Certified and Safe: How Equipment Inspections and Training Ensure Worksite Compliance and Safety
Ensuring worksite safety and compliance requires a multi-pronged approach that encompasses equipment inspections (including annual-maintenance reviews), rigorous training programs (enhanced by ladder-systems), and certification services. In today’s fast-paced industrial environments—with increasing regulatory demands and higher risks of occupational injuries—companies are prioritizing systems, such as us fall protection, that not only protect employees but also secure their reputation and operational efficiency. This article provides insights into the benefits of equipment inspections (for example, anchor text: guardrail systems), the impact of safety training on compliance, the role of certification services, and how these elements integrate to create safer work environments.
What Are the Key Benefits of Equipment Inspections for Worksite Safety?
Equipment inspections are crucial in identifying hazards before accidents occur. Early detection of wear and tear leads to prompt repairs or replacements and supports annual-maintenance strategies. Regular inspections also ensure compliance with industry standards and regulatory mandates, keeping safety protocols up-to-date, especially for ladder-systems. A structured inspection schedule minimizes the risk of equipment failure and reduces downtime. For example, thorough inspections of fall protection systems, including harnesses, lanyards, and anchor text: guardrail systems, help lower the occurrence of falls.
How Do Fall Protection Equipment Inspections Prevent Accidents?
Regular inspections reveal defects, degradation, or damage that could lead to catastrophic failures. By assessing the integrity of anchorage points, lifelines, and safety harnesses, and evaluating anchor text: guardrail systems and lifeline-systems, inspections ensure all components meet safety standards in line with annual-maintenance protocols. This proactive measure removes faulty equipment from service, reducing the likelihood of falls and enhancing us fall protection. In practice, robust inspection routines can reduce fall incidents significantly.
What Standards and Regulations Govern Equipment Inspections?
A range of standards, including those set by OSHA, ISO, and ANSI, govern worksite equipment inspections in industries-we-serve. These standards specify inspection frequency, testing procedures, and documentation requirements often incorporated into annual-maintenance schedules. Organizations that adhere to these guidelines reduce compliance issues and avoid fines. For example, OSHA requires fall protection systems, such as us fall protection, to be inspected before each use and at regular intervals by a competent person.
How Often Should Safety Equipment Be Inspected?
Safety equipment should be inspected at least monthly, with more frequent checks in high-risk environments. For industries-we-serve that handle critical systems, routine annual-maintenance checks are essential. Daily pre-use checks for items prone to rapid deterioration, such as harnesses, lifeline-systems, or lanyards in extreme conditions, are recommended. Industries with heavy machinery may conduct weekly or monthly audits, and automated systems can flag abnormalities in real time to ensure adherence to safety protocols.
How Does Safety Training Improve Compliance on Worksites?
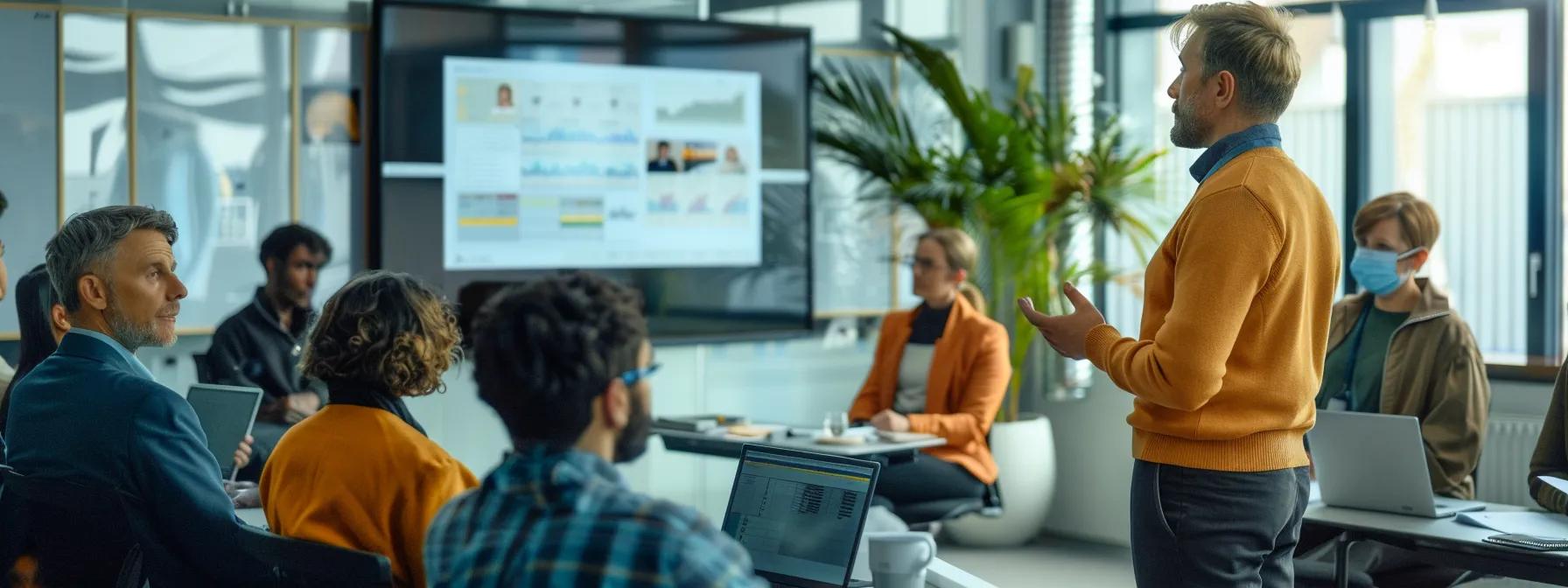
