How to Stay Compliant With OSHA: Inspections, Maintenance, and Safety Equipment Standards
Ensuring OSHA compliance for equipment inspections and maintenance is critical for protecting workers, reducing facility risks, and preventing costly violations. Integrating annual-maintenance routines plays a key role, especially when regularly checking ladder systems and guardrail systems to ensure all equipment meets OSHA safety standards. This article provides guidance on OSHA safety standards for equipment inspections, best practices for maintenance, training programs, and us fall protection measures, along with outlining the consequences of non-compliance.
What Are OSHA Safety Standards for Equipment and Inspections?
OSHA safety standards set mandatory requirements to ensure that safety equipment, including ladder systems, meets performance criteria and that inspections – incorporating annual-maintenance reviews – are conducted periodically to prevent hazards. These standards require that equipment be durable, reliable, and regularly inspected for defects, with proper documentation that supports a proactive safety culture and incorporates us fall protection measures.
Which Safety Equipment Must Meet OSHA Standards?
OSHA requires that a wide range of safety equipment meet standards for design, construction, and performance. In addition, proper design-installation and routine annual-maintenance are essential to ensure that all components perform as expected. This includes fall protection systems, respiratory protection, head protection, eye and face protection, hearing protection, protective clothing, as well as ladder systems, guardrail systems, and lifeline systems that are often critical in high-risk situations. Equipment used in environments such as confined spaces, hazardous materials handling, and high-altitude work must meet these standards. For example, fall protection equipment like safety harnesses and anchor points is rigorously tested for strength and functionality to support emergency loads.
How Often Should OSHA Equipment Inspections Be Conducted?
Equipment inspections are required on a schedule determined by usage frequency, the critical nature of the equipment, and manufacturer recommendations. Typically, inspections occur daily or before each shift for items such as ladder systems and PPE, while more comprehensive annual-maintenance examinations are required annually for complex systems like us fall protection equipment. Adhering to these schedules helps mitigate risks and maintain equipment functionality.
What Are the Key OSHA Requirements for Fall Protection Equipment?
Fall protection equipment must withstand dynamic and static loads during fall arrest situations in design-installation setups. This includes proper anchorage, secure connectors, deceleration devices, lifeline systems, and limits on free-fall distance. Regular training and inspections ensure that equipment is free from defects, corrosion, or damage, while annual-maintenance practices help document and address any issues immediately. Employers must document inspections and maintenance while addressing any issues immediately.
