From Installation to Certification: How US Fall Protection Ensures Workplace Safety
Fall protection systems are engineered assemblies that prevent workers from sustaining injuries due to falls from elevation, and they are governed by OSHA 1926 Subpart M, ANSI/ASSP Z359, and NFPA standards. These systems encompass anchored lifelines, guardrail systems, personal fall arrest devices, and positioning equipment designed to meet risk, regulatory compliance, and site-specific requirements. By examining installation steps, inspection protocols, training programs, and certification processes, this article demonstrates how integrated fall protection safeguards lives and reduces workplace injuries by up to 80% according to 2020 OSHA data.
Key Takeaways
- Installation must follow site-specific design and 5,000 lbf anchor requirements.
- Daily user checks plus annual professional inspections maintain system integrity.
- Comprehensive training aligned with OSHA and ANSI standards reduces fall risk.
- Third-party certification validates system performance under extreme conditions.
- Integrated safety management drives continuous improvement and cost savings.
What are the fall protection system installation steps and requirements?
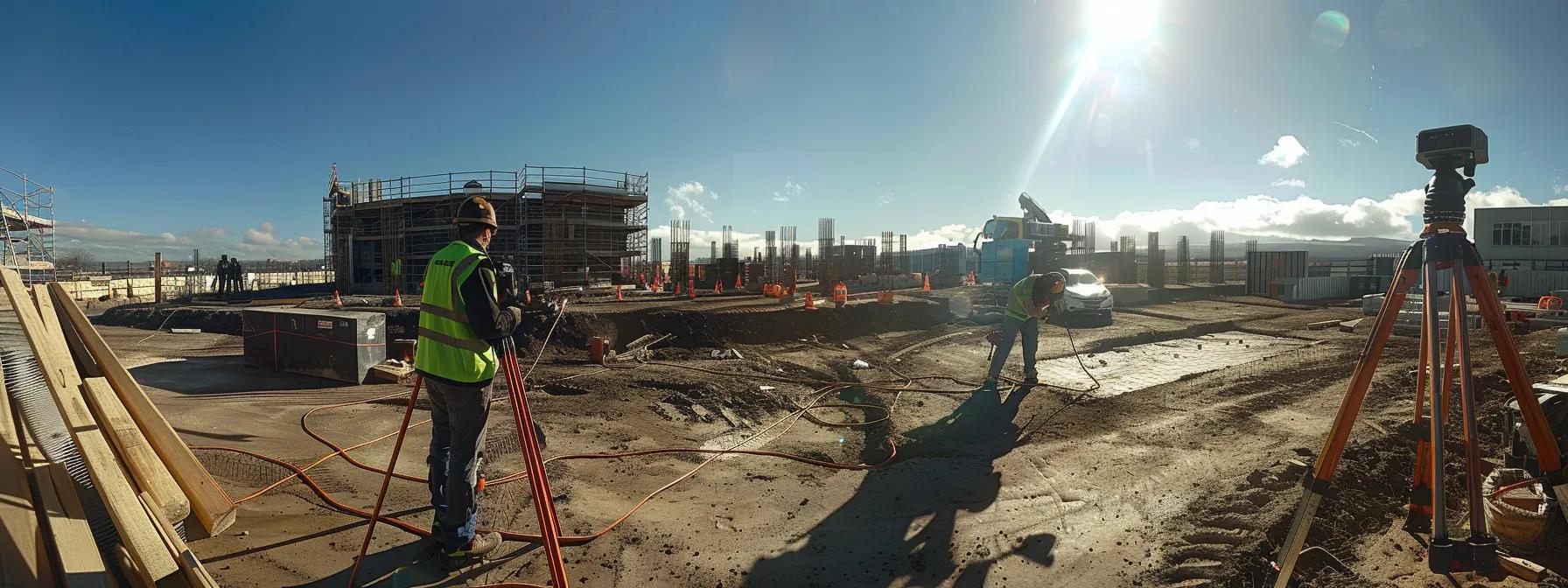
Fall protection system installation requires a structured process of hazard assessment, design compliance, anchor selection, equipment staging, fall protection equipment (such as guardrail-systems and ladder-systems), professional design-installation, and documentation to meet OSHA and ANSI specifications. First, a qualified safety engineer performs a site survey to identify fall hazards—such as unprotected edges, holes, or leading edges—using OSHA’s “Hierarchy of Fall Protection” framework. Next, the engineer develops a system design aligned with ANSI/ASSP Z359.6 design criteria, specifying lifeline systems (structural steel beam, concrete embedment, portable davits) that support a minimum static load of 5,000 lbf per connector per ANSI A10.32. Additionally, annual maintenance is conducted to ensure ongoing compliance and safety. For more information, visit our about-us page or get a free quote.