Safety training improves compliance by educating employees on proper procedures and correct use of personal protective equipment (PPE) such as anchor text: guardrail systems and us fall protection. Effective training helps workers internalize safety protocols, reducing accidents significantly while stressing the importance of annual-maintenance. Training also fosters accountability, with insights shared on our blog that highlight best practices across industries-we-serve.
What Topics Are Covered in Effective Safety Training Programs?
Effective safety training covers hazard recognition, emergency response, proper use of safety equipment (such as ladder-systems and us fall protection), and compliance with regulatory guidelines (including annual-maintenance checks). Sessions include practical demonstrations and hands-on exercises—for example, live demonstrations on harness fitting and rescue techniques incorporating lifeline-systems—to ensure employees are well-prepared for both routine operations and emergencies.
How Does Hands-on Training Enhance Worker Safety?
Hands-on training reinforces classroom learning by simulating real-life emergency scenarios. For instance, incorporating us fall protection and lifeline-systems into simulations prepares teams for real hazards. This practice builds muscle memory and improves decision-making under stress, which is critical during emergencies—especially when undertaking design installation projects where ladder-systems play an essential role. Interactive sessions also promote continuous learning, allowing employees to share experiences that refine safety protocols, such as through the implementation of anchor text: guardrail systems.
Who Should Conduct Certified Safety Training?
Certified safety training should be led by professionals backed by credentials from organizations such as osha, the National Safety Council, or the International Institute of Risk and Safety Management. Serving industries-we-serve with expertise in design installation and annual-maintenance, these experts combine in-depth safety knowledge with practical field experience that includes the proper use of ladder-systems and lifeline-systems, ensuring that us fall protection protocols are met and that the training remains compliant with evolving regulations.
What Certification Services Support Worksite Safety and Compliance?
Certification services offer formal verification that a worksite meets industry best practices and standards set by organizations like OSHA, ISO, and ANSI. For detailed information, please visit our industries-we-serve page and about us section, which highlight our rigorous standards and commitment to safety. Certification provides external validation that helps companies avoid legal penalties and operational interruptions—many companies even get a free quote for their annual-maintenance needs. In competitive markets, certified safety practices enhance an organization’s credibility and reliability. For further insights and updates on safety innovations, visit our blog.
How Do Safety System Certification Services Help Meet OSHA Requirements?
Certification services align operations with OSHA requirements through comprehensive audits and assessments. These audits confirm that safety protocols are followed and corrective measures are promptly implemented, minimizing risks and regulatory penalties. For instance, a certified review of confined space rescue plans may reveal non-compliant elements, allowing companies to adjust practices before an OSHA inspection.
What Are Industry-Specific Safety Certifications and Their Benefits?
