Protecting Utility Workers: Essential Fall Protection Systems You Need
Utility and transportation workers face significant fall risks at heights, from poles and substations to loading docks and hangars. This article outlines how hazard evaluation, engineered systems, specialized solutions, rigorous training, and strategic selection combine to deliver OSHA-compliant fall protection. Readers will learn proven methods to reduce incidents, choose the right lifeline or anchor, and maintain equipment through annual audits.
Key Takeaways
- Map fall hazards by surveying all elevated work areas and task frequencies.
- Select harnesses, lanyards, and lifelines meeting ANSI Z359 and OSHA criteria.
- Use horizontal cable lifelines for roof spans and SRLs for vertical climbs.
- Deliver annual hands-on training plus daily user checks to maintain readiness.
- Apply a decision matrix comparing system attributes to job requirements.
How do you evaluate fall hazards in utility and transportation environments?
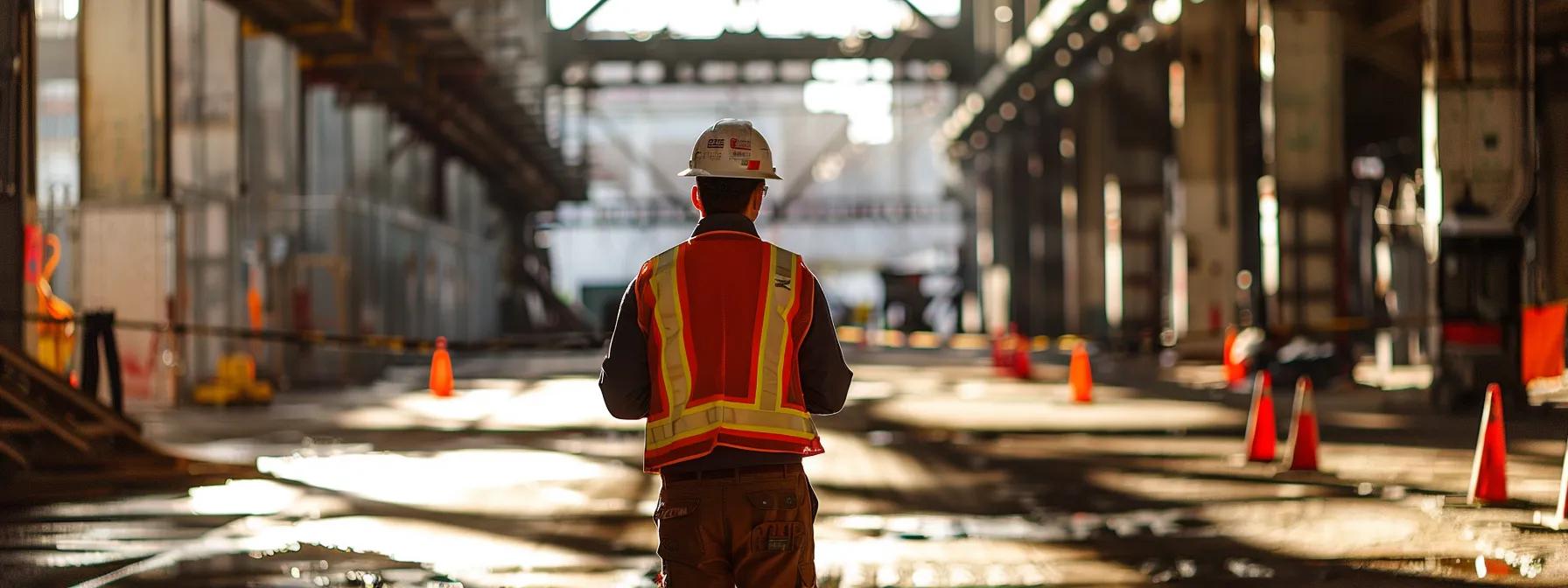
Evaluating fall hazards in utility and transportation environments, which are among the industries-we-serve, requires a systematic survey of all work locations where employees access heights and edges via ladder-systems. A formal risk assessment must catalog elevated work platforms, open penetrations in loading docks or substations, overhead crane walkways, and unguarded skylights in maintenance bays during annual maintenance. Mapping these points against task frequency, weather exposure, and worker traffic helps prioritize control measures. For more information, visit our about-us page or explore our blog. get a free quote to ensure comprehensive safety solutions.