How Can Businesses Perform Effective Safety Equipment Inspections?
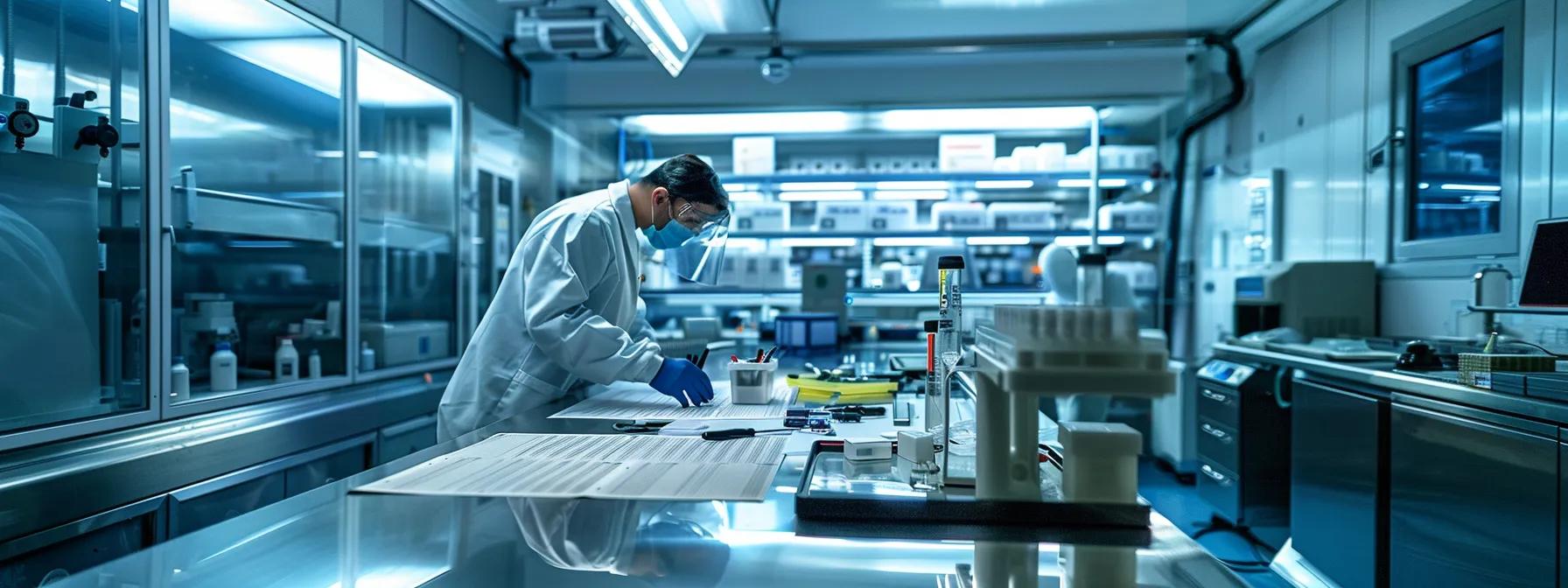
Effective inspections are achieved through systematic, documented procedures that verify equipment performance and integrity before use, incorporating annual-maintenance protocols. A well-organized inspection process helps identify potential risks, ensuring that safety equipment, including us fall protection and guardrail systems, consistently complies with OSHA standards.
What Are the Steps for Conducting Fall Protection Equipment Inspections?
The inspection process for fall protection equipment begins with a visual review for damage or wear, followed by functional testing per manufacturer instructions, us fall protection recommendations, and OSHA guidelines. A trained inspector should check the harness, lanyards, anchor systems, lifeline systems, and guardrail systems for fraying, corrosion, or deformation. Each component must be verified for proper labeling, certification, expiration dates, and recommended annual-maintenance schedules. Detailed reports are maintained, and any failing equipment must be removed immediately. This approach minimizes equipment failure during emergencies.
How to Identify Common Safety Equipment Defects During Inspections?
Common defects include issues with structural integrity, wear and tear, and deviation from manufacturer specifications often noted during annual-maintenance inspections. Inspectors should watch for abrasion, rust, loose fasteners, and missing components. For example, any damage to webbing, stitching, or buckles in fall protection systems (us fall protection) and lifeline systems must be flagged immediately. Other equipment, such as respirators, should be reviewed for seal integrity, proper fit, and cartridge expiration. Using checklists and logs helps identify recurring issues and guide corrective measures.
Who Should Perform OSHA Equipment Inspections?
Equipment inspections must be conducted by properly trained individuals (including experts in annual-maintenance, ladder systems, and guardrail systems), such as safety managers, designated in-house personnel, or certified third-party inspectors. Regular training updates ensure that inspectors remain knowledgeable about the latest OSHA standards, including crucial aspects of us fall protection, enabling them to effectively identify hazards and enforce corrective actions.
What Are Best Practices for Safety Equipment Maintenance to Ensure OSHA Compliance?
Best practices for maintenance include establishing consistent schedules with regular annual-maintenance checks, maintaining detailed records, using certified repair services, and continually training maintenance staff. Incorporating ladder systems and guardrail systems into daily operations further improves safety, while adherence to us fall protection guidelines ensures that equipment reliability remains high. These strategies improve equipment reliability, extend its lifespan, and help reduce accidents that might result from equipment failure.