Industry-specific certifications address the unique risks in sectors such as construction, manufacturing, healthcare, and laboratories. Certifications like ISO 45001 and NFPA standards provide guidelines tailored to each industry’s challenges, fostering a proactive safety culture, reducing accident rates, and potentially lowering insurance premiums. Companies with these certifications usually enjoy enhanced market reputation and customer confidence.
How Can Companies Maintain and Renew Safety Certifications?
Maintaining certifications involves periodic audits and continuous training to meet evolving standards. Companies should regularly review new risks, update safety procedures, and document corrective actions. Investments in digital inspection logs and automated compliance tracking further ensure that certifications remain valid. Partnerships with accredited bodies also help companies stay informed of regulatory changes.
How Do Equipment Inspections and Training Work Together to Keep Worksites Compliant?
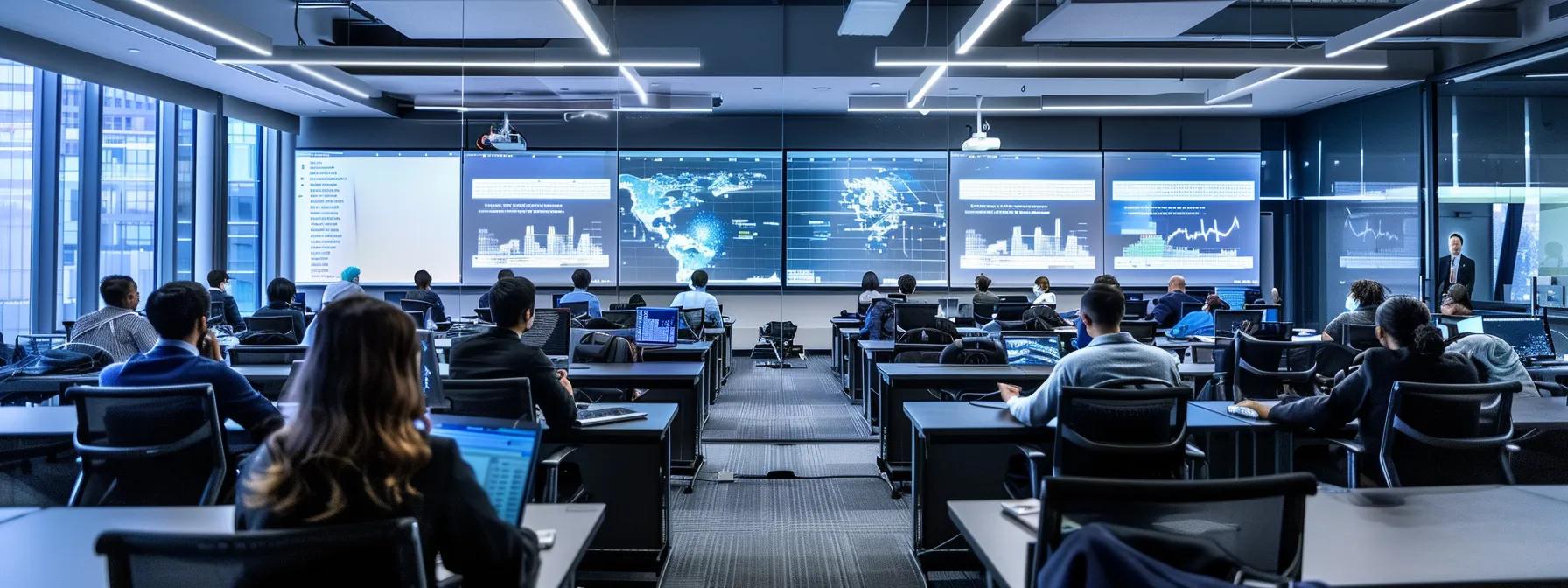
Combining equipment inspections with employee training creates a synergistic strategy that enhances worksite safety and compliance. Regular inspections identify potential hazards while targeted training equips employees to respond safely. This integrated approach not only lowers accident risks but also improves overall operational efficiency.
What Is the Role of Proactive Safety Programs in Compliance?
Proactive safety programs anticipate hazards and implement preventive measures before incidents occur. These programs depend on timely inspection data and continuous improvements in training methods. By identifying weak points and integrating lessons from past incidents, proactive programs maintain high levels of preparedness and prevent unnecessary downtime.