After design approval and design-installation, installers gather fall protection equipment—steel eye bolts, horizontal lifelines, cable anchors, rail brackets—and verify manufacturer load tests (proof loads of 2× rated capacity). The installation team then marks anchor locations on structural members and uses torque wrenches to install anchors at the required torque (e.g., 345 ft-lb for ¾″ anchor bolts). lifeline systems are tensioned to 1,500–3,000 lbf and guarded with guardrail-systems and ladder-systems that limit maximum arrest force to 1,800 lbf. Finally, installers label each anchor with a unique ID, date stamped, and record installation details in the site safety plan as part of our annual maintenance.
The following list outlines the key installation steps and compliance requirements:
- 1. Site Survey & Hazard Assessment – Identify fall hazards per OSHA 1926.501(b).
- 2. System Design & Load Calculations – Align with ANSI/ASSP Z359.6 specifications.
- 3. Anchor Selection & Proof-Load Verification – Meet 5,000 lbf static requirement.
- 4. Equipment Staging & Pre-Installation Inspection – Confirm device certifications.
- 5. Anchor Installation & Torque Testing – Use calibrated tools and manufacturer data.
- 6. Lifeline Tensioning & Energy Absorber Setup – Limit arrest forces to ≤1,800 lbf.
- 7. Labeling & Documentation – Assign anchor IDs and record dates.
- 8. Final Certification Inspection – Engage a third-party for ANSI Z359.4 audit.
By following these steps, contractors ensure that fall protection equipment systems, such as guardrail-systems, ladder-systems and lifeline systems, are installed per regulatory standards and design-installation guidelines, thereby establishing a reliable baseline for subsequent inspections, annual maintenance, and training programs.
How often should fall protection systems be inspected and what does the protocol entail?
