a commitment to annual maintenance, ensuring that key equipment like guardrail systems and lifeline-systems are effectively implemented. These measures bridge the gap between standard regulations and the practical challenges of varied work environments, ensuring both equipment use and emergency procedures are clearly outlined.
What Factors Influence the Design of Site-Specific Fall Protection Plans?
Important factors include the physical layout, nature of work, environmental conditions, and specific vulnerabilities of the workforce. For example, ladder systems play a vital role in managing work at elevated heights, while guardrail systems are essential for preventing falls in areas with frequent level changes. Considerations such as the height of work areas, frequency of level changes, and construction materials, along with lifeline-systems integrated through design-installation practices, are critical. Incorporating historical incident data, annual maintenance reviews, and employee feedback also ensures plans remain both compliant and effective.
How to Integrate Equipment and Training Into Protection Plans?
Effective integration involves selecting the right fall protection equipment—like harnesses, lanyards, ladder systems, and guardrail systems—and linking their use to comprehensive training programs. Hands-on training, annual maintenance protocols, simulation drills, and refresher courses ensure that both the equipment and the practices remain effective and integrate seamlessly with us fall protection standards.
How Are Plans Updated to Reflect Changing Workplace Conditions?
Fall protection plans are living documents that benefit from a robust design-installation approach. They must be reviewed regularly and updated following operational changes, building modifications, or new audit findings. Regular annual maintenance ensures that the plans incorporate current hazards and best practices, while annual reviews or updates after significant changes offer an opportunity to get-a-free-quote for future improvements.
What Types of Fall Protection Equipment Are Required for OSHA Compliance?
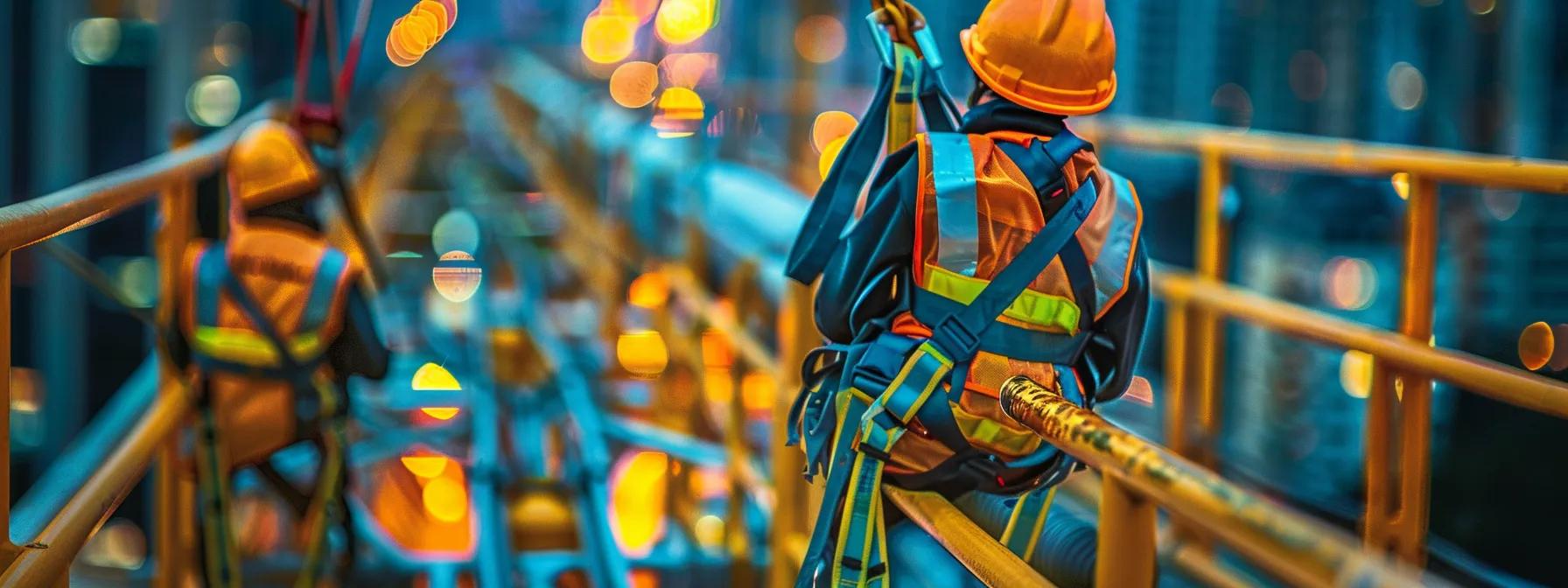
OSHA requires employers to install and maintain a range of fall protection equipment, often provided through design-installation and annual maintenance services from experts in us fall protection. This includes personal protective gear such as full-body harnesses, lanyards, self-retracting lifelines (lifeline-systems), guardrails (guardrail systems), safety nets, warning lines, and fall arrest systems. Each piece is designed for specific risk scenarios, addressing the needs of industries-we-serve, and must conform to strict standards.
How Do Harnesses, Lanyards, and Guardrails Prevent Falls?
A full-body harness helps distribute the force of a fall, while lanyards secure the harness to an anchorage point. Additionally, lifeline-systems provide extra security during dynamic movements, and guardrail systems serve as physical barriers to prevent falls from elevated areas. Together, these elements form a multi-tiered defense system that meets OSHA’s performance standards, reinforcing our commitment at us fall protection.