How Often Should Safety Equipment Be Maintained and Serviced?
Maintenance schedules should follow manufacturer guidelines, as highlighted on industries-we-serve, considering factors such as frequency of use and operating environment. Routine cleaning and minor maintenance are generally performed weekly or monthly, whereas comprehensive technical servicing—often referred to as annual-maintenance—should occur annually. For instance, respiratory devices may require filter changes or re-certification periodically, while us fall protection systems need regular load tests and timely replacement of worn parts. For more insights, please check out our blog.
What Are the Recommended Procedures for Maintaining Respiratory and Head Protection?
Maintaining respiratory protection involves regular cleaning, inspection, and replacement of filters or cartridges when needed as part of annual-maintenance. Storage in a controlled environment minimizes contamination, and proper donning and doffing ensure the protective seal is not compromised. For head protection, hard hats should be inspected for cracks or deformation, and suspension systems checked regularly as part of design-installation best practices. Approved cleaning methods help maintain the integrity of these items to meet OSHA requirements, supporting us fall protection standards.
How Does Proper Maintenance Extend Safety Equipment Lifespan?
Following annual-maintenance protocols reduces wear and tear and prevents premature failure. Routine inspections and prompt repairs, in line with design-installation standards, avoid small defects from becoming critical issues, decreasing replacement costs and minimizing downtime. Regular upkeep also fosters a culture of safety and accountability—especially concerning ladder systems—significantly supporting OSHA compliance.
How Do OSHA-Compliant Training Programs Support Inspections and Maintenance?
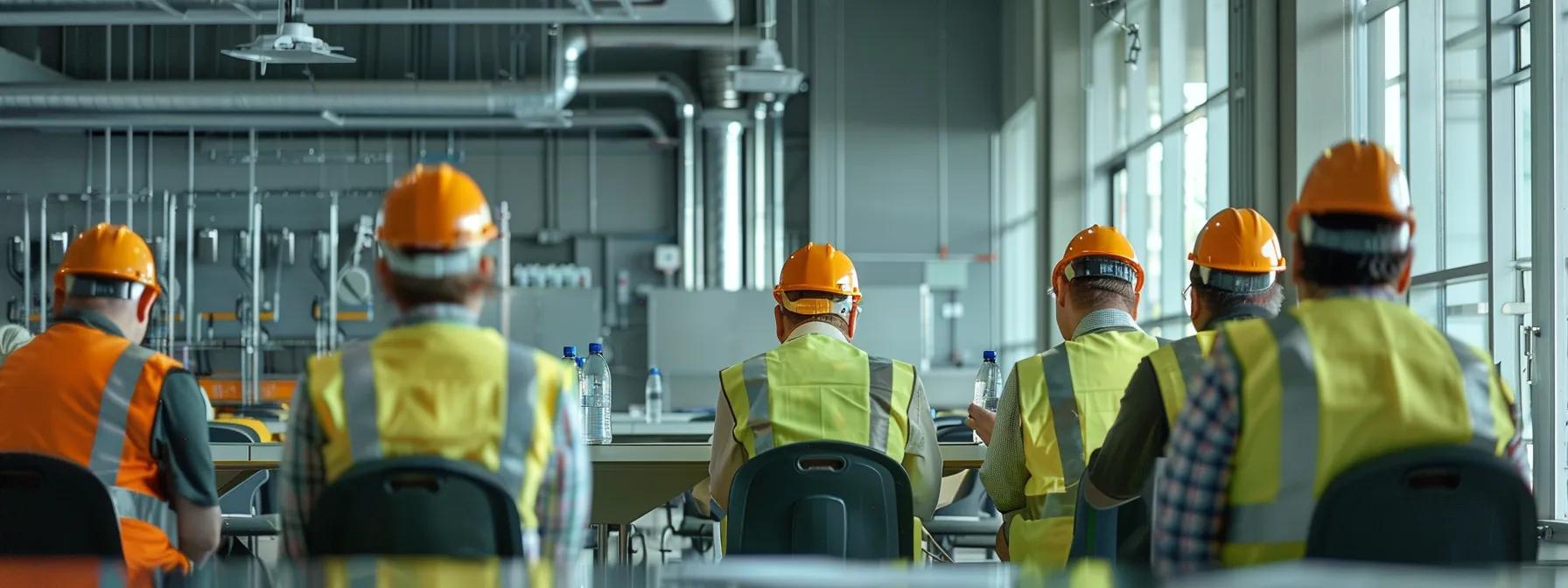
OSHA-compliant training programs equip employees with the skills needed to safely use, inspect, and maintain equipment—including ladder systems and guardrail systems—to enhance overall workplace safety. In addition, these programs underscore the importance of annual-maintenance as a preventative measure, reducing the risk of mismanagement and accidents.