How Does Combining Inspections With Training Reduce Workplace Risks?
Integrating equipment inspections with robust training minimizes both mechanical failures and human errors. While inspections detect technical issues, training ensures employees operate equipment safely and respond correctly during emergencies. This dual approach addresses the technological and human factors behind workplace accidents, significantly reducing risk.
What Are the Common Challenges in Implementing Safety Inspections and Training?
Implementing comprehensive safety inspections and training programs can be challenging due to employee resistance and high implementation costs. New protocols may be seen as disruptive, and recurring expenses for inspections, training sessions, and certifying renewals can be significant. Overcoming these barriers requires clear communication and effective change management.
How Can Worksites Overcome Resistance to Safety Protocols?
Involving employees in the development of safety procedures can reduce resistance. Participation in safety committees or providing feedback during training helps workers accept changes. Clear communication of the benefits—such as fewer injuries and improved operational uptime—and incentives for safety excellence further encourage adoption of new protocols.
What Are the Costs and ROI of Safety Inspections and Training?
Although the initial costs of safety inspections and training are considerable, the long-term return on investment can be substantial. Preventing even one major accident can save significant expenses in legal fees, downtime, and lost productivity. Many companies report an ROI of 3:1 or higher, while lower insurance premiums further offset costs.
How Can Customized Safety Solutions Enhance Worksite Compliance?
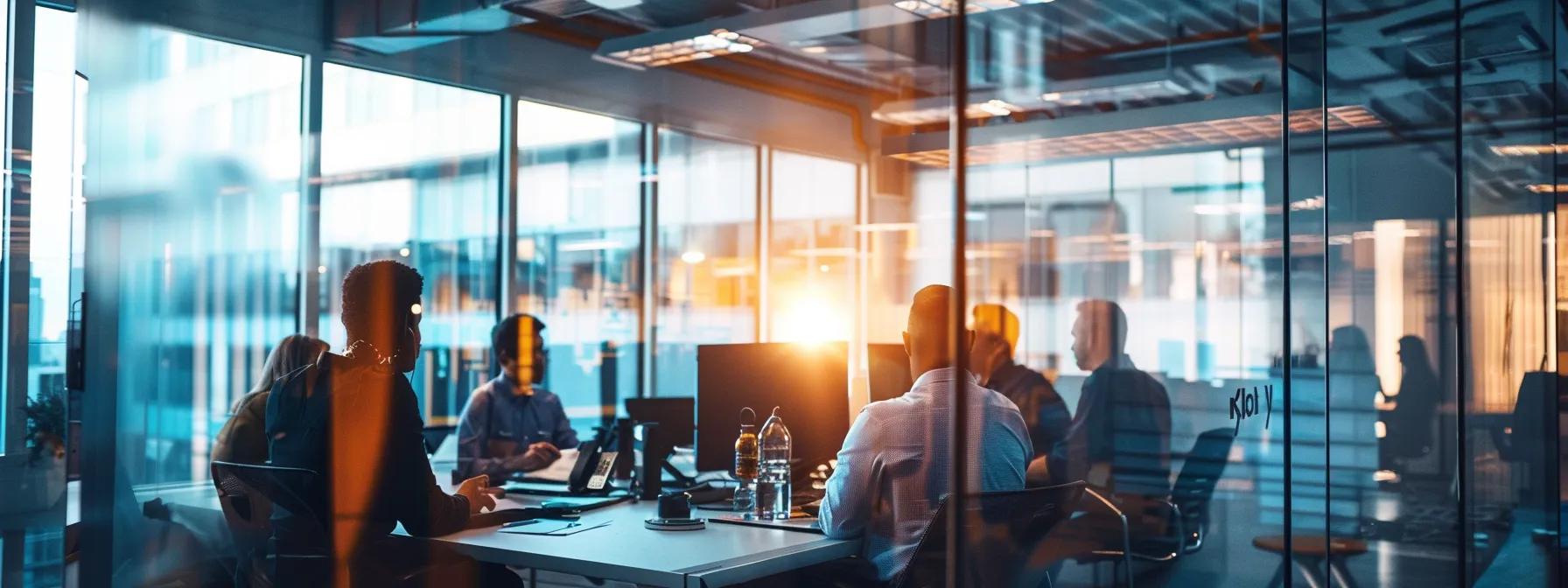
Customized safety solutions are designed to meet the unique needs of individual worksites and industries. Tailoring both safety training and equipment inspections to the specific operational risks leads to more effective prevention strategies, improved compliance, and sustained operational efficiency. This personalized approach also boosts worker confidence.