Effective evaluation follows a three-step process: site reconnaissance to identify potential fall points; measurement of height, edge angle, and distance to obstructing equipment; and quantification of worker exposure based on job tasks such as line inspections, aircraft annual maintenance, or cargo handling. Incorporating utility pole climber studies—showing that 42% of pole-related falls occur during descent—guides focus on design-installation near ground level. Integrating incident data from transportation terminals further refines the hazard matrix, highlighting ladder-systems edges and gap risk at railcar loading areas. For more information, visit our about-us page or get a free quote.
Site surveys link directly to engineered solutions by revealing where railcar fall protection or aerial lift maintenance is most critical.
What are the core fall protection systems for utility workers?
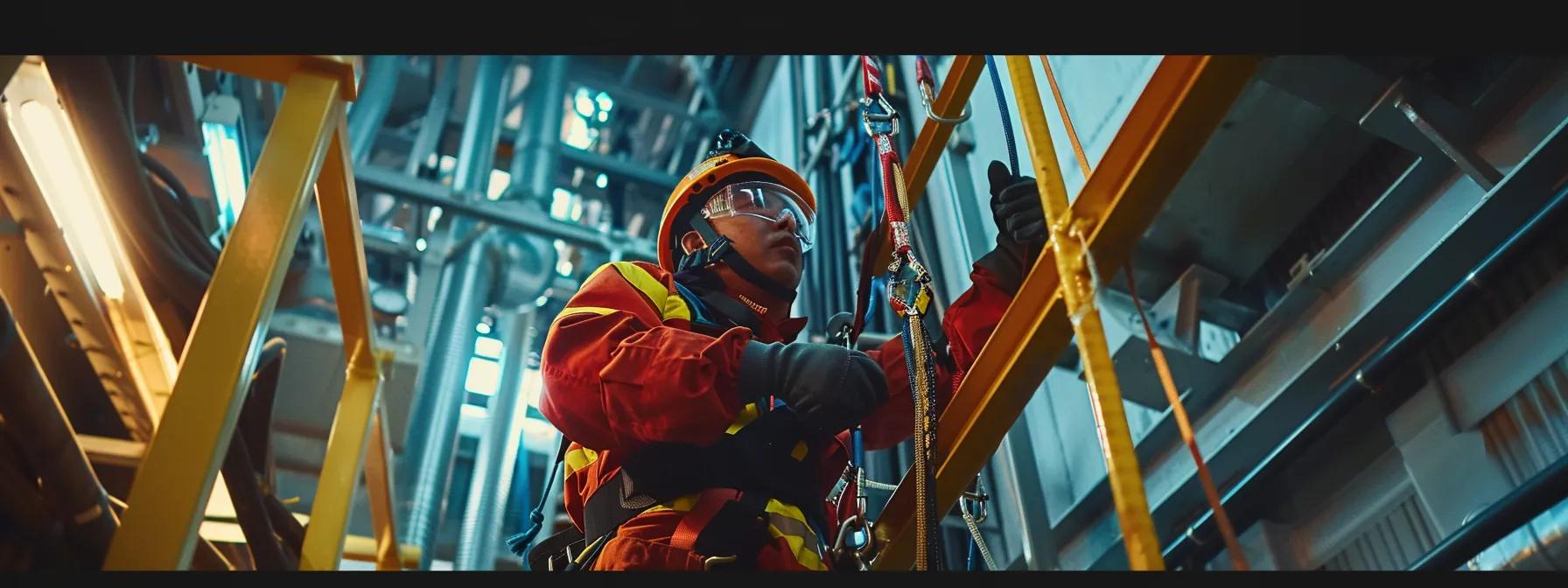
Core fall protection systems for utility workers include full-body harnesses, shock-absorbing lanyards, self-retracting lifelines, rigid lifelines, and fixed anchor points rated to 5,000 lb. Certification by the American National Standards Institute (ANSI Z359) and OSHA 29 CFR 1910.140 ensures each component meets dynamic impact load requirements. For design-installation and annual maintenance, please get a free quote. Learn more about our about-us or the industries-we-serve. Visit our blog for the latest updates. For more information, see our US fall protection resources.
Full-body harnesses distribute fall forces across thighs, pelvis, chest, and shoulders and must include a front and dorsal D-ring. Shock-absorbing lanyards limit arrest forces to under 1,800 lb at arrest, while self-retracting lifelines (SRLs) reduce fall arrest distances to under 2 ft. Rigid rail lifelines mounted on poles or substations guide climbers safely while preventing swing-fall hazards. Anchor connectors—such as horizontal beam clamps—must be installed at or above worker shoulder height to minimize free-fall distance. For more information, get a free quote on US fall protection design-installation and annual maintenance services. Visit our blog to learn more about-us and the industries-we-serve.