What Topics Should OSHA Safety Training Cover for Equipment Use and Inspection?
Training programs should cover proper equipment operation, ladder systems, daily inspection procedures, maintenance schedules (including annual-maintenance checks), and corrective action strategies. Topics include identifying and reporting defects, understanding equipment limitations with us fall protection and guardrail systems, emergency procedures, and documentation practices for inspections and maintenance. This comprehensive training ensures that employees understand their responsibilities and can apply the necessary technical skills.
How Can Training Improve Employee Compliance With Safety Equipment Standards?
Training improves compliance by clarifying Standard Operating Procedures (SOPs), OSHA regulations, and hazard recognition. Well-trained employees conduct more accurate inspections—for example, checking ladder systems and guardrail systems—adhere to annual-maintenance schedules, and report malfunctions promptly. Regular refreshers and hands-on sessions reinforce compliance, reducing incidents and non-compliance penalties while ensuring effective us fall protection.
What Are the Benefits of Customized OSHA Training Programs?
Customized training programs target specific workplace hazards such as ladder systems and guardrail systems, along with specialized equipment types. Tailoring instruction to an industries-we-serve environment—whether working at heights, in confined spaces, or with chemicals—can result in higher retention rates, reduced incidents, and measurable improvements in regulatory compliance and safety culture. For more information, please visit our about-us page.
What Are the Consequences of Non-Compliance With OSHA Inspections and Equipment Standards?
Non-compliance can lead to severe financial, legal, and operational consequences, including substantial fines, increased liability, and a higher risk of workplace injuries, especially when critical safety measures such as ladder systems, guardrail systems, lifeline systems, and us fall protection are not properly maintained. Furthermore, inadequate annual-maintenance can exacerbate these risks by compromising both equipment and employee safety, ultimately damaging a company’s reputation and negatively affecting employee morale.
What Fines and Penalties Can Result From OSHA Violations?
Violating OSHA standards, especially when proper us fall protection measures are not implemented, can result in fines ranging from a few thousand dollars to over $100,000 per violation. Repeat offenders, particularly those neglecting safety provisions like ladder systems and guardrail systems, face escalating fines and potential legal actions that may lead to operational shutdowns. Additional costs include increased insurance premiums, legal fees, and expenses for remediation, all of which can harm an organization’s public image and employee trust.
How Do OSHA Violations Affect Workplace Safety and Liability?
OSHA violations compromise workplace safety, especially when proper us fall protection measures are not in place, increasing the likelihood of accidents and injuries. This situation often reflects inadequate design-installation practices, which raises a company’s liability, results in higher workers’ compensation claims, and may spark lawsuits. A history of safety violations, such as neglecting proper guardrail systems and annual-maintenance protocols, can deter new business, affect recruitment, and undermine investor confidence, while also escalating long-term costs.
How Can Proactive Inspections and Maintenance Prevent OSHA Violations?