What Factors Determine the Best Safety Training for Different Industries?
The best training approach depends on the nature of the work, associated risks, and existing safety culture. Factors include the type of equipment used, past accident data, and regulatory requirements. For example, construction sites may need specialized training in fall protection and confined space rescue, while healthcare facilities might focus on infection control and emergency response.
How Are Equipment Inspections Adapted to Unique Worksite Conditions?
Adapting inspections to specific worksite conditions involves specialized tools and methods that consider environmental exposure, operational stress, and equipment type. In outdoor settings, advanced non-destructive testing methods may detect early signs of corrosion, while indoor environments may use digital monitoring systems for real-time equipment tracking. Customized protocols and data analytics help ensure continuous compliance.
What Are the Latest Trends in Safety Equipment Inspections and Training?
Advancements in technology and innovative training methodologies are rapidly transforming safety inspections and training. Emerging trends include the use of AI and machine learning for predictive maintenance, alongside virtual and augmented reality for immersive training experiences. These technologies improve inspection accuracy and enhance worker engagement.
How Is Technology Improving Equipment Inspection Accuracy?
New technologies such as sensors, drones, and AI-enabled analytics have revolutionized equipment inspections. High-resolution cameras and thermal imaging sensors can detect minute structural weaknesses that might be missed in routine checks. Machine learning algorithms also analyze inspection data to predict maintenance needs, reducing downtime and improving safety compliance.
What New Training Methods Are Increasing Worker Engagement?
Innovative methods like VR simulations, gamified learning modules, and interactive e-learning platforms are changing safety training. These techniques allow workers to experience simulated hazards and practice responses in a controlled environment. Mobile-friendly training also ensures that employees can update their knowledge anytime, leading to higher engagement and better retention.
Frequently Asked Questions
Q: What are the immediate benefits of regular equipment inspections?
A: Regular inspections identify safety hazards and defects, enabling proactive maintenance, reducing downtime, and ensuring compliance with industry standards.
Q: In what ways do fall protection equipment inspections reduce workplace injuries?
A: Inspections verify that all fall protection components are functional and meet safety standards, reducing the risk of falls through early detection and timely replacements.
Q: How does combining safety training with inspections create a safer worksite?
A: Integrating training with regular inspections ensures employees are aware of hazards and equipped with the skills to handle emergencies, thus reducing human error and preventing accidents.
Q: What role do certification services play in worksite safety?
A: Certification services validate that a company’s safety management systems meet recognized standards, enhancing regulatory compliance and bolstering credibility.
Q: How can emerging technology impact the safety training process?
A: Technologies such as VR and AI analytics provide immersive training experiences and improve hazard detection during inspections, leading to better engagement and retention of safety information.
Q: What are the cost implications of implementing comprehensive safety inspections and training programs?
A: While initial costs may be high, the long-term savings from reduced accident rates, fewer penalties, lower downtime, and decreased insurance premiums offer a significant return on investment.
Q: Why is it important to customize safety solutions for different industries?
A: Customization aligns safety protocols with the specific risks of each industry, leading to more effective prevention strategies and improved compliance rates.
Q: What benefits do digital monitoring systems offer in equipment inspections?
A: Digital monitoring systems provide real-time data, enabling early detection of issues, predictive maintenance scheduling, and a reduction in unexpected equipment failures.
Final Thoughts
Worksite safety and compliance are essential for maintaining operational efficiency and protecting employees from injury. Integrating regular equipment inspections with comprehensive safety training and certification services creates a robust framework that prevents accidents and meets regulatory demands. Advances in technology improve both inspection accuracy and training engagement, supporting a proactive, dynamic approach to risk management. As companies invest in customized safety solutions, the future of worksite compliance looks more secure and sustainable, fostering a culture of continuous improvement and heightened risk awareness.