Properly selecting these core systems closes the gap between hazard recognition and worker protection.
What specialized fall protection measures apply to aircraft hangar environments?
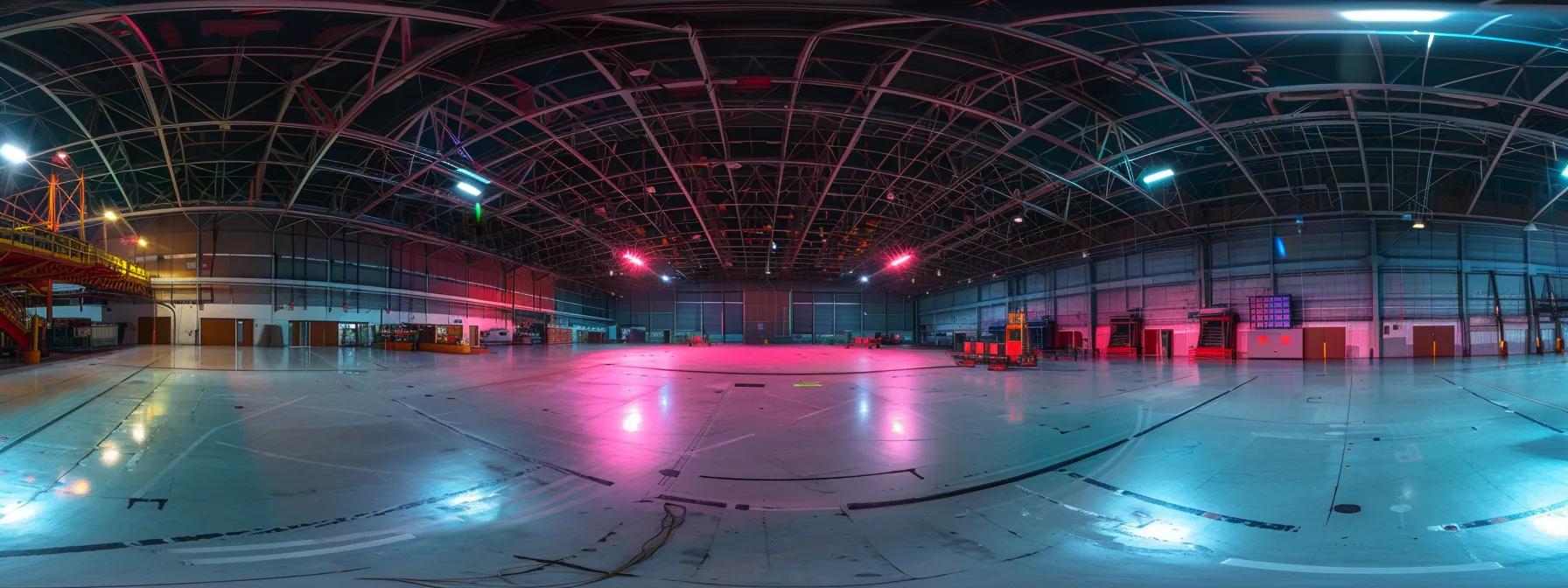
Specialized fall protection in aircraft hangar environments addresses large, flat roofs, skylights, and elevated maintenance platforms unique to aviation facilities. US fall protection around roof perimeters and removable rail guards around open skylights prevent unintentional falls into maintenance pits. Additionally, our design-installation process ensures that all guardrail systems meet industry standards, and we provide annual maintenance to uphold their effectiveness. For more information about us, visit our about-us page. Contact us to get a free quote today.
Key solutions include horizontal lifeline systems spanning the full hangar roof, compliant with NFPA 409 and OSHA’s aviation maintenance regulations. Temporary rail barriers adapt to fuselage positioning for engine overhauls, while retractable safety nets installed beneath wing-level platforms provide secondary protection during wing inspections. Aircraft-specific harness configurations often integrate tool-tether attachment points to reduce dropped object risk while maintaining fall arrest compliance. Our design-installation and annual maintenance services ensure optimal performance and safety. Visit our blog for the latest updates or get a free quote today.
Integrating aviation-grade lifeline and net systems ensures both fall arrest and debris prevention under one engineered solution.
Which fall protection measures apply in transportation facilities?