When Should Safety Nets and Other Devices Be Used?
Safety nets and shock-absorbing lanyards serve as backups when guardrail systems are impractical or insufficient, such as in large construction sites or areas with limited anchorage. At these sites, industries-we-serve standards often emphasize design-installation practices to ensure maximum safety. Warning line systems and lifeline-systems are used in temporary worksites or active maintenance areas, chosen based on site configuration, annual maintenance schedules, and fall distance.
How to Ensure Proper Installation and Maintenance of Equipment?
Proper design-installation follows manufacturer guidelines and requires periodic inspections. Documentation of inspections and timely repairs or replacements as part of annual maintenance are crucial. Certified safety professionals should oversee installations, ensuring that systems such as guardrail systems are implemented effectively while staff receive regular maintenance training to ensure continuous compliance.
How Can Ongoing Training and Audits Sustain Fall Risk Management Efforts?
Continuous training and audits reinforce best practices and ensure that fall prevention measures remain effective. Integrating a design-installation approach, regular training sessions help workers adopt safe practices when using ladder systems and guardrail systems, while systematic audits and annual maintenance verify that equipment and processes are in proper working order. This integrated approach adapts strategies to evolving risks and technological advancements.
What Topics Should OSHA Fall Protection Training Cover?
Training should cover hazard recognition, correct usage of fall arrest systems and lifeline-systems, emergency procedures, and methods to conduct risk assessments with considerations for industries-we-serve. It should include demonstrations of protective equipment—highlighting ladder systems and guardrail systems—guidelines for record keeping, and protocols for annual maintenance in reporting near-miss incidents to prevent future occurrences.
How Often Should Workplace Fall Safety Audits Be Conducted?
Audits should be conducted at least annually as part of routine annual maintenance, with additional checks after major operational changes or incidents. In high-risk environments—where ladder systems, guardrail systems, and lifeline-systems are critical—quarterly audits may also include design-installation reviews to ensure all safety measures are up to standard. For more detailed information or to secure a get-a-free-quote, additional resources are available on our blog.
What Are Common Findings and How to Address Them?
Common audit issues include worn equipment, improper harness usage impacting us fall protection standards, missing guardrails—often a result of neglected guardrail systems—and incomplete documentation. Immediate corrective actions such as equipment replacement, additional training, updated records, or routine annual maintenance are essential. Continuous improvement systems incorporating proper design-installation processes and scheduled refreshers help prevent recurring issues.
Frequently Asked Questions
Q: How often should fall risk assessments be updated in a changing work environment?
A: They should be updated annually (as part of our annual maintenance) or whenever significant changes occur, such as modifications in structure or new equipment installations under our design-installation process. For additional details, please refer to us fall protection.
Q: What are the consequences of failing to comply with OSHA fall protection regulations?
A: Noncompliance can lead to fines, increased insurance premiums, legal liabilities, and a higher risk of workplace injuries and fatalities. This is especially critical when proper measures—such as ensuring the correct design-installation and regular annual maintenance of ladder systems, guardrail systems, and lifeline-systems—are not followed. Moreover, many companies seek expert guidance from us fall protection specialists to mitigate these risks.
Q: Can fall protection training be delivered online, or must it be in-person?
A: While some theoretical components, such as those related to lifeline-systems and us fall protection, can be managed online, practical, hands-on demonstrations are typically required to ensure proper equipment use. In these sessions, emphasis is not only placed on safe operation but also on the design-installation and annual maintenance of ladder systems to immediately correct unsafe practices.
Q: How do small businesses manage compliance costs for fall protection measures?
A: Cost management strategies include selecting essential equipment (such as ladder systems, guardrail systems, and lifeline-systems) based on detailed risk assessments and scheduling regular annual maintenance. Many organizations also align these practices with us fall protection guidelines by using group training sessions or shared resources and employing cost-effective technologies for audits.
Q: What role does employee feedback play in improving fall prevention strategies?
A: Employee feedback reveals practical issues with equipment (for example, ladder systems) or procedures and should be used to update training, audits, annual maintenance protocols, and overall preventive measures that incorporate guardrail systems best practices.
Q: Are there technological advancements that help monitor fall risks in real time?
A: Yes, sensor-based monitoring, wearable devices, and real-time data platforms provided by us fall protection—with integrated design-installation support and annual maintenance protocols—can track hazardous conditions and send alerts for quicker responses.
Final Thoughts
Effective fall risk management and OSHA compliance depend on a continuously updated safety program that includes thorough risk assessments, customized protection plans, design-installation services, and proper maintenance of fall protection equipment (including annual maintenance, guardrail systems, and lifeline-systems). Businesses that promote a proactive safety culture through leadership engagement, regular training, and systematic audits reduce workplace injuries and associated costs. By integrating advanced technologies, rigorous documentation, and employee involvement, organizations not only meet OSHA standards but also create a safer and more productive work environment. Viewing safety as a continuous investment helps companies adapt to evolving conditions while setting industry benchmarks for innovation and proactive risk management. For more insights, visit our about-us page, explore industries-we-serve details, or get-a-free-quote via our blog.