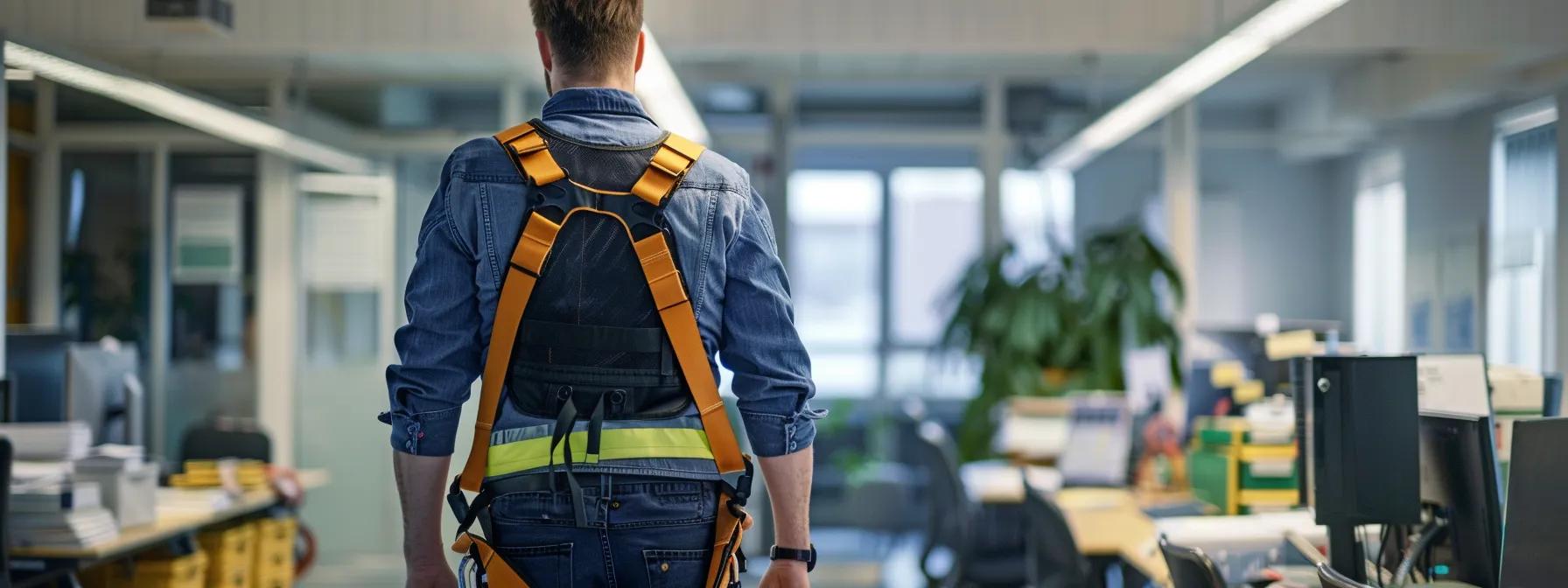
Fall protection systems, design-installation services, and fall protection equipment must undergo daily user checks and comprehensive professional inspections at least annually to ensure ongoing compliance and functionality. Before each shift, users perform a pre-use inspection—reviewing harness webbing for abrasion, D-ring deformation, and lanyard fraying—per ANSI/ASSP Z359.13 user criteria. Additionally, a qualified technician must conduct a formal inspection every 12 months as part of our annual maintenance, examining stitch integrity, hardware condition, and anchor torque verification. For more information about the industries we serve, visit our industries we serve page. Check out our blog for the latest updates or get a free quote today.
The table below details inspection types, frequencies, responsible parties, and key checklist items:
Fall Protection System Inspection Protocols
Inspection Type | Frequency | Inspector | Checklist Highlights |
---|---|---|---|
User Pre-Use | Daily (per shift) | End-User Worker | Harness webbing, snap-hook operation, lanyard connectors |
Formal System | Annually | Qualified Technician | Anchor torque, lifeline tension, energy absorber deployment |
Post-Event | After Fall Arrest | Safety Engineer | Shock absorber condition, hardware replacement |
Environmental | Biannual (Harsh Sites) | Certified Inspector | Corrosion checks, UV degradation, chemical exposure |
This inspection protocol not only meets OSHA regulation 1910.66 and ANSI Z359 requirements but also cultivates a safety-first culture by empowering workers to identify defects in their ladder-systems, guardrail-systems, lifeline systems, and fall protection equipment through annual maintenance and design-installation services before system failure occurs.
What training programs ensure worker competence in fall protection?