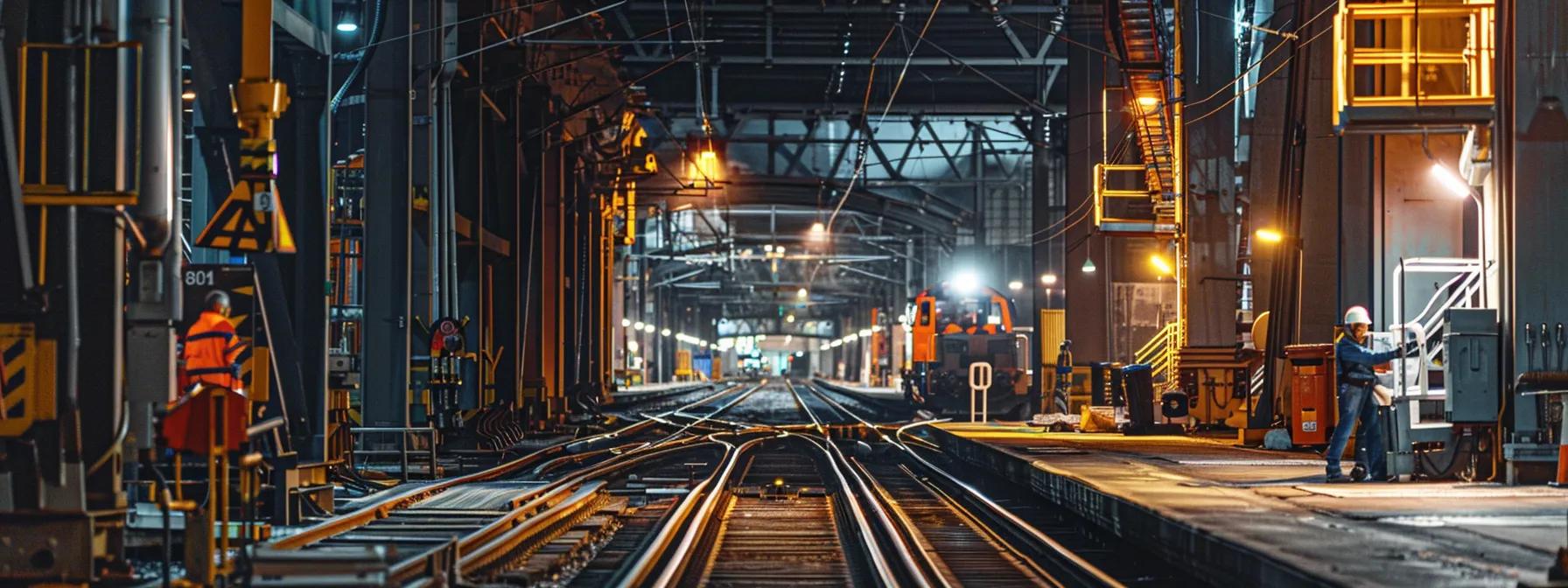
Transportation facilities—rail yards, cargo docks, bus maintenance shops, and railcar substations—require both passive and active US fall protection tailored to moving equipment and confined spaces through our design-installation services. Fixed guardrails at platform edges, safety barriers at loading docks, and warning lines on elevated maintenance walkways form the first line of defense. Regular annual maintenance ensures these safety systems remain effective. For more information, visit our blog or get a free quote today.
Active systems include retractable lifelines anchored to overhead cranes for locomotive inspections and SRLs on catenary maintenance structures for rail-line technicians, as part of our US fall protection solutions. In tunnel or trench environments, vertical lifeline kits with rope grabs facilitate safe descent and retrieval. Employers must also install wheel chocks and railcar docking locks to prevent unexpected equipment movement during height work. Inspection pits in bus garages benefit from removable bollard-mounted rails that maintain clear access when removed for vehicle ingress. For more information on our design-installation and annual maintenance services, visit our blog or get a free quote.
Term:
Combining passive rails with active lifelines mitigates both inadvertent stepping hazards and uncontrolled falls in high-traffic areas.
How should worker training and equipment inspection practices be conducted?