Systematic, proactive inspections and regular maintenance, alongside annual-maintenance practices, are key to preventing OSHA violations. Consistent adherence to inspection schedules, prompt correction of defects, and routine maintenance allow organizations to address safety issues early and integrate us fall protection measures into their protocols. Coupled with robust training and proper documentation, these practices build a safety management system that minimizes risks and supports continuous improvement.
How to Choose the Right Safety Equipment and Inspection Services for OSHA Compliance?
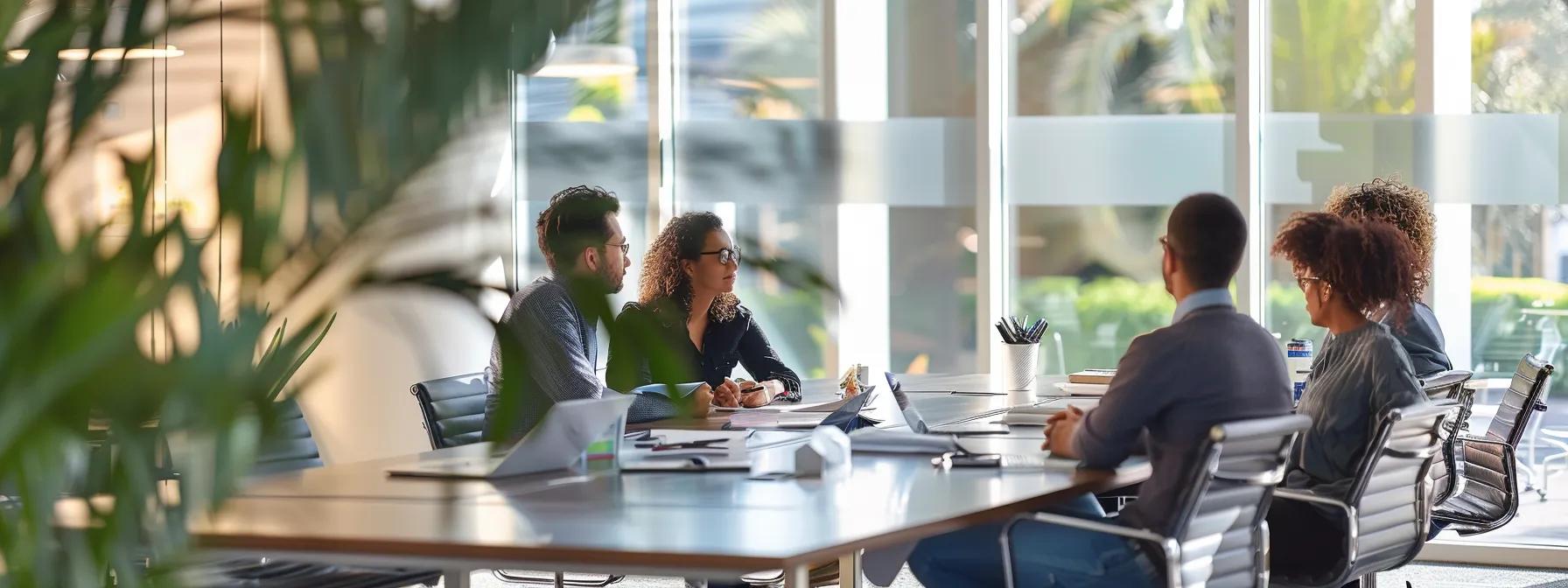
Choosing the right safety equipment, including ladder systems and lifeline systems, and inspection services is essential for OSHA compliance and worker safety. Organizations must evaluate product quality, design-installation, vendor accreditation, and service reliability to ensure that decisions align with regulatory requirements and operational needs. For more detailed insights, please visit our about-us page and check out industries-we-serve. Additionally, companies can get-a-free-quote for us fall protection services as part of their annual-maintenance routines, ensuring that guardrail systems remain state-of-the-art.
What Criteria Should Businesses Use to Select OSHA-Compliant Safety Equipment?