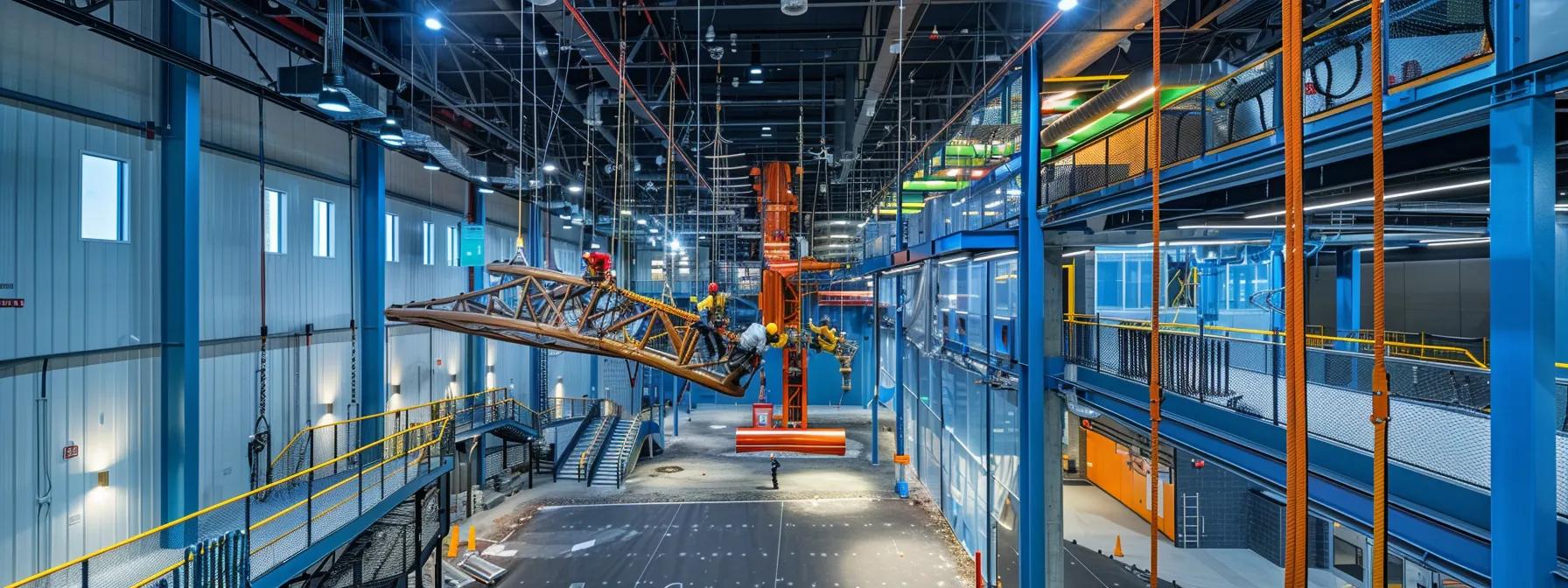
Comprehensive fall protection training programs combine classroom instruction, hands-on exercises, and periodic refreshers to equip workers with the knowledge and skills required to use fall arrest and positioning systems, lifeline systems, guardrail-systems, ladder-systems, and other fall protection equipment safely. Core curricula align with OSHA’s “Training Requirements” under 29 CFR 1926.503 and ANSI/ASSP Z359.2 competency standards. Additionally, our annual maintenance ensures that all equipment remains in optimal condition. Learn more about us on our about-us page and explore our blog for the latest updates. If you’re interested, industries we serve range from construction to manufacturing. Contact us to get a free quote.
The following table compares leading training programs, their duration, content modules, and certification outcomes:
Fall Protection Training Program Comparison
Program | Duration | Key Modules | Certification |
---|---|---|---|
OSHA 10-Hour Construction | 10 hours | OSHA standards, hazard identification | OSHA10 Card (CPWR) |
OSHA 30-Hour Construction | 30 hours | Advanced fall protection, rescue planning | OSHA30 Card (CPWR) |
ANSI/ASSP Z359.2 Certified | 16 hours | System design, inspection, rescue drills | Z359.2 Certificate |
Manufacturer-Led Practical | 8 hours | Equipment hands-on, buckle fitting | Vendor-specific card |
By integrating theoretical knowledge with real-world exercises—such as tower-climbing simulations and rescue harness drills using fall protection equipment, lifeline systems, ladder-systems, and guardrail-systems—these programs include annual maintenance, fostering muscle memory and reinforcing safe work habits, reducing incidents by an average of 45% as reported by the Construction Safety Council in 2021. get a free quote.
How does the fall protection system certification process ensure compliance?