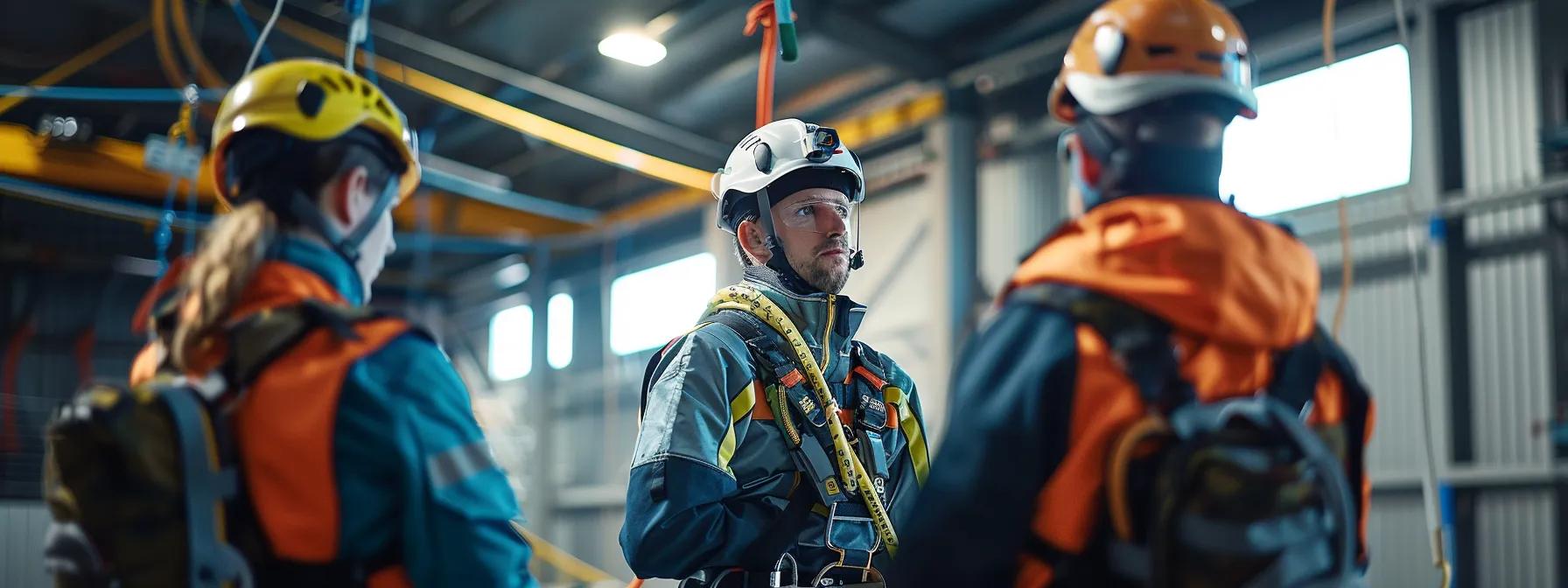
Worker training and equipment inspection practices must adhere to OSHA’s 29 CFR 1910.269(b)(2) requirements, providing annual hands-on instruction and annual maintenance, as well as daily pre-use self-checks. Training covers proper harness donning, lanyard connection sequence, anchor point selection using US fall protection, rescue planning, and hazard recognition around high‐voltage lines or moving railcars. For more insights, check our blog. If you need assistance, get a free quote today.
Inspections follow a two-tier process: a user inspection before each shift to check webbing abrasion, hardware deformation, and SRL retraction speed; and a formal annual maintenance by a qualified person, examining stitching integrity, lanyard shock pack status, and anchor connector torque values. Documented inspection tags with date, inspector initials, and next due date ensure traceability. Key training topics include emergency descent techniques, rescue hoist operation, and lockout/tagout coordination to prevent equipment energization during fall rescue drills. For more information, visit our blog or get a free quote. Learn more about-us and the industries-we-serve.
Term:
- Conduct hands-on fall rescue drills quarterly
- Implement daily user pre-shift harness checks
- Maintain inspection logs with traceable identifiers
- Review rescue and recovery procedures during each toolbox talk
Regular training and rigorous inspections keep both workers and equipment compliant and ready for safe operation.
How can strategic selection optimize fall protection systems?