Businesses should evaluate safety equipment based on durability, manufacturer certifications, performance test results, and compatibility with workplace hazards. Key criteria include adherence to industry standards, ease of inspection and maintenance, and the availability of replacement parts. Total cost of ownership—including purchase price, maintenance expenses, and potential downtime—should also be considered.
Why Use Professional Inspection and Maintenance Services?
Professional services offer expert validation of equipment safety, ensuring that all components meet regulatory requirements and perform as expected under field conditions. Regular inspections by certified technicians, who stay current with OSHA guidelines, minimize risks, reduce downtime, and maintain accurate compliance documentation.
How Can Customized OSHA Compliance Solutions Meet Industry-Specific Needs?
Tailored compliance solutions address the unique hazards and operational challenges faced by different industries. Whether in manufacturing, construction, or healthcare, customized services integrate risk assessments, targeted training programs, and specialized inspection schedules to meet regulatory requirements while optimizing equipment performance and workplace safety.
What Are the Latest Updates and Trends in OSHA Safety Equipment Standards?
Recent updates in OSHA safety equipment standards reflect technological advancements, evolving industry best practices, and a heightened emphasis on worker safety. Staying informed about these changes is critical for maintaining compliance and improving operational safety.
How Have OSHA Equipment Standards Changed Recently?
Recent changes have focused on enhancing equipment durability, reliability, and performance. Updates include stricter criteria for fall protection systems, improvements in respiratory protection guidelines, and more rigorous requirements for labeling and certification of PPE. These adjustments, influenced by technology and industry feedback, help companies avoid non-compliance and maintain a safer work environment.
What Emerging Technologies Improve Safety Equipment Inspections and Maintenance?
Emerging technologies such as IoT sensors, predictive maintenance software, and mobile inspection applications are transforming safety equipment inspections. These tools allow real-time monitoring, data-driven decision making, and automated routines. For example, sensors in fall protection systems can alert supervisors to potential failures, while mobile apps facilitate prompt defect reporting and accurate documentation.
How Can Businesses Stay Informed About OSHA Compliance Changes?
Businesses can remain current by subscribing to regulatory updates, attending industry conferences, and engaging with professional safety organizations. Online resources like OSHA’s website, industry publications, and consulting services also help organizations integrate regulatory updates into internal safety practices.
Frequently Asked Questions
Q: What is OSHA compliance and why is it important?
A: OSHA compliance means meeting all safety standards set by the Occupational Safety and Health Administration to ensure a safe work environment, reduce accidents, and prevent legal penalties.
Q: How frequently should fall protection equipment be inspected?
A: Equipment should be inspected daily or before use, with detailed inspections at least annually, according to manufacturer and OSHA guidelines.
Q: What are the consequences of failing an OSHA inspection?
A: Failing an OSHA inspection can result in significant fines, legal actions, increased insurance premiums, and a heightened risk of workplace injuries.
Q: How can new technologies benefit OSHA inspections?
A: Technologies like IoT sensors and mobile inspection apps improve inspection accuracy and frequency by enabling real-time monitoring and streamline maintenance processes.
Q: Who is responsible for ensuring OSHA compliance in a workplace?
A: Employers, safety managers, and designated safety personnel are responsible for ensuring compliance, supported by proper training and regular inspections.
Q: How can customized OSHA training programs improve safety standards?
A: Customized training targets specific workplace hazards and equipment, leading to higher compliance, better hazard recognition, and improved employee safety engagement.
Final Thoughts
This article highlights the importance of adhering to OSHA safety standards for equipment inspections, maintenance, and overall operational safety. By following rigorous inspection schedules, implementing proactive maintenance practices, and investing in targeted training programs, businesses can reduce workplace hazards and ensure regulatory compliance. Keeping up with emerging technologies and industry-specific trends further strengthens safety management systems, minimizes risks, and avoids costly consequences. Ultimately, a robust safety culture not only protects employees but also enhances operational efficiency and organizational credibility.