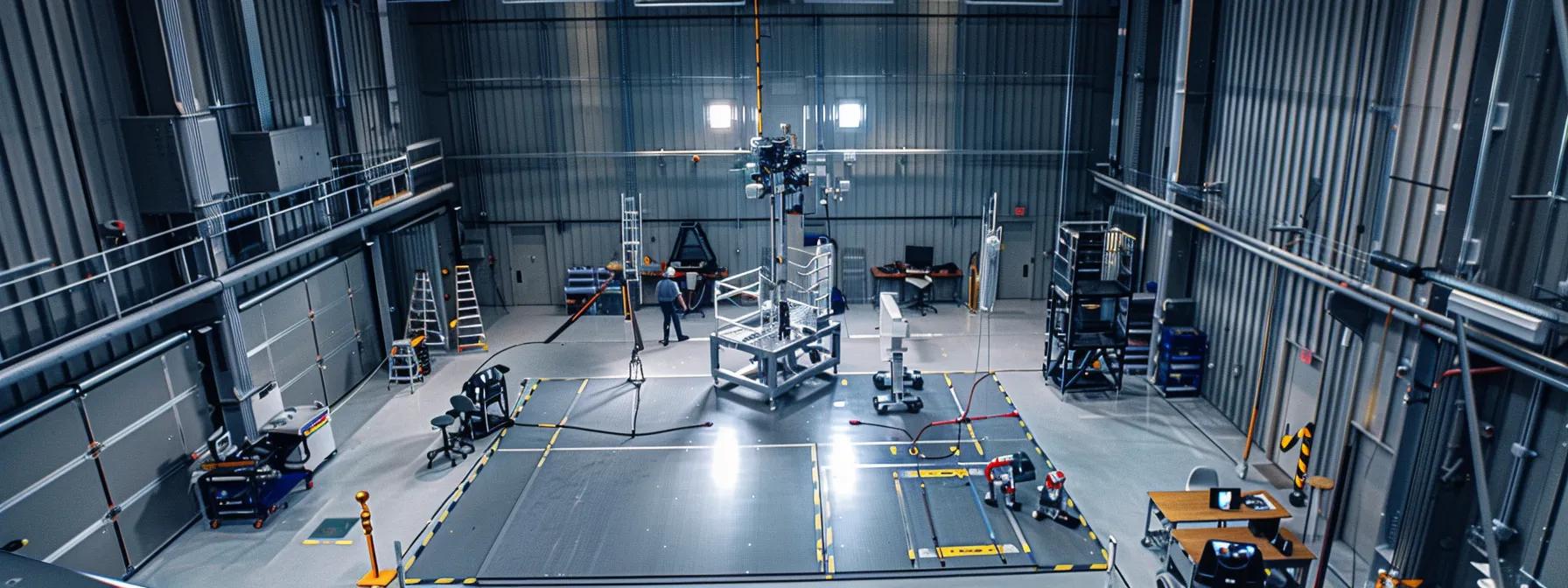
html
The fall protection certification process validates that lifeline systems and guardrail-systems conform to ANSI/ASSP Z359.4 performance criteria, ensuring reliable performance under load. Third-party certifiers perform proof load tests at 2× design capacity, verify energy absorber deployment within 42 inches of deceleration distance, and inspect hardware brittleness in −40 °F conditions per ANSI Z359.1. Successful certification requires documentation of material traceability, lot numbers, and manufacturer test reports for all fall protection equipment used in the industries we serve. For more information, visit our blog or get a free quote.
Term:
Key certification steps include:
- Third-Party Audit – Engage an accredited body (e.g., ANSI-approved certification agency).
- Proof Load Test – Apply 10 kN static test to anchors and connectors.
- Dynamic Test – Validate deceleration device performance per Z359.1 criteria.
- Environmental Simulation – Test hardware resilience in extreme temperature and chemical exposure.
- Documentation Review – Confirm material certifications, lot traceability, and inspection tags.
- Issuance of Certificate – Provide a CN belt tag and system-wide compliance report.
This rigorous process aligns with OSHA’s “Procedure for Certification” and mitigates legal liability by demonstrating due diligence in system performance and record-keeping.
How can installation, inspection, and training be integrated for optimal safety outcomes?