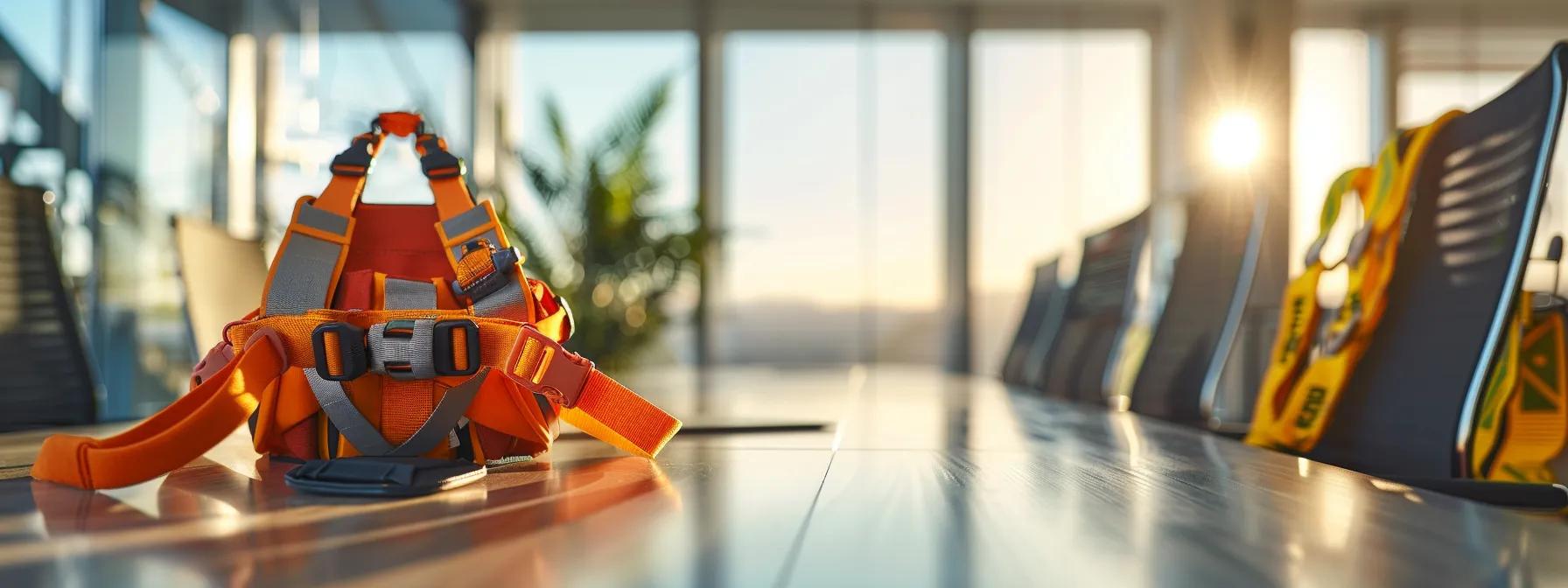
Strategic selection optimizes fall protection systems by matching system attributes—such as maximum arrest distance, anchorage capacity, ladder-systems, and mobility requirements—to specific job tasks and environments across the industries-we-serve. A decision matrix comparing lifeline types (rigid vs. SRL), harness styles, and anchor points drives evidence-based procurement, design-installation, and annual maintenance. For more insights, visit our blog or get a free quote today.
For example, SRLs offer minimal fall clearance for vertical maintenance but may restrict mobility on long horizontal runs, where cable-based horizontal lifelines excel. Full-body harnesses with integrated tool tethers reduce dropped-object incidents by 35% in high-traffic substations, according to a 2022 utility safety journal. Visit our blog for more insights. Table 1 below summarizes key system comparisons to guide facility managers in selecting the optimal combination for pole-top work, railcar inspection, and hangar roof maintenance. For more information on design-installation and annual maintenance, get a free quote by contacting US fall protection.
Using a comparative framework ensures alignment with regulatory compliance and enhances worker acceptance.
What is the maximum arrest distance for a shock-absorbing lanyard?
Maximum arrest distance is typically under 6 ft when using a 42 in. lanyard with 3.5 ft deceleration.
How often must lifelines undergo formal inspection?
Formal inspection by a qualified person is required at least annually per ANSI Z359.1 standards.
Can horizontal lifelines be used on sloped roofs?
Yes, when installed with appropriate intermediate support and designed for slope angles up to 30°.
What training duration is mandated for fall protection?
OSHA requires initial and annual retraining, with a minimum of 8 hours for new entrants.
How do you choose an anchor point for aerial lift use?
Anchors must support 5,000 lb or twice the intended load, positioned overhead to minimize free-fall distance.
Effective fall protection for utility and transportation workers combines detailed hazard evaluation with engineered systems and specialized solutions. Integrating rigorous training and standardized inspections ensures equipment reliability and worker competence. Strategic selection based on task analysis and incident data maximizes both safety and productivity. Implementing these measures fosters a compliant safety culture and reduces lost-time injuries.