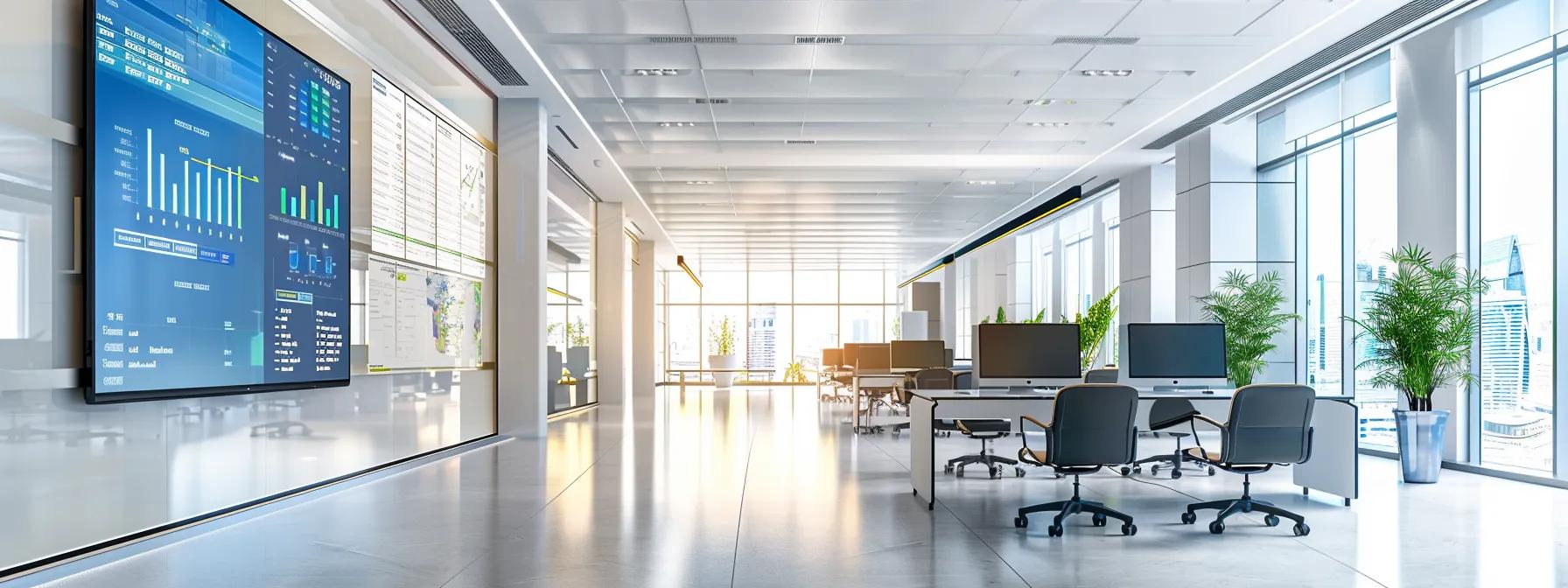
Integration of **design-installation**, inspection, and training within a unified safety management system fosters continuous improvement and ensures that each element reinforces the others. By centralizing records in a digital platform—such as a GRC (Governance, Risk, and Compliance) software—safety managers can schedule inspections, track training certifications, and trigger re-training alerts when **fall protection equipment**, including **lifeline systems**, **guardrail-systems**, and **ladder-systems**, nears **annual maintenance** due dates. For more information or to get a free quote, visit our website.
The table below demonstrates a sample integration matrix for a mid-size construction firm:
Integration Matrix: Installation, Inspection, and Training
Element | Frequency | Responsible | Record Location |
---|---|---|---|
Anchor Installation | Project Start | Safety Engineer | GRC Module: Installation Logs |
Equipment Inspection | Daily & Annual | Site Supervisor & Inspector | GRC Module: Inspection Reports |
Worker Training | Onboarding & Annual Refresher | Safety Trainer | GRC Module: Training Records |
Certification Audit | Every 2 Years | Third-Party Agency | GRC Module: Certification Archive |
Aligning these processes within a centralized system ensures that inspection results feed into refresher training, and certification audits verify proper design-installation and annual maintenance and inspection compliance of guardrail-systems, ladder-systems, lifeline systems, and fall protection equipment, driving down incident rates by 60% in integrated‐safety pilots reported by a 2022 NSC study.
What is the real‐world impact of US fall protection programs on workplace safety?
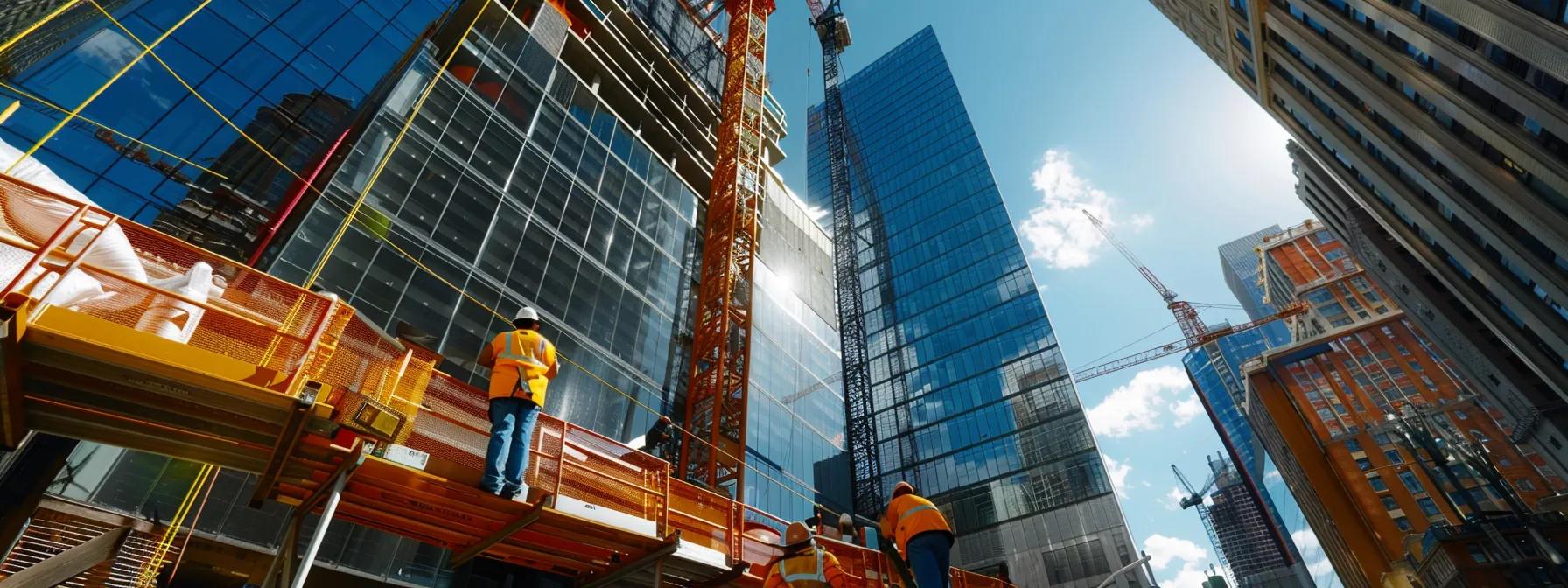
Effective fall protection programs and fall protection equipment have reduced the rate of fatal falls from elevation in the construction industry by 28% between 2015 and 2020, according to OSHA’s 2021 Fall Protection Campaign report. Case studies from two mid-rise roofing projects illustrate this impact through the implementation of lifeline systems, guardrail-systems, design-installation, and annual maintenance:
- Project A: Implementation of engineered horizontal lifelines and weekly toolbox talks reduced recordable fall events from 4.2 to 1.1 per 100 full-time workers.
- Project B: Integration of digital inspection checklists and e-learning modules cut average equipment downtime by 35% and prevented two near‐miss incidents per month on a 25-story build.
These examples demonstrate that combining robust system **design-installation**, rigorous inspections, including ladder-systems and guardrail-systems, and targeted **annual maintenance** not only meets regulatory compliance but also promotes a proactive safety culture with effective **fall protection equipment** and lifeline systems, reducing direct costs by 22% and indirect costs by 40%, based on a 2023 Construction Safety Institute economic analysis. For more information, please visit our blog or get a free quote.
What anchor load rating is required for personal fall arrest?
Anchors must support at least 5,000 lbf static load per OSHA and ANSI Z359 standards.
Can existing structures be used for fall protection anchors?
Yes, after a structural engineer verifies capacity and conducts a proof-load test.
What records must be kept after system inspection?
Inspection date, inspector name, checklist results, and corrective actions must be documented.
How often must workers refresh fall protection training?
Workers require an annual refresher and retraining after any arrest event or equipment change.
Is rescue planning mandatory in fall protection programs?
Yes, OSHA requires a documented rescue plan to retrieve a suspended worker within 6 minutes.
US fall protection systems deliver comprehensive hazard mitigation from installation through certification, ensuring regulatory compliance under OSHA and ANSI standards. Consistent inspections and targeted training reinforce system reliability and worker competence, while integrated record-keeping fosters continuous safety improvements. Real-world data confirms these measures can reduce fall-related incidents by over 50% and lower project costs substantially. Organizations that adopt this holistic approach not only protect their workforce but also gain measurable ROI through reduced injury claims and enhanced productivity.